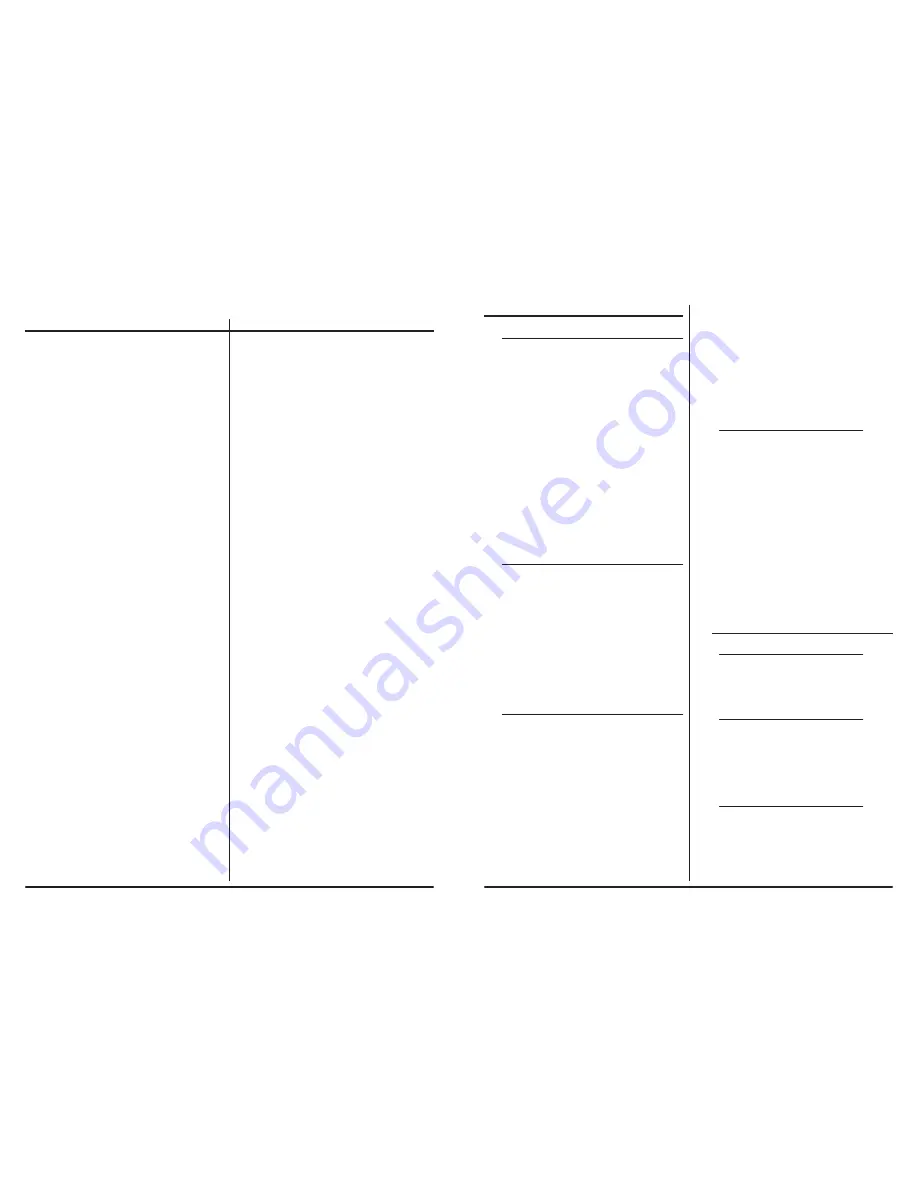
38
JR 11X • RADIO INSTRUCTION MANUAL
39
JR 11X • RADIO INSTRUCTION MANUAL
Your DSM2 equipped 2.4GHz system is intuitive to operate, functioning
nearly identically to FM systems. Following are a few common questions from
customers:
Q: After I’ve bound the receiver to my transmitter, which do I turn
on first when I want to fly?
A:
Either one. Every DSM 2.4GHz transmitter has a GUID (Globally Unique
Identifier) code imbedded in its signal. When you bind a DSM receiver
to your transmitter, this GUID code is stored in the receiver. If you turn
the receiver on before the transmitter, you don’t have to worry about it
responding to another transmitter. The receiver will inhibit throttle output
and drive all controls to preset positions while it waits for a signal from the
transmitter with the same GUID code it has stored.
If a DSM transmitter is turned on first you can expect it to connect within 6
seconds of powering on the receiver.
Q: Sometimes the system takes longer to connect or doesn’t
connect at all. Why?
A:
In order for a DSM system to connect, the receiver must receive a large
number of uninterrupted signal packets from the transmitter. This process
takes just a few seconds, but if the transmitter is too close to the receiver
(within 4 feet) or near metal objects it may detect its own reflected 2.4GHz
energy as “noise”. This can delay or prevent connection.
If this happens make sure you are a sufficient distance from metal objects
and the receiver itself before you power up and try again.
Q: Is it true that DSM systems are less tolerant of low voltage?
A:
All DSM receivers require at least 3.5V to operate normally. Most servos
cease to operate below 3.8V. Using multiple high-voltage servos, however,
with an inadequate power supply can allow voltage to momentarily drop
below 3.5V. This will cause the receiver to “brown out” and reconnect.
All recently manufactured JR and Spektrum DSM receivers feature
QuickConnect technology that will reconnect the system within a quarter of
a second should a brownout occur. In addition, the receiver’s LED will flash,
indicating a brownout has occurred. If after landing you notice your DSM
receiver’s LED is flashing, make sure you have adequate power before you
fly again.
Q: Sometimes when I power on my DSM system I notice the
receiver won’t connect and it needs to be rebound to the
transmitter. Can this happen in flight?
A:
No. A DSM receiver cannot be unbound from its transmitter without specific
action by the user.
You can accidentally unbind a receiver by inadvertently pressing the bind
button on your transmitter when you turn it on. This causes the transmitter
to go into bind mode. If this happens and the transmitter doesn’t detect a
binding signal from the receiver it can cause the receiver to be unbound.
Some transmitter stands can cause the bind button to be depressed during
power up, but these instances are extremely rare.
If your system fails to connect, chances are much greater that it’s the result
of one of the following conditions and not because the receiver is unbound.
1. You’ve selected the wrong model memory.
2. The transmitter is too close to conductive material to connect
(see FAQ #2).
Q: How important is it that I test my system using a Spektrum
flight Log?
A:
All 2.4GHz signals, not just DSM, are affected by proximity to conductive
materials such as carbon fiber or metal. Few RTF and ARF sport airplanes
or helicopters use enough of these kinds of materials for it to be an issue.
If, however, you’re flying a sophisticated model that uses a lot of conductive
materials in its construction, a Flight Log can be helpful. The information it
collects when you fly will help you determine the optimum location for your
receiver(s) so you can minimize the effects of these materials on your signal
performance. For more details on the Flight Log and how it works, visit
SpektrumRC.com.
GENERAL INfORMATION
Servo Precautions
• Do not lubricate servo gears or motors.
• Do not overload retract servos during retracted or extended conditions. Make
sure they are able to travel their full deflection. Overloading or stalling a
servo can cause excessive current drain.
• Make sure all servos move freely through their rotations and no linkages
hang up or bind. A binding control linkage can cause a servo to draw
excessive current. A stalled servo can drain a battery pack in a matter of
minutes.
• Correct any control surface “buzz” or “flutter” as soon as it is noticed in
flight, as this condition
can destroy the feedback potentiometer in the servo. It may be extremely
dangerous to ignore such “buzz” or “flutter.”
• Use the supplied rubber grommets and brass servo eyelets when mounting
your servos. Do not over-tighten the servo mounting screws, as this negates
the dampening effect of the rubber grommets.
• Ensure the servo horn is securely fastened to the servo. Use only the servo
arm screws provided; the size is different from other manufacturers.
• Discontinue to use servo arms when they become “yellowed” or discolored.
Such servo arms may be brittle and can snap at any time, possibly causing
the aircraft to crash.
• Check all related mounting screws and linkages frequently. Aircraft often
vibrate, causing linkages and screws to loosen.
General Notes
Radio controlled models are a great source of
pleasure. Unfortunately, they can also pose a
potential hazard if not operated and maintained
properly.
It is imperative to install your radio control
system correctly. Additionally, your level of
piloting competency must be high enough to
ensure that you are able to control your aircraft
under all conditions. If you are a newcomer to
radio controlled flying, please seek help from an
experienced pilot or your local hobby store.
Safety, Precautions, and Warnings
As the user of this product, you are solely
responsible for operating it in a manner that does
not endanger yourself and others or result in
damage to the product or the property of others.
Carefully follow the directions and warnings for
this and any optional support equipment (chargers,
rechargeable battery packs, etc.) that you use.
This model is controlled by a radio signal that
is subject to interference from many sources
outside your control. This interference can cause
momentary loss of control so it is necessary to
always keep a safe distance in all directions around
your model, as this margin will help to avoid
collisions or injury.
• Always operate your model in an open area away from cars, traffic, or
people.
• Avoid operating your model in the street where injury or damage can occur.
• Never operate the model out into the street or populated areas for any
reason.
• Never operate your model with low transmitter batteries.
• Carefully follow the directions and warnings for this and any optional
support equipment (chargers, rechargeable battery packs, etc.) that you use.
• Keep all chemicals, small parts and anything electrical out of the reach of
children.
• Moisture causes damage to electronics. Avoid water exposure to all
equipment not specifically designed and protected for this purpose.
Safety Do’s and Don’ts for Pilots
• Ensure that your batteries have been properly charged prior to your initial
flight.
• Keep track of the time the system is turned on so you will know how long
you can safely operate
your system.
• Perform a ground range check prior to the initial flight of the day. See the
“Daily Flight Checks Section” for information.
• Check all control surfaces prior to each takeoff.
• Do not fly your model near spectators, parking areas or any other area that
could result in injury to people or damage of property.
• Do not fly during adverse weather conditions. Poor visibility can cause
disorientation and loss of control of your aircraft. Strong winds can cause
similar problems.
• Do not point the transmitter antenna directly toward the model. The radiation
pattern from the tip of the antenna is inherently low.
• Do not take chances. If at any time during flight you observe any erratic or
abnormal operation, land immediately and do not resume flight until the
cause of the problem has been ascertained and corrected. Safety can never
be taken lightly.
Federal Aviation Administration
Purpose
This advisory outlines safety standards for
operations of model aircraft. We encourage
voluntary compliance with these standards.
Background
Attention has been drawn to the increase in model
aircraft operation. There is a need for added caution
when operating free flight and radio controlled craft
in order to avoid creating a noise nuisance or a
potential hazard to full-scale aircraft and persons
and/or property on the surface.
Operating Standards
Modelers generally are concerned with safety and
exercise good judgment when flying model aircraft.
However, in the interest of safer skies, we encourage
operators of radio controlled and free flight models
to comply with the following standards:
FReQUeNTLy ASkeD QUeSTIONS
ON SPEKTRUM 2.4GHz