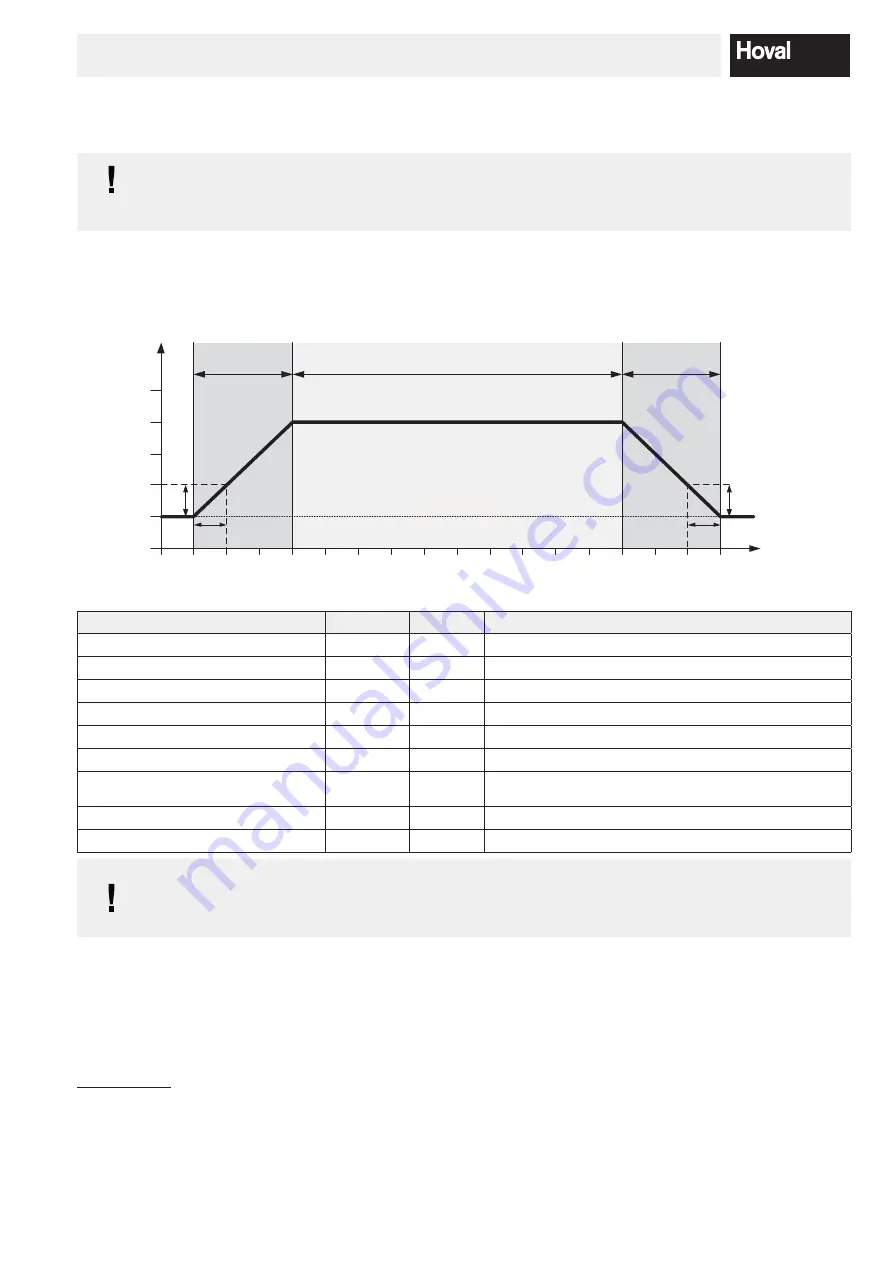
31
4 214 864 / 02
COMMISSIOnInG
NOTICE
The activation of the screed function must only be made by a specialist trained by Hoval or by Hoval cus-
tomer service.
Description of function
The control module of the TopTronic
®
E contains a functional sequence used for drying out screed fl oors. To start the
screed drying, it is necessary for the individual functions to be set accordingly.
Flow temperature
Start
Days
0
1
2
3
4
10
11
12
13
5
6
7
8
9
40°C
45°C
35°C
30°C
25°C
20°C
14
15
16
5K
1 d
Heating-up phase
( 04-061)
Inerta phase
( 04-064)
Cool-down phase
( 04-062)
Starttemperatur
( 04-075)
End
-5K
1 d
Start temperature
(04-075)
Function
Parameters Value
Description
Start temp. screed drying
04-075
25.0°C
Start temperature (from SW 2.09.xxx)
Heating-up phase
04-061
5 K/d
Kelvin per day (rising)
Stabilisation temperature
04-063
40.0 °C
Inertia phase fl ow setpoint
Inertia phase
04-064
10
Number of days in stabilisation temperature
Cooling off phase
04-062
-5 K/d
Kelvin per day (falling)
Activate screed function
04-060
1 (ON)
Start and stop screed drying
Max. temp. diff . ramp increase screed func-
tion (from SW 2.03.xxx onwards)
04-069
10 K
Kelvin (FL act/set)
Information
Remaining run time screed function
02-019
… days
Forecast in days
NOTICE
The graphic/table shows the factory settings. The time profi le and the maximum fl ow temperature must be
discussed with the screed layer, otherwise there could be damage to the screen – and in particular, cracks.
REACTION
screed function
• Start/stop: Switch parameter 04-060 ON (1) or OFF (0)
• Power failure in heating-up phase: program restart
• Failure in the steady-state phase: Retain maximum temperature and add the failure time to the steady-state phase
•
Power failure in the cooling off phase: Measurement of actual fl ow value and continue cooling until start value reached
• Program end: Previous basic program active again
Additional info:
When the screed function starts, the heating circuit pump is switched on and the screed function starts after 1 minutes.
The FL set value must be reached in each case so the controller continuously increases the fl ow temperature according
to the set ramp. With HC parameter “04-069 Maximum temperature diff erence ramp increase (factory setting: 10 K)”
it possible to set by how much the FL set value calculation is allowed to increase without the actual value reaching the
set value.
5.6
Record - Activation of screed function
Summary of Contents for CompactGas
Page 36: ...36 4 214 864 02 ...
Page 37: ...37 4 214 864 02 ...