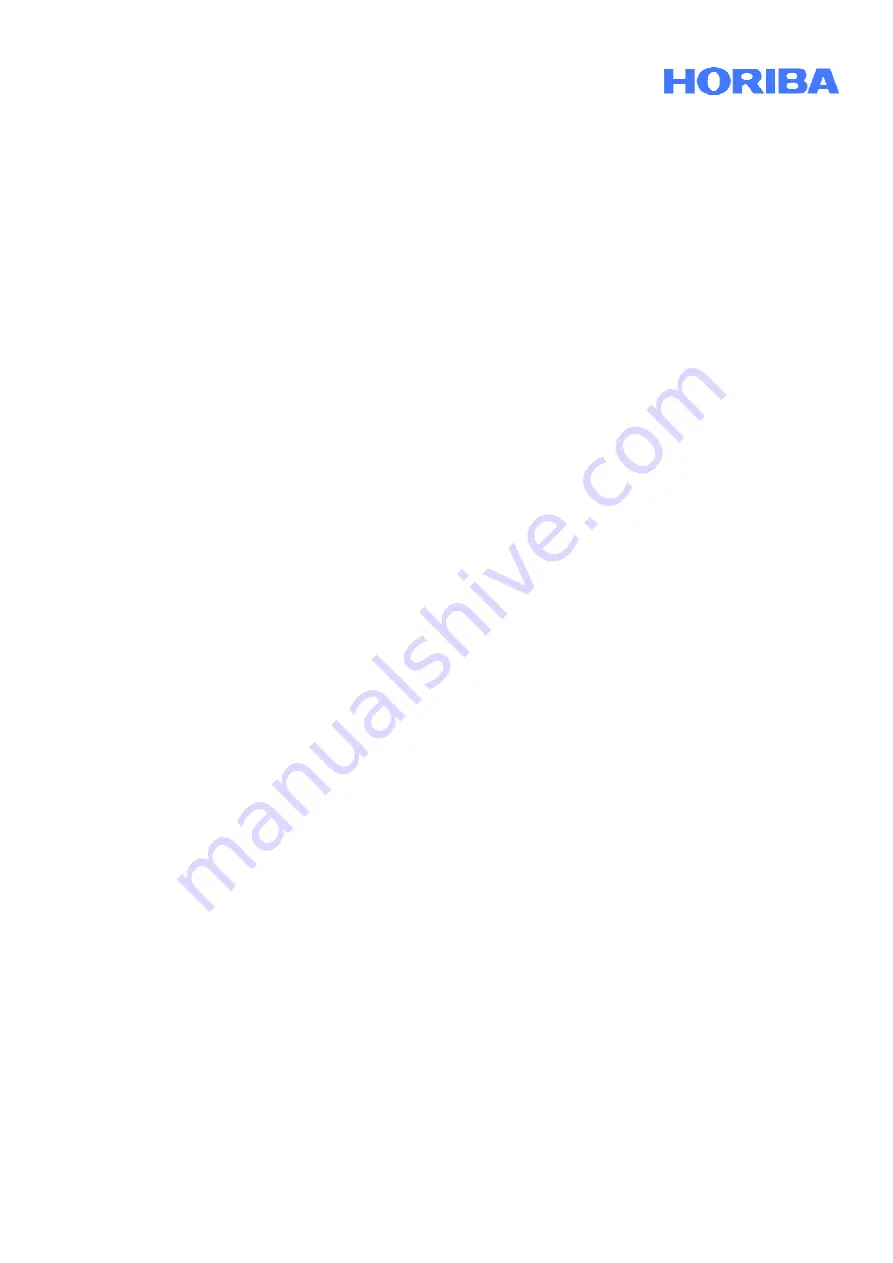
Operation Manual HORIBA APDA-371
Particulate Monitor
Date:
April, 2010
______________________________________________________________________________________________________________________
______________________________________________________________________________________________________________________
HORIBA Europe GmbH, Julius-Kronenberg-Str. 9, D-42799 Leichlingen, Telefon: +49(0)2175-8978-0, Fax: +49(0)2175-8978-50
Page 59
4.
TAPE FAULT
This is a contact-closure output which will be activated whenever a “T” or tape error is
generated (see section 6.5). Polarity is normally-open.
5.
FLOW FAULT
This is a contact-closure output which will be activated whenever an “F” or flow error is
generated (see section 6.5). Polarity is normally-open.
6.
INVALID DATA
This is a contact-closure output which will be activated whenever a C, P, N, R, L, I, M,
or U error is generated by the APDA (see section 6.5). Polarity is normally-open.
7.
MAINT
This is a contact-closure output which will be activated whenever a maintenance “M”
flag is generated (see section 6.5). Polarity is normally-open.
8.
RANGE X1
This contact-closure output is no longer supported. The relay for this channel is now
used by the Smart Heater.
9.
RANGE X10
This contact-closure output is no longer supported. The relay for this channel is now
used by the Smart Heater.
10. PUMP CONTROL
This is the low-voltage output which signals the vacuum pump to turn on or off. There is
no polarity on this output because the pump controller has a diode bridge input.
Connect the two-wire control cable from the pump to these output terminals.
11. POWER FAIL
This is a contact-closure output which will be activated (closed) whenever a power
failure of the 5 volt DC system or an “L” error occurs (see section 6.5).
12. VOLT OUT
This is the analog concentration output voltage terminal. Typically 0-1 VDC. See
section 8.1. Polarity must be observed on this output.
13. CHASSIS
These are the earth-ground terminals. These must be attached to a solid ground point
for best operation of the unit.
14. CL OUT
Current Loop Output. This is used when the analog output is needed in current loop
form instead of voltage. Typically only used if there is a long distance between the
APDA and the datalogger. Output is selectable between 4-20mA or 0-16mA.
8.4
Digital Datalogger Interfacing with the APDA-371
Applications involving digital data transfer between the APDA-371 and other manufacturer’s digital dataloggers, such as
DR DAS
™
and Campbell CR-1000
™
models among others, have become more common. This typically requires a
considerable amount of programming experience with the particular type of logger to be used. Any digital files from the
APDA-371 must be obtained from either the RS-232 two-way serial port, or the RS-232 output-only printer port. There
are several possible pitfalls which can be encountered when collecting APDA-371 data with a digital datalogger.
The most straight-forward way to accomplish digital datalogger interface with the APDA is to configure the printer output
port as a fixed width data output as described in Sections 9.5 and 9.4. This causes the APDA-371 to output a single
fixed-width string of data at the end of each sample hour without having to be prompted. The digital logger must be
programmed to wait for the data string, then process it appropriately.
The alternative is to program the digital datalogger to send the APDA-371 the appropriate commands to retrieve data,
just like you would when downloading the data with a computer as described in Section 9.4. Typically, the APDA would
be sent the appropriate commands to respond with CSV files 6,3 (new data since last download) or 6,4 (last hourly data
record only). The digital logger must receive and sort the files appropriately.
The most important consideration when collecting the data in this manner is to remember that the APDA-371 only
measures concentration data once per hour, and during other parts of the hour (especially near the beginning and end
of each hour) the APDA is often moving tape transport parts and making mechanical adjustments which prevent the
unit from responding to digital data requests due to a busy processor. See Section 4. The best solution is to
program the digital logger to make a single data request to the APDA at some time during the sample period near the
middle of each hour, such as between minute 25 and minute 50. This is especially important if large amounts of data
are to be downloaded at once, since it can take more than 10 minutes to download the entire data log. If the download
overlaps a mechanical motion by the APDA, then the data can be delayed by several seconds in the middle, or even
interrupted entirely. Small digital files (such as the last hourly record only) can be downloaded very quickly, and may be
accomplished at almost any time during the hour as long as the timing is carefully controlled. It is highly recommended
that the APDA clock be regularly synchronized by the external datalogger to prevent timing problems due to clock drift.
If a datalogger is programmed to digitally request data from the APDA-371 continuously throughout the hour (such as
every minute), then there will almost certainly be a number of requests each hour which will be ignored by the APDA
due to mechanical interrupts.