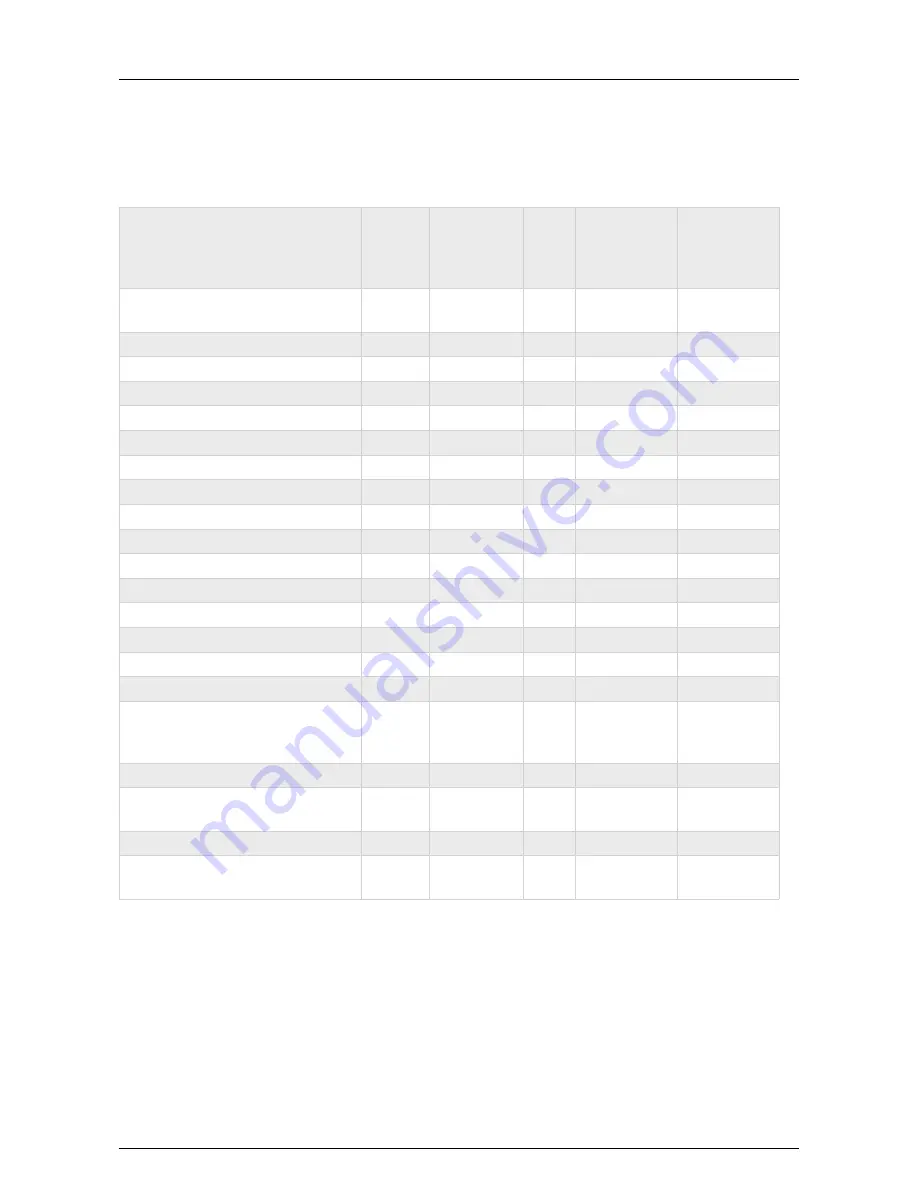
Technical data
HTC 270 EG
40
2.0
8
Technical data
The table below shows the machine's technical data.
Machine type
HTC 270 EG
1 x 230 V, 50
Hz
EU
HTC 270 EG
1 x 230 V, 60
Hz
US
HTC 270 EG
3 x 460 V, 60
Hz
US
Part number
Article
no.
501054
Item
no.
113256
113325
Total machine weight
kg
103
lbs
227
227
Weight, grinding head
kg
55
lbs
121
121
Chassis weight
kg
48
lbs
106
106
Grinding pressure
kg
36
lbs
79
79
Grinding diameter
etc.
270
in
10.6
10.6
Grinding discs
etc.
1 x 270
in
1 x 10.6
1 x 10.6
Motor
kW
2.2
hp
2.9
2.9
Voltage
W
1 x 230
W
1 x 230
3 x 460
Current
A
13
A
13
5
Recommended minimum cable area
mm²
2.5
in²
0.004
0.004
Frequency
Hz
50
Hz
60
60
Rotational speed, grinding discs
rpm
455-1210
rpm
455-1210
455-1210
Storage temperature
°C
-25…+70
°F
-13…+158
-13…+158
Working temperature
°C
-10…+50
°F
14…+122
14…+122
Humidity
%
5-95
%
5-95
5-95
Sound power level, according to ISO
3741, measured using class 1
instruments as sound level meters.
dBA
100
dBA
100
100
Vibrations, grinding/polishing
m/s²
3.92
m/s²
3.92
3.92
Permitted daily exposure,
grinding/polishing
h
13
h
13
13
Vibrations, Floor preparation (T-Rex) m/s²
3.75
m/s²
3.75
3.75
Permitted daily exposure, Floor
preparation (T-Rex)
h
14.2
h
14.2
14.2
Summary of Contents for 270 EG
Page 1: ...HTC 270 EG MANUAL GB Translation of manual in original language...
Page 2: ...HTC 270 EG...
Page 8: ...Table of contents HTC 270 EG iv...
Page 25: ...HTC 270 EG Usage 2 0 17 4 4 1 Fitting grinding tools...
Page 49: ...HTC 270 EG Technical data 2 0 41 Figure 8 1 Height and length of the machine in millimetres...
Page 50: ...Technical data HTC 270 EG 42 2 0 Figure 8 2 Width of the machine in millimetres...
Page 51: ...HTC 270 EG Technical data 2 0 43 Figure 8 3 Working angles for the grinding head...