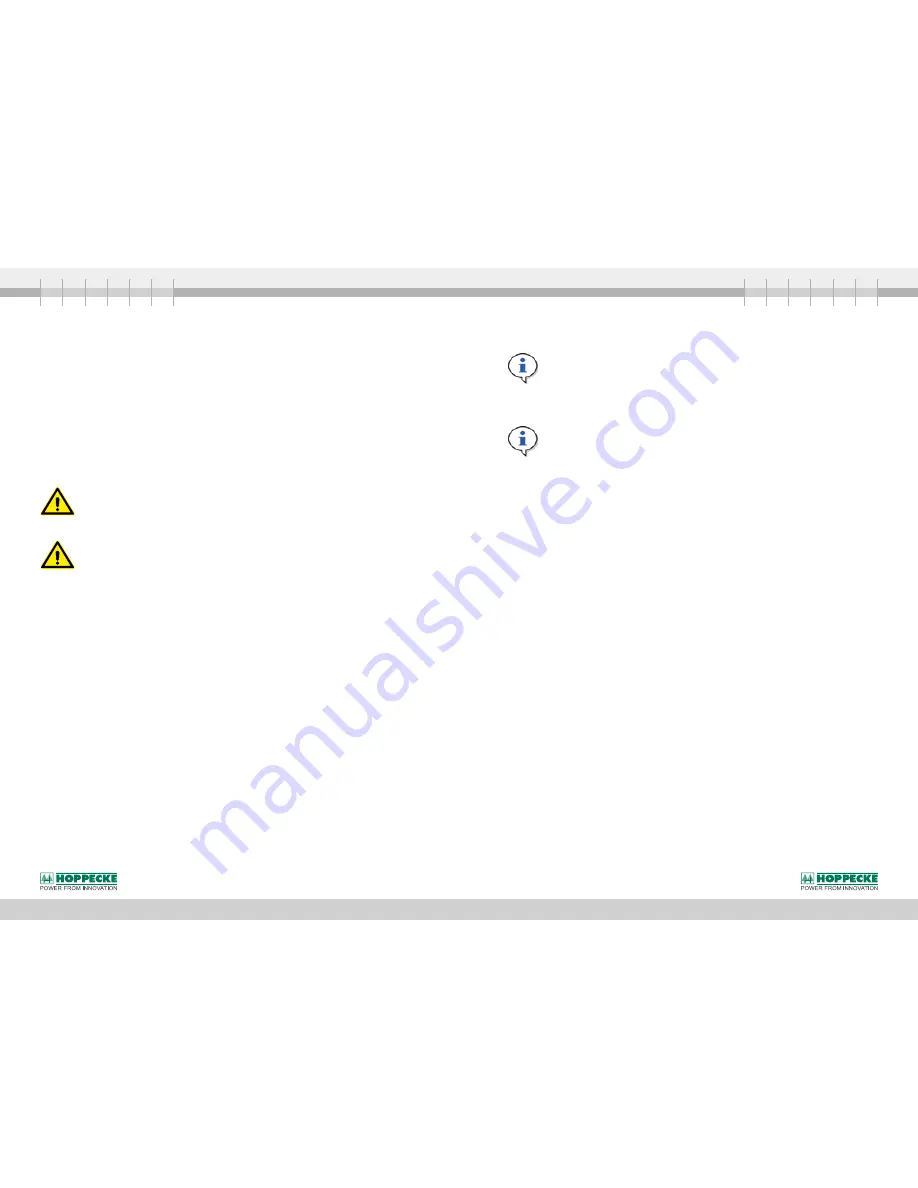
48
49
Installation, commissioning and operating instructions for valve-regulated stationary lead-acid batteries
7140203153 V1.4 (09.2018)
Installation, commissioning and operating instructions for valve-regulated stationary lead-acid batteries
7140203153 V1.4 (09.2018)
9 Testing the battery system
9.1 Performing the capacity test (short form)
For tests, proceed as directed in EN 60896-21: „Stationary lead acid batteries - Part 21: Valve
regulated types - Methods of test“ (IEC 60896-21:2004).
In addition, note special test instructions, e.g. in accordance with DIN VDE 0100–710 and DIN
VDE 0100–718.
The following is the short form of the procedure for testing the actual capacity of your battery system. Also
observe all instructions in
Chap. 9.2
.
We recommend performing an equalizing charge on the battery system (as described in Chap.
6.2.5) before performing this test.
Perform the equalizing charge no more than 7 days in advance and no less than 3 days in
advance!
1. Make sure that all connections are clean, secure and noncorroded.
2. During normal battery operation, measure and record the following parameters:
– Individual voltage of all cells or monobloc batteries.
– Surface temperature of at least one out of every ten cells or monobloc batteries.
– Voltage of the complete battery system.
3. Interrupt the connection between the battery system that you wish to test and the charger and all consumers.
4. Prepare an adjustable load that you can connect to the battery system.
The load current must correspond
to the maximum permitted current for which the battery is designed.
5. Prepare a shunt that you can connect in series with the load.
6. Prepare the voltmeter so that you can test the total voltage of the battery.
7. Connect the load, the shunt and the voltmeter. Simultaneously start a time measurement.
8. Keep the load current constant and measure the voltage of the battery system in regular time intervals.
9. Check the row connectors (block connectors), step connectors and tier connectors for excessive heating.
10. Calculate the capacity of the battery system using the following formula:
Capacity (% at 20 °C) = (T
a
/T
s
) x 100
T
a
= actual discharge time until the permitted minimum voltage is reached.
T
s
= theoretical discharge time until the permitted minimum voltage is reached.
11. Reconnect the battery system as originally connected and perform a boost charge
(see Chap. 5.13)
.
9.2 Performing the capacity test (extended version)
Preparation
The best and quickest method for preparing batteries for testing is the IU charge method, also used for equa-
lizing charges. Because it is possible to exceed the permitted load voltages, appropriate measures must be
taken, e.g. disconnection of the consumers.
The IU characteristic curve with increased voltage (2.33 - 2.40 V) x number of cells is the most common char-
ging characteristic used for commissioning the batteries.
The charge is performed with a constant voltage of max. 2.40 V/cell for up to 48 hours. The charge current
should not be higher than 20 A per 100 Ah nominal capacity. If the elcetrolyte temperature of the cells/blocs
exceeds the maximum of 45 °C, terminate the charge or switch to float charge to allow the temperature to drop.
8.2 Work to be performed annually
Take the following measurements and record the measurement values:
1. Voltage of the complete battery system.
2. Individual voltage of
all
cells or monobloc batteries.
3. Surface temperature of
all
cells or monobloc batteries.
4. Temperature in battery room.
5. Perform a visual check of
all
screwed connectors.
6. Check
all
screwed connectors to make sure that they are firmly secured.
7. Visual check of battery racks or battery cabinets.
8. Check to make sure that the battery room is properly ventilated and deaerated.
HOPPECKE recommends the use of a stationary battery monitoring system for the inspection of relevant data.
Please contact your local HOPPECKE representative for further information.
8.3 Cleaning of the battery
Danger!
Cleaning the batteries on a regular basis is necessary to maintain battery availability and to meet
accident prevention regulations.
Batteries should be cleaned at least once per year. Note the following points:
- While cleaning the batteries you must wear safety goggles and saftey clothes. To avoid electro-
static charges while handling the batteries your clothes, safety shoes and saftey gloves must
have a surface resistance of <= 10^8O hm.
Danger!
– Do not use dry cleaning cloth!
– Plastic parts of the batteries, especially the cell container, have to be cleaned with water or water moistened
cleaning cloth without additives.
- After cleaning the battery surface has to be dried with apporiate measures, like moist antistatic cleaning cloth
(e.g. cotton).