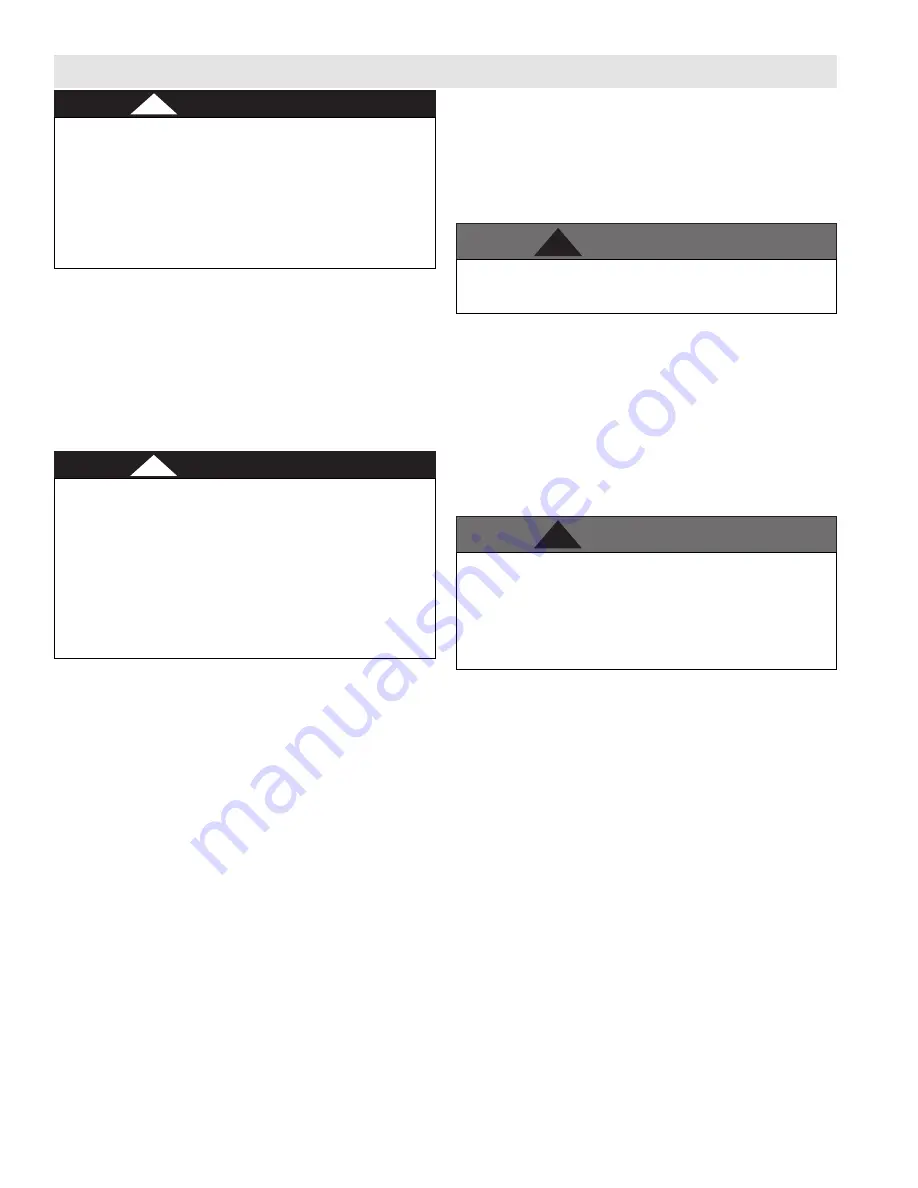
LP-719 Rev. 000 Rel. 000 Date 6.25.20
78
Part 14 - Maintenance
DANGER
!
The boiler must be inspected and serviced annually, preferably at
the start of the heating season, by a qualified service technician. In
addition, the maintenance and care of the boiler as outlined in this
manual must be performed by the user/owner to assure maximum
efficiency and reliability. Follow the maintenance procedures
given throughout this manual. Failure to perform the service and
maintenance or follow the directions in this manual could damage
the boiler or system components, resulting in substantial property
damage, severe personal injury, or death.
A. Procedures
Periodic maintenance should be performed once a year by a qualified
service technician to ensure that all the equipment is operating safely
and efficiently. The owner should make necessary arrangements with
a qualified heating contractor for periodic maintenance of the boiler.
The installer must also inform the owner that a lack of proper care
and maintenance of the boiler may result in a hazardous condition.
Check the Surrounding Area
DANGER
!
To prevent the potential of substantial property damage, severe
personal injury, or death, eliminate all the materials listed in Table
6 from the area surrounding the boiler and the vicinity of the
combustion air intake. If contaminants are found:
•
Remove products immediately from area.
•
If contaminants have been there for an extended period,
call a qualified service technician to inspect the boiler for
possible damage from acid corrosion.
If products cannot be removed, immediately call a qualified service
technician to re-pipe the combustion air intake piping away from
the contaminated areas.
Ensure the Cabinet is Closed When the Boiler is Operating
The boiler cabinet must be closed when the boiler is operating.
Combustible/Flammable Materials
Do not store combustible materials, gasoline, or other flammable
vapors or liquids near the boiler. If found, remove these materials
immediately.
Air Contaminants
If allowed to contaminate combustion air, products containing
chlorine or fluorine will produce acidic condensate that will
cause significant damage to the boiler. Read the list of potential
contaminants and areas likely to have these contaminants in Table
6. If any of these contaminants are in the room where the boiler is
located, or combustion air is taken from one of the areas listed, the
contaminants must be removed immediately or the intake pipe must
be relocated to another area.
Check the Power Source
Make sure the power cord and the main power line are properly
connected to the manual switch box inside the boiler.
Check the Status of the Control Panel
Observe the Control Panel to ensure the boiler is powered on and to
check for any error codes. Clear any debris from the panel.
Check CH Pressure Gauge
Ensure the pressure reading on the CH gauge does not exceed 30
psig. Higher pressure readings may indicate a problem with the
expansion tank. Immediately contact a qualified service technician
to inspect the boiler and system.
Check Exhaust Vent and Intake Pipe Terminations
Verify that the boiler exhaust vent and intake pipe terminations are
clean and free of obstructions. Remove any debris from the exhaust
B. Maintenance That May be Performed by the User
vent or intake pipe openings. If removing the debris does not
allow the boiler to operate correctly, contact your qualified service
technician to inspect the boiler and the vent system.
Check Exhaust Vent and Intake Piping
Visually inspect the exhaust vent for any signs of blockage, leakage,
or deterioration of the piping. Inspect the exhaust vent bracing.
Ensure bracing is undamaged and in good condition. Notify a
qualified service technician immediately if any problems are found.
WARNING
!
Failure to inspect the venting system and have it repaired by
a qualified service technician can result in vent system failure,
causing severe personal injury or death.
Check Pressure Relief Valve
1. Visually inspect the primary pressure relief valve and discharge
pipe for signs of weeping or leakage.
2. If the pressure relief valve often weeps, the expansion tank may
not be operating properly. Immediately contact a qualified
service technician to inspect the boiler and system.
Operate Pressure Relief Valve
1. Before proceeding, verify that the relief valve outlet has been
piped to a safe place of discharge, avoiding any possibility of
scalding from hot water.
2. Shut power off to the boiler. To avoid scalding, wait for boiler to
cool before operating the relief valve.
WARNING
!
To avoid water damage or scalding due to relief valve operation, a
discharge line must be connected to the valve outlet and directed
to a safe place of disposal. This discharge line must be installed
by a qualified service technician in accordance with the boiler
installation manual. The discharge line must be terminated so as
to eliminate possibility of severe burns or property damage should
the valve discharge.
3. Lift the relief valve lever. If water flows freely, release the lever
and allow the valve to seat. Watch the end of the relief valve
discharge pipe to ensure that the valve does not weep after
the line has had time to drain. If the valve weeps, lift the lever
again to attempt to clean the valve seat. If the valve does not
properly seat and continues to weep, contact a qualified service
technician to inspect the valve and system.
4. If water does not flow from the valve when you completely
lift the lever, the valve or discharge line may be blocked.
Immediately shut the boiler down per instructions on page 2
and call a qualified service technician to inspect the valve and
system.
5. If relief valve seats properly, restore power to the boiler. Observe
operation for five minutes and ensure it operates properly.
Check the Condensate Drain System
1. While the boiler is running, check the discharge end of the
condensate drain tubing. Ensure no flue gas is leaking from
the condensate drain tubing by holding your fingers near the
opening.
2. If you notice flue gas leaking from the opening, this indicates
a dry condensate drain trap. If problem persists, contact
a qualified service technician to inspect the boiler and
condensate line and refill the condensate trap.
3. If applicable, check the condensate neutralizer and ensure it is
full of condensate neutralizing marble chips.