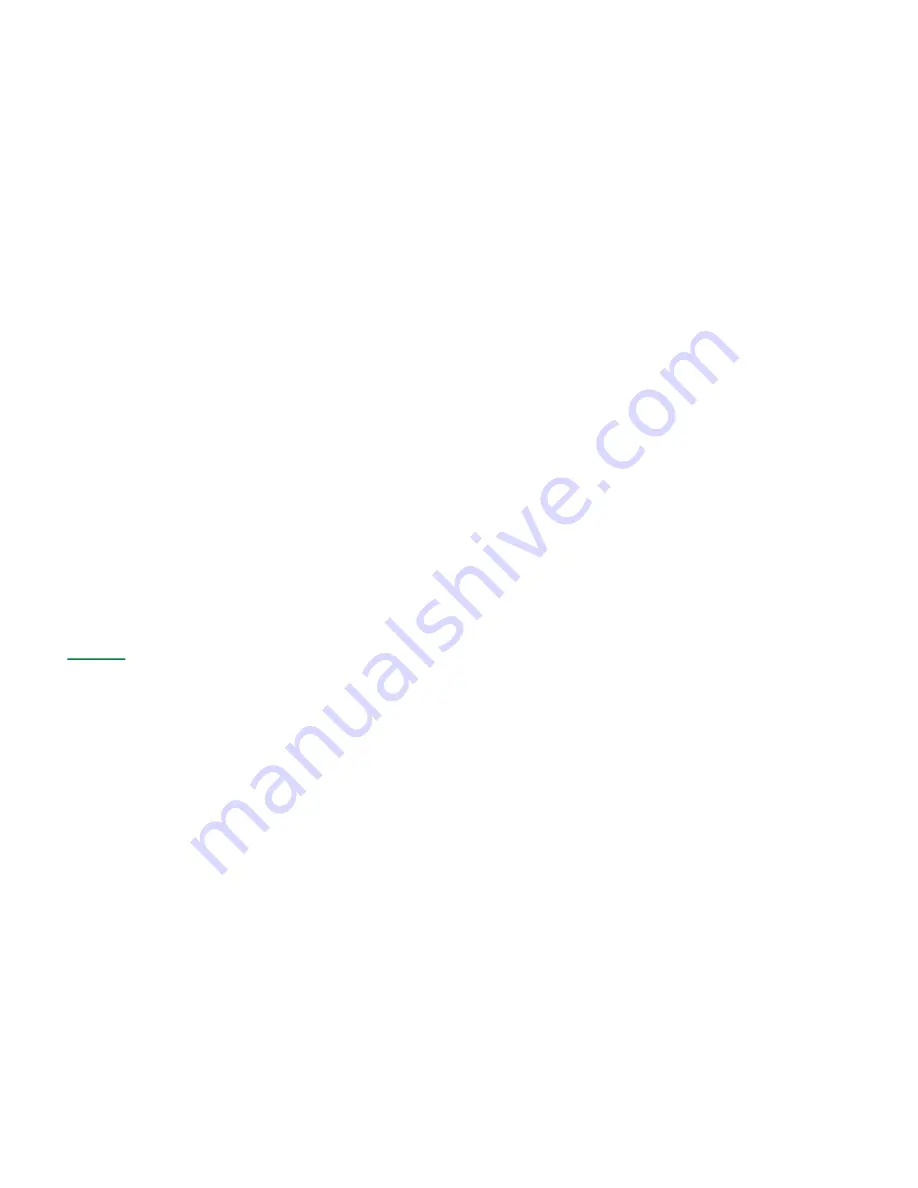
12
25 and then work your way up in increments of five or ten until the ball at the end of the wire is cut off when you stop
welding. More pinch than that is not necessary. The harder the wire is and the larger the diameter, the more pinch you
will need). Pinch for any size steel wire, and for 3/64” 5554 aluminum alloy wire, is usually set at 100.
Note: If you purchased a remote control for you MIG, spool, or push/pull gun, the following is only of limited
interest to you as you can adjust your weld parameters WHILE welding at any time! So, essentially, you can
make your own hot start, slope down, and final current at any time to suit your needs.
To fill the crater at the end of the weld, the slope down (t2) may be set (a slope down time between 2.5 and 4 seconds
should suffice, but again, this number depends on material thickness and type of filler wire).
Everybody knows that aluminum is supposed to be preheated before welding. There are a few situations in which
preheating the material is not possible, practical, or safe. If you choose not to preheat the part(s) that you are welding,
for whatever reason, there is a hot start function built into the Pro Pulse 220 MTS that will reduce the effects of
starting an aluminum MIG weld on a cold part.
The hot start function will boost the welding current by about 35% above the selected settings. As the chosen settings
reach 200 amps, that boost will be reduced because the machine is only capable of putting out 220 amps for a very
short period of time. There are two ways to access hot start:
1. Through time (0.2 to 4 seconds) that can be pre-selected in the MIG 2T mode Start Menu:
a. Set the start speed to 100% and the start time to 0.1 seconds for no hot start. This will give you 0.2 seconds
of hot start time, but, in reality, that is the time it takes to ignite the arc so you will not notice any hot start.
b. Set the time to 2 seconds to get 4 seconds of hot start time. During the first 2 seconds, you will get 35% hot
start, the following 2 seconds (seconds 3 and 4) you will get hot start tapering down from +35% to the
selected welding current.
2. Fully controlled by you with no time limit (as needed) through trigger motion in MIG 4T mode:
a. Pull and hold the trigger; 35% added hot start in addition to the selected welding settings.
b. Let go of the trigger; the selected settings are being run, the arc stays lit, and welding is in progress.
c. Pull and hold the trigger; the machine initiates the slope down sequence and fills the crater at the end of the
weld. Once the slope down timer runs out, the welding current stops automatically
d. Let go of the trigger; welding completed and gas flow stopped.
Pro Tip:
During hot start, slope down, or final current, there is no double pulse. If double pulse is desired during
hot start or slope down, please use a remote control (sliders on MIG guns and spool guns or potentiometers on
push/pull guns) to achieve the desired effect manually.
Note: The 4T trigger was reprogrammed in the aluminum programs.
The material thickness settings in the display are approximate, especially when welding aluminum. When welding
aluminum, the values change with the temperature or with the material welded. If the material is cold, the chosen
material thickness in the display may have to be a little higher than the actual material thickness. When the material is
preheated properly or has been welded on for a while, then the thickness in the display needs to be lower or a lot
lower than the actual material thickness. Therefore, you have the ability to adjust the material thickness (which will
adjust the wire speed and the voltage at the same time), while welding, by turning the upper encoder counter-
clockwise.
Because this is not always practical while welding, there is a second way to control the heat input. For instance, if the
machine is in MIG 2T and the slope down time is set, for example, anywhere between 3 and 6 seconds, you have the
option, if you notice that the weld is getting too hot, to let go of the trigger. Laying off the trigger lets the machine go
into slope down, causing the welding current to taper gradually. Just before the machine turns off, depress the trigger
again, though only for a very short time, and then lay off the trigger again, allowing the process to repeat. Doing this
allows you to fill in gaps and/or manually compensate for a too hot setting or the material heating up.
Summary of Contents for Pro Pulse 220 MTS
Page 5: ...5 Fig 1...
Page 13: ...13 Fig 3...
Page 26: ...26 Pro Pulse 220 MTS Wiring Diagram...