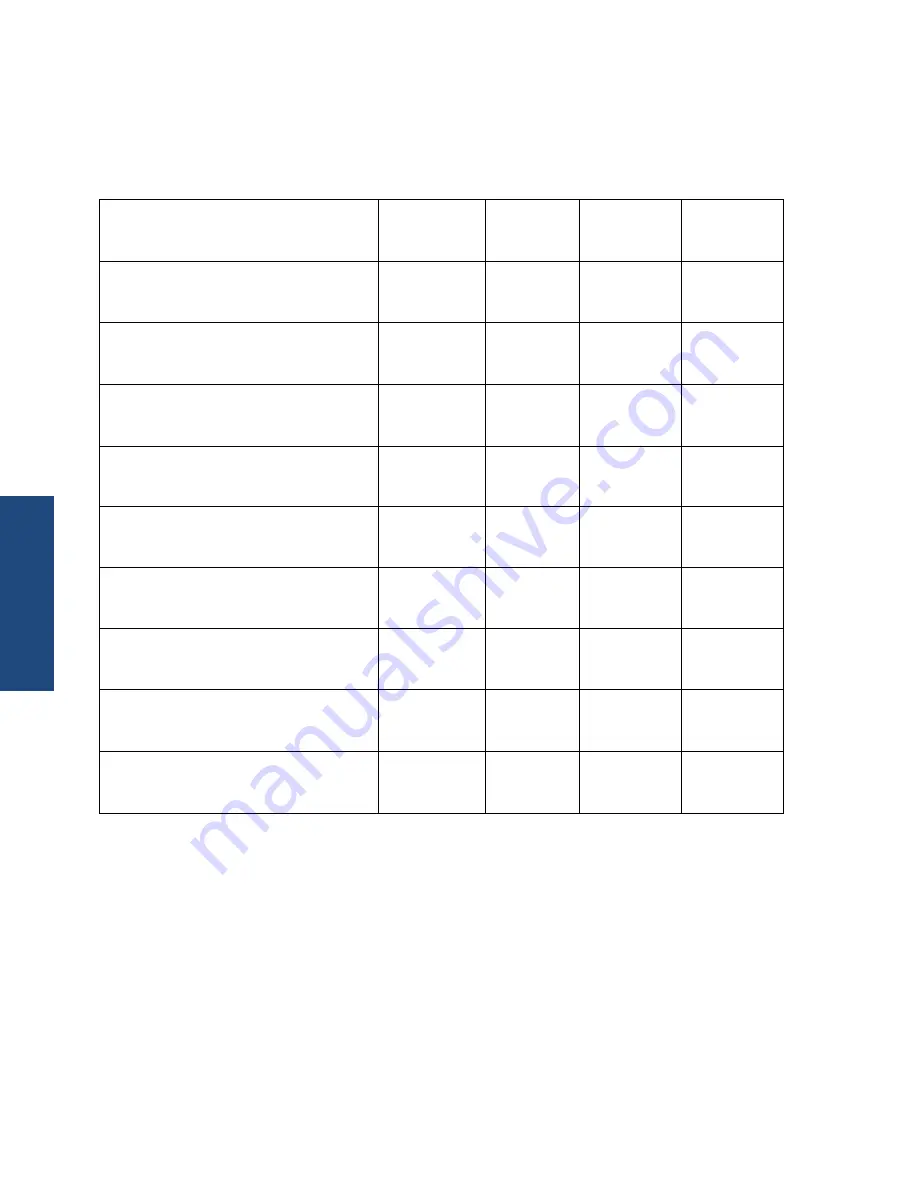
28
St
art
U
p &
O
pe
rat
io
n
Maintenance
Preventative Maintenance Schedule
Page
Number
Every 3
Months
Every 6
Months
Every 12
Months
Lubricate Sleeve Bearings
•
Ensure Float Valve is unclogged and
flowing freely
•
Verify correct Sequence of
Operation of Photo Eye sensors
•
Clean and Sanitize Ice Flaker
•
Replace Water Filter Cartridge
•
Run a Field Capacity Check
•
Verify Ice Blade Clearance
•
Check Squeegee for excessive and
uneven wear
•
Check Main Shaft for movement
and Sleeve Bearing wear
•
Summary of Contents for HoweIce Rapid Freeze 4000-RL-CO 2DX
Page 6: ...6 Engineering Guidelines Figure 1...
Page 37: ...Appendix 37 Appendix Cut View 1000 RLE...
Page 38: ...38 Appendix Cut View 2000 RLE...
Page 39: ...Appendix 39 Assembly Drawing 1000 RLE Ice Flaker CP750 Mobile Express Ice Bin...
Page 40: ...40 Appendix Assembly Drawing 2000 RLE Ice Flaker CP1500 Mobile Express Ice Bin...
Page 41: ...Appendix 41 Wiring Diagram Ice Flaker Main Control Panel...
Page 42: ...42 Appendix Wiring Diagram CO2 EEV EEPR Control Panel...