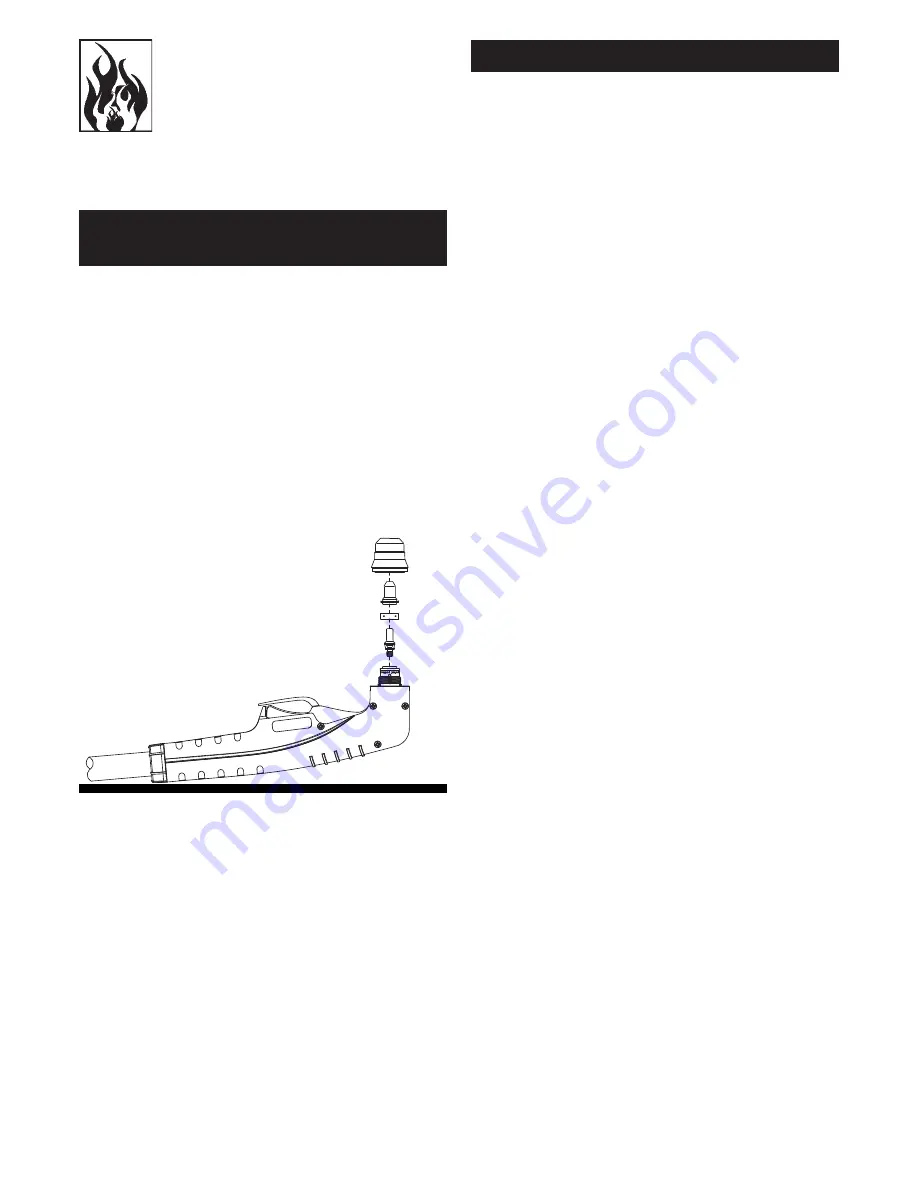
13
WORK
TABLE
SHIELD CUP
CUTTING TIP
SWIRL RING
ELECTRODE
TORCH HEAD
ASSEMBLY
Figure 7 PLASMA TORCH CONSUMABLE PARTS
TORCH CONSUMABLE PARTS
SELECTION
CAUTION
Sparks from the cutting process can
cause damage to coated, painted, and
other surfaces such as glass, plastic and
metal.
NOTE
Handle torch leads with care and protect
them from damage.
To change the torch consumable parts use the
following procedure: Position the torch with the
shield cup facing upward to prevent these parts
from falling out when the cup is removed.
Use:
- .036 ø cutting tip to cut pieces more than .2
inch thick (output current 30-40 Amp)
- .031 ø cutting tip to cut pieces more than .2
inch thick (output current 20-30 Amp)
- .025 ø cutting tip to cut pieces less than .2
inch thick (output current 10-20 Amp)
WARNING: Wait the torch has suffi
ciently
cooled before replacing torch parts.
1. Unscrew and remove the shield cup from the
Torch Head Assembly.
2. Remove the tip, swirl ring, and electrode.
3. Install the electrode, swirl ring, and tip.
4. Hand tighten the shield cup until it is seated
on the torch head. If resistance is felt when
installing the cup, check the threads before
proceeding.
OPERATING FAULTS
During cutting operations performance faults
may arise which are not caused by the plasma
cutter but by other operational faults such as:
• Insuffi
cient penetration :
too high cutting speed;
torch is too tilted;
piece is too thick;
cutting current too low;
torch parts are worn out;
non-genuine Manufacturer’s parts;
•
Interruption of the cutting arc:
cutting speed too slow;
excessive distance between torch and
workpiece;
AC line too low - reduce output current;
torch parts are worn out;
non-genuine Manufacturer’s parts;
work cable is disconnected;
• Excessive
dross:
too low cutting speed (bottom dross);
too high cutting speed (top dross);
excessive distance between torch and
workpiece;
cutting current too low;
torch parts are worn out;
non-genuine Manufacturer’s parts;
•
Tilted cutting (not perpendicular):
torch position not correct;
asymmetric wear of nozzle hole and/or wrong;
assemblage of the torch parts;
•
Excessive wear of nozzle and electrodes:
air pressure too low;
exceeding system capability (material too thick);
contaminated air (humidity-oil);
excessive pilot arc arc ignitions in the air;
Improperly assembled torch;
torch tip contacting workpiece;
damaged or loose torch head components;
non-genuine Manufacturer’s parts.
Summary of Contents for MICROCUT 600
Page 18: ...18 WIRING DIAGRAM...