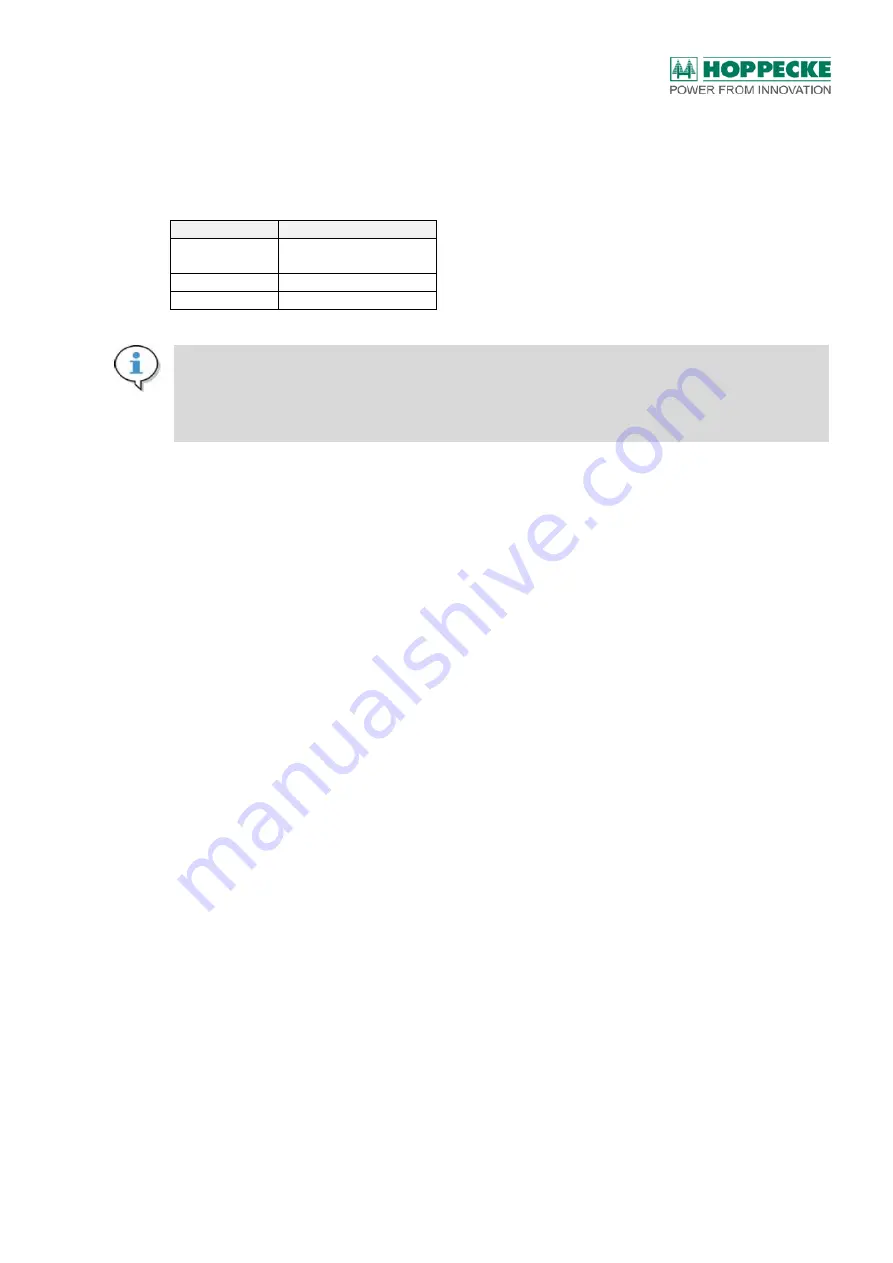
55
charging and discharging processes, the system only develops an approx. 8-10 K heating
level in comparison to the ambient temperature. The associated watt hour efficiency rates
η
Wh
of
trak | systemizer dynamics
systems are listed as examples for this configuration in
the following table:
Components
Efficiency rate η
Wh
Charging
technology
0.88
Battery
0.89
System
0.78
EN 16796-1:2015 "Efficiency Standard for Industrial Trucks"
Efficiency rate details have been determined based on a real vehicle charging profile, which
significantly exceeds the charging specifications in accordance with the above efficiency
standard.
7.6.
Service Life
The optimum service life of the
trak | systemizer dynamics
system depends on the
respective operating conditions.
The discharge depth (DOD) and temperature are significant influencing factors.
8.
Maintenance
8.1.
General
The electrolyte is immobilised sulphuric acid, i.e. the sulphuric acid is bound in a fleece
material. The density of the electrolytes cannot be measured.
•
Do not refill with water!
•
Never open cell valves!
If a valve is damaged, please immediately request a valve replacement from HOPPECKE
Customer Service.
The battery cells in the
trak | systemizer dynamics
system must always be kept clean and
dry in order to avoid leakage currents. Cleaning should be undertaken in accordance with
the ZVEI leaflet "Cleaning Batteries".
Damage to the carrier insulation must be repaired after the damaged site has been cleaned
with suitable material, in order to ensure insulation values in line with DIN EN 62485-3 and
avoid carrier corrosion.
Customer service must be contacted for the purpose of replacing cells.
8.2.
Installation
The
trak | systemizer dynamics
storage system must be removed from the vehicle in order
to carry out maintenance or service work, in order to ensure access to the components of
carriers, cells, charger and cabling.