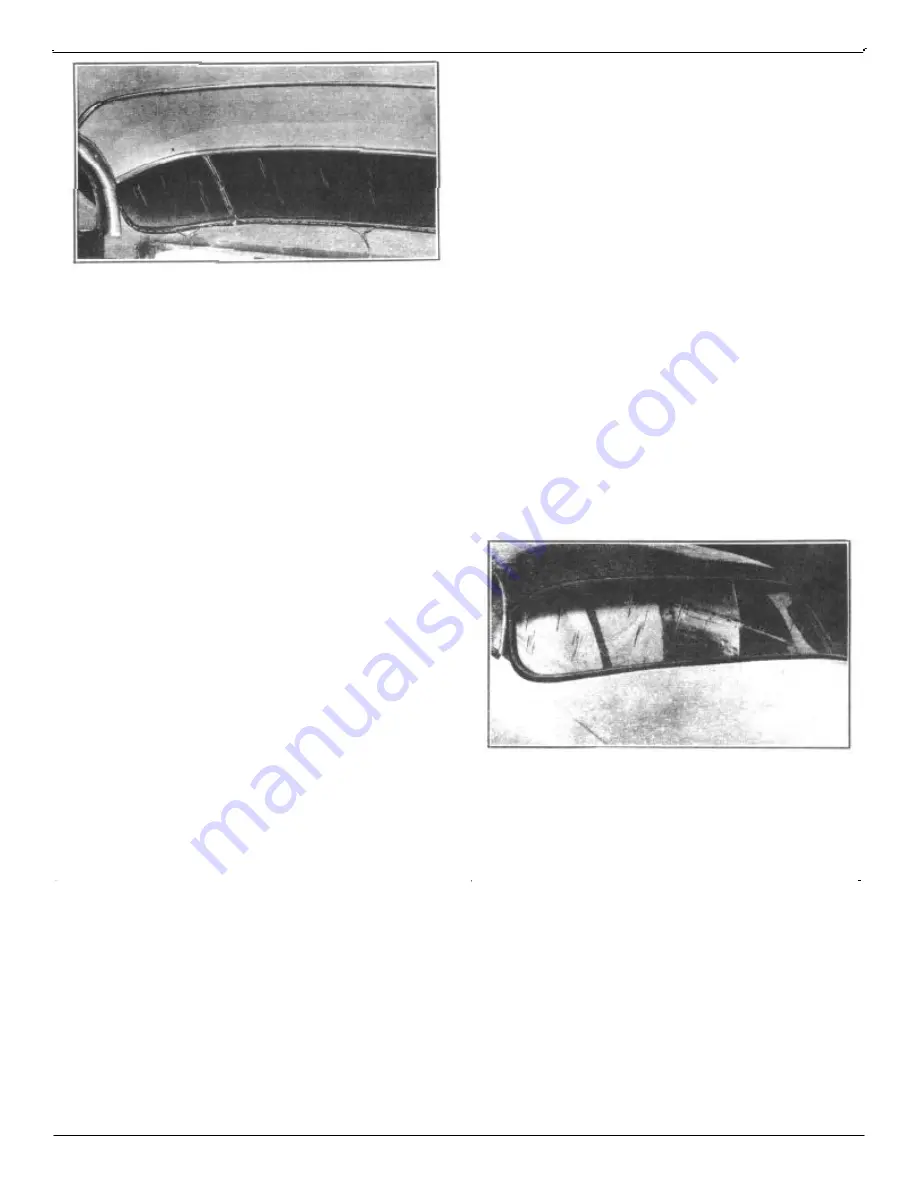
FIGURE 198
side body rubber lip and lip of recess, Figure 198). Tie
cords tightly enough to draw the inner edges of the rubber
channel within the limits of the rear window sections.
Leave sufficient cord to provide a good hand hold to pull
the cords, tape loose ends to window glass (to inside).
3. Place a protective cloth over the rear seat back and pack-
age shelf.
4. Apply liquid soap on the inside of the large lip (inner lip)
of the rubber weatherstrip.
5. With one man inside the car and one man on each side of
the car (outside of car), position the glass and weatherstrip
so that inside lip of weatherstrip is over the lip of the
bottom flange in rear window opening, and that the win-
dow is evenly spaced over the rear window opening.
NOTE: If the glass and weatherstrip is not properly posi-
tioned before the release cords are pulled, it will be neces-
sary to remove the assembly and perform operations 2, 4
and 5 again.
6. With the two helpers firmly pressing inward and down-
ward on the glass and weatherstrip assembly and the
assembly properly positioned in rear window opening,
pull the center release cord slowly and carefully so that the
lip of the weatherstrip is raised sufficiently to allow the
weatherstrip to seat properly in the body recess.
7. After seating the center section, release the cord on the left
hand section, working the inner lip of the weatherstrip
over the body flange, using your fingers to pull and posi-
tion the rubber while the helpers steadily push and strike
the window with the palm of the hand immediately over
the area being worked. Apply additional liquid soap as
required to facilitate the installation.
8. After the center and left sections have been properly
positioned, proceed to the right hand side, proceeding as
in paragraph 7 above.
NOTE: When performing the above operation the glass
must be forced into position by blows with a soft rubber
mallet or with the palm of the hand. Recheck to see that
the outside lip of rubber is spaced evenly around rear
window opening (reposition as necessary).
CAUTION: Do Not Scratch the Glass.
9. Remove the masking tape from window and weatherstrip
and install the rear window inner and outer vertical
mouldings.
10. Install Part No. 228715 Sealing Tape 1/8" thick, 1/2"
wide over groove, between weatherstrip and outside
body recess completely around the window in a uniform
thickness, Figure 199.
11. Install the upper and lower moulding retainers over the sealing
tape and weatherstrip. Place a small wad of Permagum under
the moulding retainers at the area of the screw holes. Draw the
screws down carefully and evenly to spread the sealer uniformly
and to avoid distorting the moulding retainers.
FIGURE 199
12. Install the roof panel quarter mouldings, (4), Figure 196, the
upper mouldings outer (3) and lower rear belt mouldings (1).
NOTE: When installing the finish mouldings work from
the ends to the center to avoid damaging the mouldings.
133 BODY MANUAL
Summary of Contents for 1948 Commodore
Page 1: ......
Page 2: ...This manual courtesy of Hudson Essex Terraplane Club member Drew Meyer...
Page 45: ...BODY MANUAL 40 MODELS 1948 1949 FIGURE 78...
Page 46: ...41 BODY MANUAL MODELS 1950 FIGURE 79...
Page 47: ...BODY MANUAL 42 MODELS 1951 FIGURE 80...
Page 48: ...43 BODY MANUAL MODELS 1952 FIGURE 81...
Page 49: ...BODY MANUAL 44 MODELS 1953 EXCEPT 1C AND 2C FIGURE 82...
Page 50: ...45 BODY MANUAL MODELS 1953 1954 1C 1D 2C 2D AND 3D FIGURE 83...
Page 51: ...BODY MANUAL 46 MODELS 1954 4D 5D AND 7D FIGURE 83...
Page 84: ...79 BODY MANUAL MODELS 1948 1949 FIGURE 13...
Page 85: ...BODY MANUAL 80 FIGURE 114...
Page 86: ...81 BODY MANUAL Figure 115...
Page 89: ...BODY MANUAL 84 FIGURE 117 FIGURE 118 FIGURE 119...
Page 126: ...121 BODY MANUAL ALL CONVERTIBLE MODELS 1954 FIGURE 189...
Page 143: ...REFERENCE Source of Information Date Subject...
Page 144: ...REFERENCE Source of Information Date Subject...
Page 145: ...REFERENCE Source of Information Date Subject...
Page 146: ...REFERENCE Source of Information Date Subject...
Page 147: ......