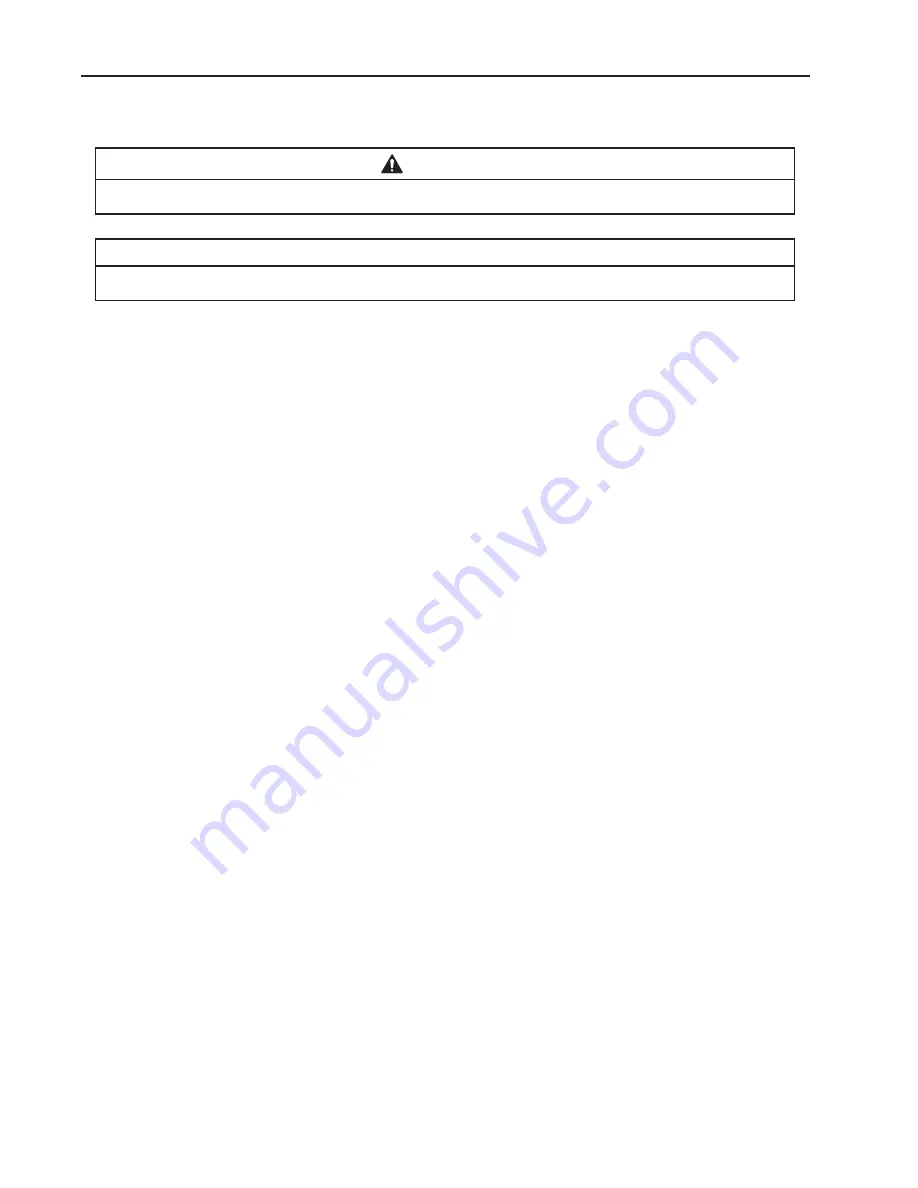
48
V. Preparing the Appliance for Periods of Non-Use
When shutting down the appliance for periods of non-use, follow the instructions below.
WARNING
Prevent the doors from closing to reduce the risk of children getting trapped.
NOTICE
Clean the cabinet interior, door gaskets, and shelves.
1) Before shutting down the appliance, move the stored food into another refrigerator or
freezer.
2) Unplug the appliance.
WARNING! To reduce the risk of electric shock, do not touch
the plug with damp hands.