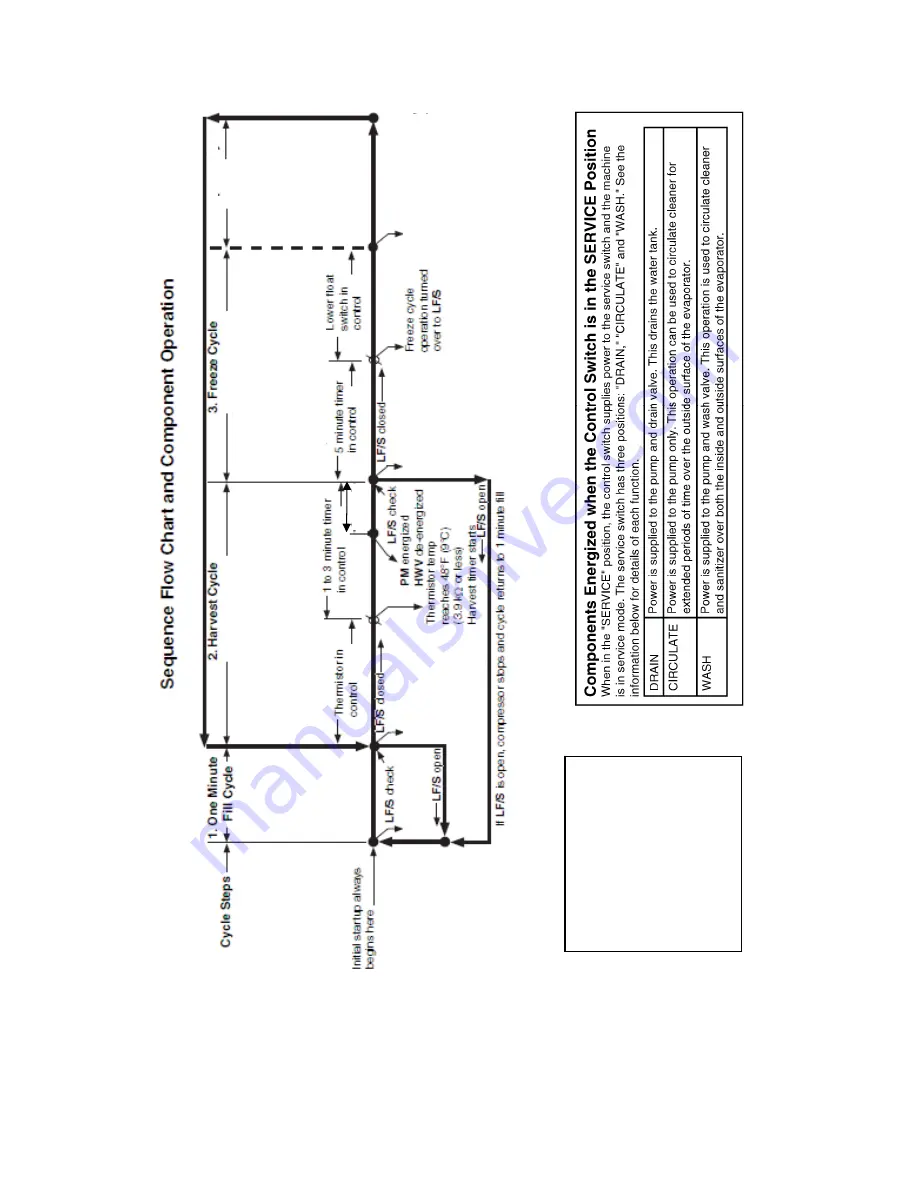
7
KMD-410MA
H, 410MWH
“H” board will have
5 second delay
x
Maximum harvest water valve time: 6 minutes
(HWV time is 6 minutes of the length of harvest
minus 0, 10, 30, or 50 sec. (S1
dip switch
7 & 8), whichever is shorter. P
M
energizes
and runs for th
e last 0, 10, 30, o
r 50 sec. of
harvest.)
x
Maximum harvest time: 20 minutes
x
Minimum freeze time: 5 minutes
x
Maximum freeze time: freeze time setting
x
Lower float swit
ch used to initiate water
Tank refill (1 refill for KMD-410)
x
Upper float swit
ch used to termin
ate
water tank refill (1 minute maximum fill
time)
Factory set for every
10
th
cycle (S1 dip
Switch 5 & 6)
Pump motor stop
s
for 2 sec. and th
en
runs for 10/
20 se
c.
(S1 dip switch 3 & 4)
0, 0,30,
or 50 sec
HWV
energized
COMP
ene
rgized
HGV
ene
rgized
HWV
continues
FW
V
de-ene
rgized
DV
de-ene
rgized
COMP
continues
PM
continues
FW
V
energized/
de-energized
for
refill
onl
y
FMS
energized
HGV
de
-ene
rgized
PM
de-ene
rgizes 0/2 sec.,
energizes
fo
r
10/20
sec.
COMP
continues
DV
energized/
HGV
ene
rgized
FMS
de-en
ergize
d
Lege
nd:
COMP
- comp
re
ssor
DV
– drain valve
FMS
– self-conta
ined fan motor
FW
V
– fill water valve
HGV
– ho
t gas valve
HWV
– harvest
water valve
LF/S
– lowe
r floa
t switch contacts
PM
– pump moto
r
UF/S
– upp
er flo
at switch contacts
4. Drain C
ycle