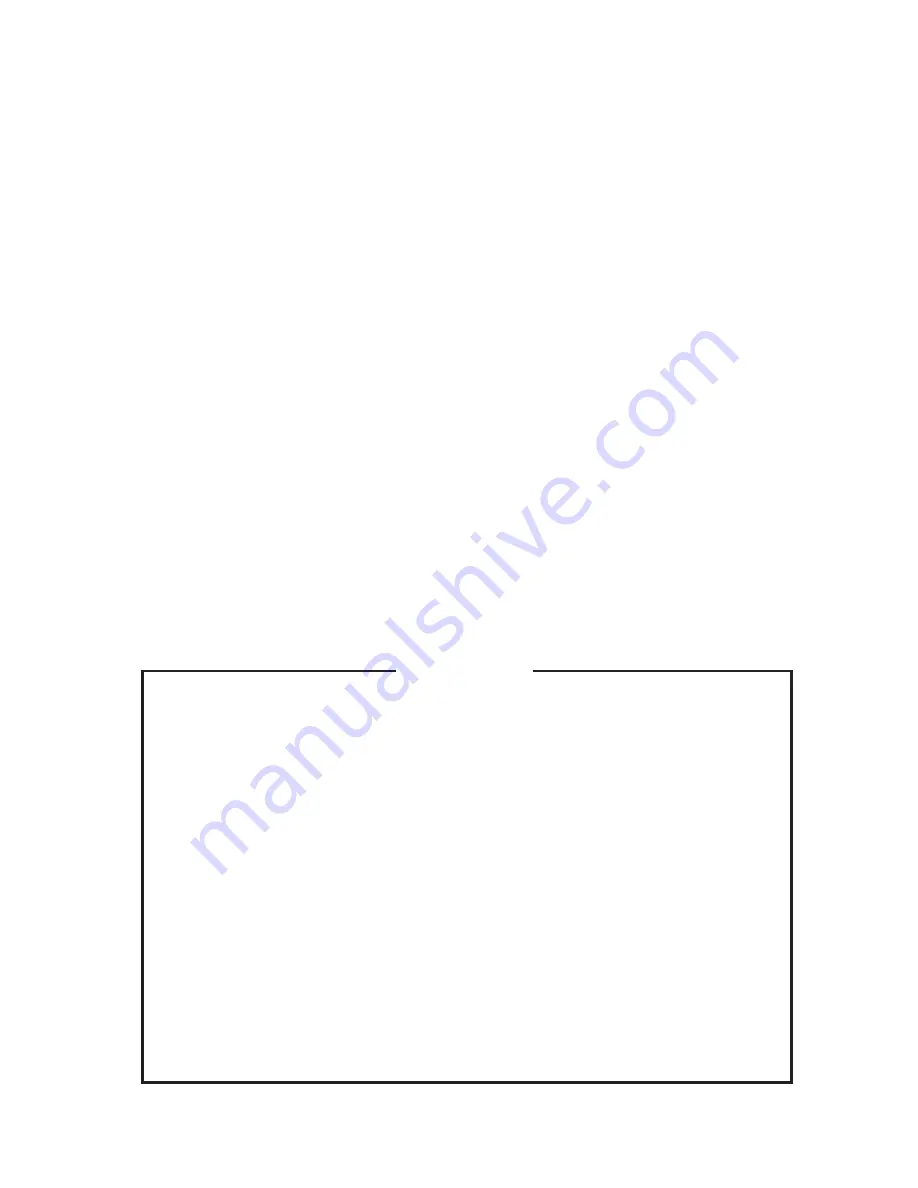
51
3) Allow the vacuum pump to pull down to a 29.9" Hg vacuum. Evacuating period
depends on pump capacity.
4) Close the low-side valve and high-side valve on the service manifold.
5) Disconnect the vacuum pump, and attach a refrigerant service cylinder to the high-
side line. Remember to loosen the connection, and purge the air from the hose. See
the nameplate for the required refrigerant charge. Hoshizaki recommends only virgin
refrigerant or reclaimed refrigerant which meets ARI Standard No. 700-88 be used.
6) A liquid charge is recommended for charging an R-404A system. Invert the service
cylinder. Open the high-side, service manifold valve.
7) Allow the system to charge with liquid until the pressures balance.
8) If necessary, add any remaining charge to the system through the low-side. Use a
throttling valve or liquid dispensing device to add the remaining liquid charge
through the low-side access port with the unit running.
9) Close the two refrigerant access valves, and disconnect the hoses and service
manifold.
10) Cap the access valves to prevent a possible leak.
2. Brazing
DANGER
1. Refrigerant R-404A itself is not flammable at atmospheric pressure and
temperatures up to 176
° F.
2. Refrigerant R-404A itself is not explosive or poisonous. However, when
exposed to high temperatures (open flames) R-404A can be decomposed
to form hydrofluoric acid and carbonyl fluoride both of which are hazard-
ous.
3. Always recover the refrigerant and store it in an approved container. Do
not discharge the refrigerant into the atmosphere.
4. Do not use silver alloy or copper alloy containing arsenic.
5. Do not use R-404A as a mixture with pressurized air for leak testing.
Refrigerant leaks can be detected by charging the unit with a little
refrigerant, raising the pressure with nitrogen and using an electronic leak
detector.
Summary of Contents for F-1500MA-C
Page 11: ...11 2 Condenser Unit URC 12F...
Page 18: ...18 III Technical Information 1 Water Circuit and Refrigeration Circuit F 1500MAH C...
Page 19: ...19 F 1500MWH C...
Page 20: ...20 F 1500MRH C...
Page 21: ...21 2 Wiring Diagrams F 1500MAH C...
Page 22: ...22 F 1500MWH C...
Page 23: ...23 F 1500MRH C...
Page 25: ...25 b When reservoir has been filled gear motor starts immediately...
Page 26: ...26 c Compressor starts about 60 sec after gear motor starts...
Page 27: ...27 d Bin control operates and about 6 sec later compressor and gear motor stop simultaneously...
Page 28: ...28 e Low water except water cooled model...
Page 32: ...32 4 Timing Chart...
Page 33: ...33...
Page 34: ...34...
Page 35: ...35...
Page 36: ...36...