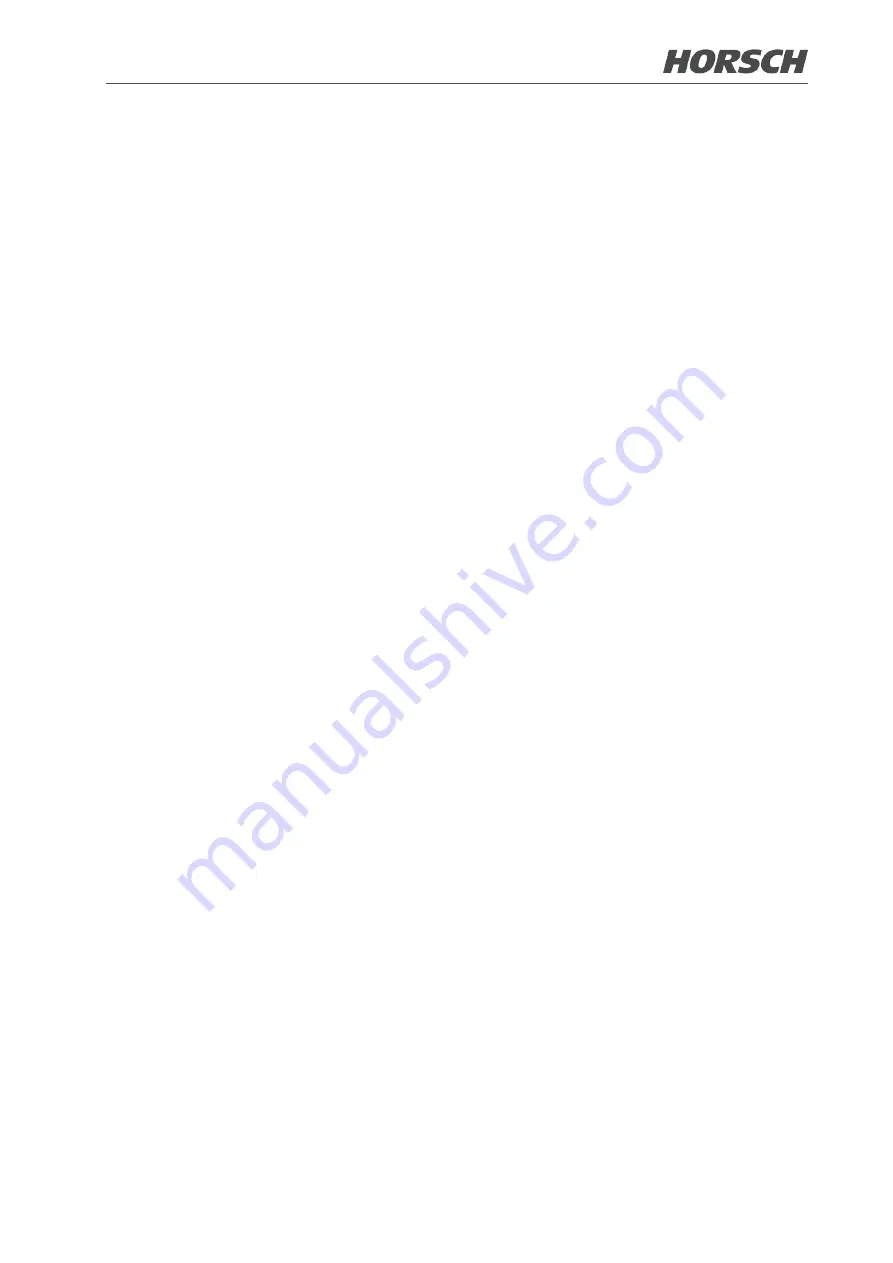
Service
HORSCH Company would like you to be com-
pletely satisfied with your machine and our
services.
If you encounter any problems, please feel free
to contact your sales partner.
The service staff of our sales partners and the
service employees at HORSCH will always be
available to assist you.
In order to be able to solve technical problems
as quickly as possible, we ask you kindly to
support us.
Please help the service personnel by providing
the following information to avoid unnecessary
queries.
•
Customer number
•
Name of customer representative
•
Name and address
•
Machine model and serial number
•
Purchasing date and operating hours or area
performance
•
Type of problem
Warranty claim
processing
Warranty claim forms must be submitted to
HORSCH through your local HORSCH sales
partner.
Consequential damage
The machine has been manufactured by
HORSCH with greatest care. However, despite
the intended use deviations in placing quantity
up to total failure may be caused by e.g.:
•
damage caused by external influences
•
wear of wear items
•
missing or damaged cultivation tools
•
incorrect travel speeds
•
incorrect setting of the unit (incorrect connec-
tion, non-observance of setting tables)
•
failure to comply with the operating instruc-
tions
•
neglect and improper care and maintenance
Therefore, it is crucial to always check your ma-
chine before and during use for correct operation
and adequate application accuracy.
Compensation claims for damages that have
not occurred on the machine are excluded. This
also means that any liability for consequential
damages caused by travel and operating faults
is excluded.
5