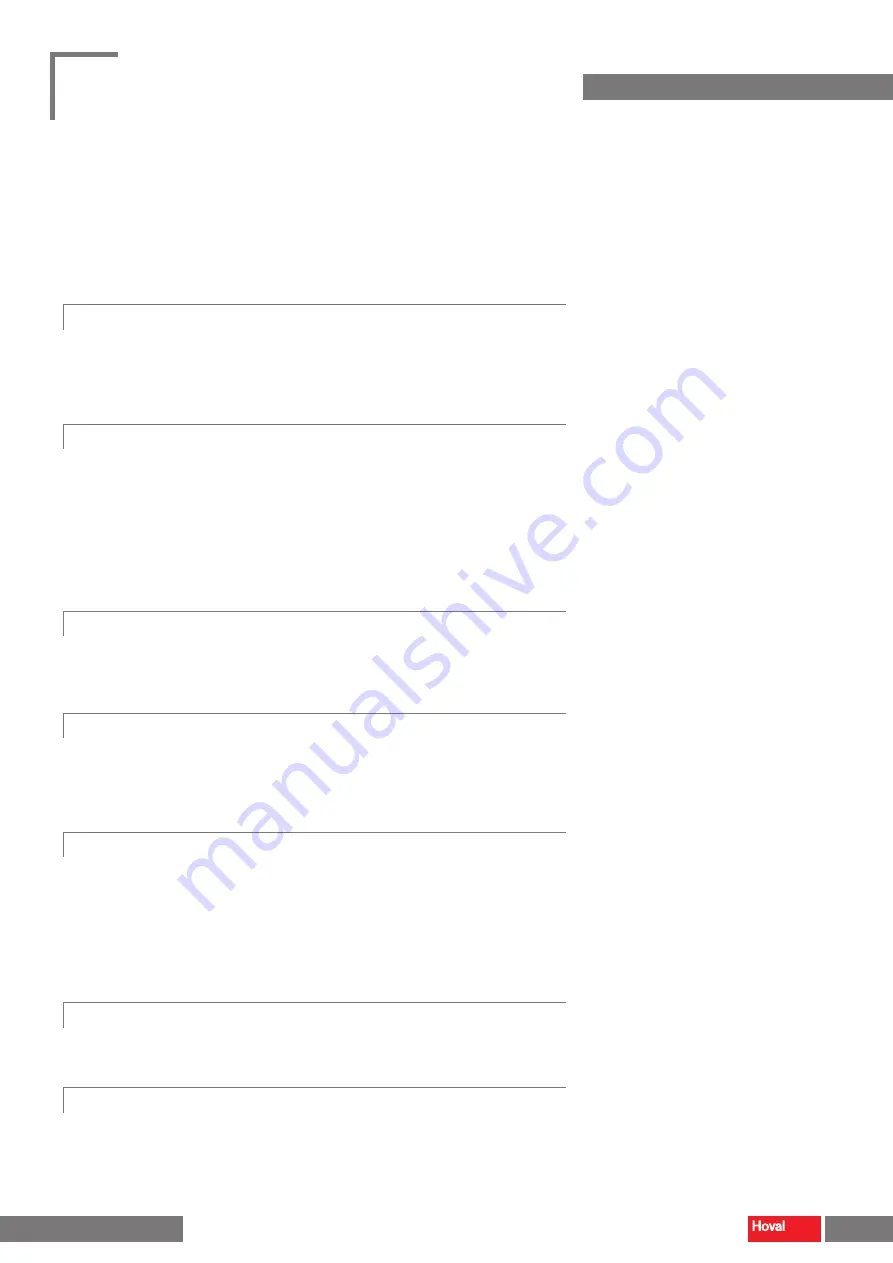
11.4 Measures
After identifying the problem, use the Case number to find the possible cause in
this paragraph.
Case 1: Flame lasts only 5 seconds after ignition
■
No flame is detected:
–
Check the ignition/ionisation cable and the electrode. The cable should have
a resistance of 1 kΩ.
■
The unit is not earthed properly.
■
The circuit board is defective.
Case 2: No flame after ignition
■
There is not enough gas pressure.
■
The gas mixture is too poor.
–
Re-adjust the gas valve (see section 9.5).
■
The gas valve does not open.
–
During ignition, check for a 230 V voltage on the valve.
■
Check if the ignition electrode sparks. If not:
–
Check the cable and electrode.
–
Check if the burner control gives a spark output.
–
Replace defective components.
Case 3: Heat exchange sensor or flue gas sensor overheated
■
Check if the connectors J12 and J6 are plugged in correctly and if the terminals
J12-1 / J12-4 (optional overheating protection) are jumpered.
■
Check if the system fan supplies enough air.
■
Check the settings of the gas valve.
Case 4: Heat exchange sensor or flue gas sensor not detected, or short circuit
■
The heat exchange sensor consists of 2 internal sensors. The readings of these
sensors may differ too much.
–
Measure the resistance of each sensor. The resistance should be 20 kΩ at
25 °C and 25 kΩ at 20 °C.
–
If the measured values differ too much, replace the sensor.
Case 5: Too many flame failures while burning
■
The gas supply is not constant. This results in a drop in gas supply pressure
while burning.
–
Check the gas supply pressure while the heater is burning.
■
The burner pressure for partial load operation is too low.
–
Check the burner pressure in partial load operation and adjust if necessary.
■
Flue gas is sucked back into the air inlet, resulting into a lack of oxygen.
–
Check the flue gas system and combustion air supply. Only certified, original
parts should be used.
Case 6: Gas blower does not work
■
Check if the gas blower fan is blocked.
■
Check if the wiring is damaged.
■
The gas blower is defective.
Case 7: Gas blower rotates at the wrong speed
■
Check if the gas blower runs smoothly.
■
Check if the wiring is damaged.
34
TopVent
®
TG | GV | MG
Operating instructions
Troubleshooting
4 220 656-en-03
4 220 656-en-03
Summary of Contents for TopVent GV
Page 41: ...41 4220656 en 03 Notes...
Page 42: ...42 4220656 en 03 Notes...
Page 43: ...43 4220656 en 03...