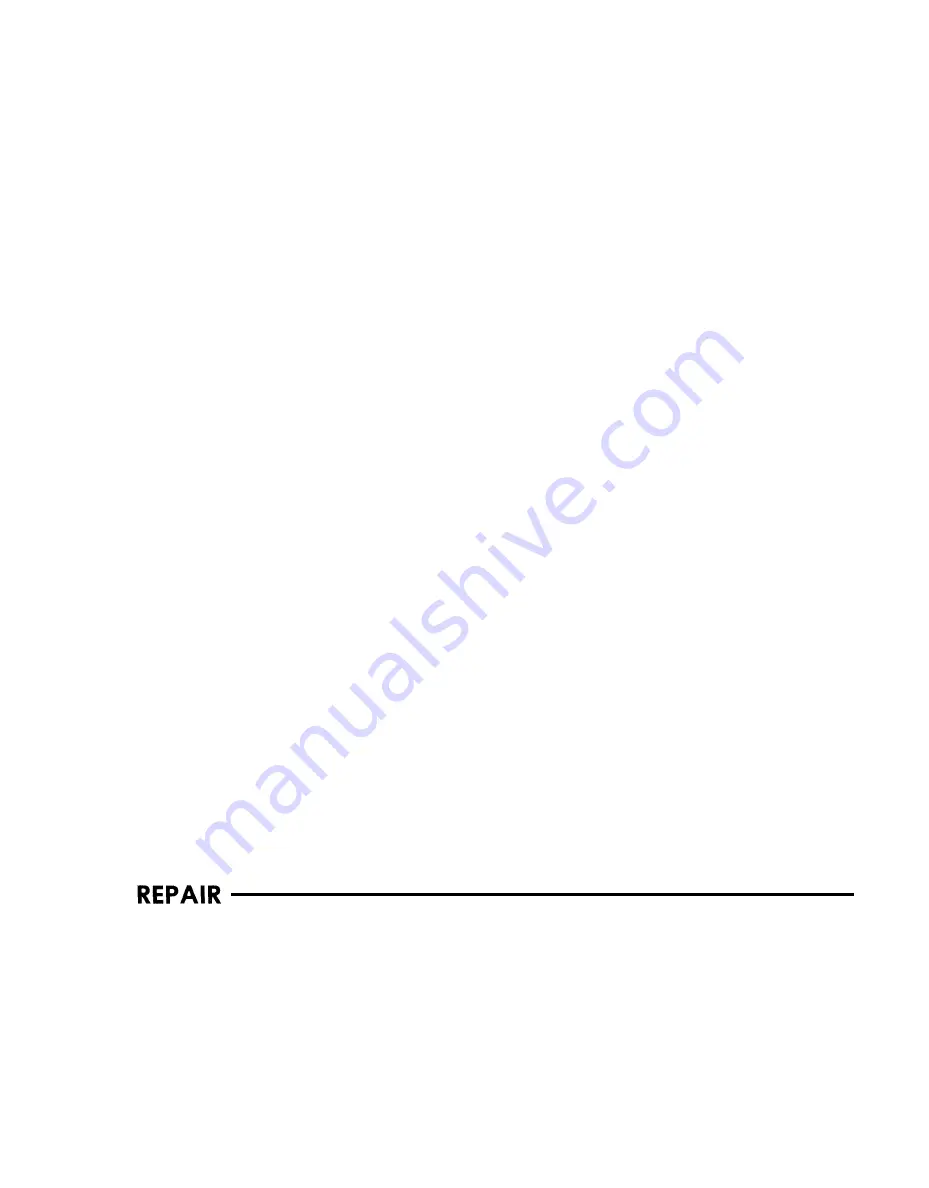
RUNS, BUT TANK SHOWS NO BUILD UP
Cut off building air supply to eliminate possibility of
broken lines by closing supply valve on tank. If unit still
fails to build up, remove air intake filter. If still no
success, disconnect copper lines connected to intake
valves (3/4 HP and up). While the unit is running, no air
should be coming out of the copper line. If air is coming
out of the line, the unloader pilot is stuck or defective.
It should be removed, cleaned and inspected. The un-
loader pilot is at the other end of the copper line. See
Parts List for details of unloader and pilot.
If unit is not equipped with unloading valves (1/4 to
1/2 HP are not), remove discharge tube and check for
air flow. Block with hand to check ability to build up.
If poor or no discharge air, disassemble and inspect valves.
If discharge is good, look for air leak between pump and
tank valve (cracked discharge tube, tank, etc).
BUILDS UP, BUT NOT COMPLETELY, OR TAKES
EXCESSIVE TIME
Cut off system by closing tank valve and check pump
up time (see Data Table II). Remove intake and recheck.
Disconnect copper line at intake valves (3/4 HP and up).
If air is coming out of line (while unit is running), dis-
assemble and clean unloader pilot located at other end
of line. See Parts List for details.
Another reason for poor delivery, in multicyclinder
units, could be a valve unloader sticking. The valve un-
loaders can be checked by disconnecting the copper line
leading to them and removing the cover bolts. Tapping
with a blunt instrument such as the handle of a large
screwdriver or small hammer, will loosen the cover so it
may be lifted off. Carefully remove the diaphragm; this
will expose the piston cup which operates the unloader.
With the unit running, manually depress the piston.
There should be a distinct change in the intake sound
indicating the valve is being held open. Slowly depressing
the piston, you should first feel the resistance of the
return spring, then the piston contacting the intake
valve, then the sound change is you move the valve off
the seat. Use fingernails to remove this piston cup for
cleaning beneath, if necessary.
If the source of the trouble has still not been located,
remove and inspect intake and exhaust valves for dirt or
warpage. (NOTE: The head must be removed on the 1/2
HP unit to service valves as they are not removable.) The
piston top and cylinder walls can be inspected at this
time.
PUMP SLOWS, STALLS, OR GOES OUT ON OVER-
LOAD
This is probably the result of the pump seizing. Check
oil level (and pressure in 1 HP and up).
Check tank pres-
sure, should be 90 psi or lower. (On WP240 units, turn
off power to both motor-pump units.)
Remove belt and bleed down tank. Turn pump by
hand, it should turn freely. If it does, motor may be
defective. If it does not, it may be the pump or a
plugged aftercooler tube. Disconnect discharge tube and
turn pump by hand again. If still hard turning, problem
is internal to the pump. If it now turns freely, check
piping to tank for obstructions.
EXCESSIVE VIBRATION
Usually due to omission of vibration pads or an
uneven weight distribution on the pads. Check this by
shutting off unit and applying your weight to the dif-
ferent corners of the unit. Excessive rocking should be
shimmed out. In very uneven floors, adjustable levelers
may be needed.
Belt guards often produce a vibrating noise even
under normal operating conditions. Readjusting will
usually eliminate this.
In some cases, the normal operation of the com-
pressor is considered excessive noise or vibration. In
these cases a remote air intake, adjustable pads, and air
line vibration isolators may be required, Isolators are
stocked in the commercial warehouse.
PUMP REMOVAL AND REPLACEMENT
Shut off power, drain oil, and bleed down tank.
Remove belt guard, loosen motor mounts and remove
belt(s).
Remove aftercooler tube at pump end. If tube is type
which wraps around crankshaft, then remove both ends
and any hold down straps.
If flywheel is accessible, then remove at this time;
otherwise it can be removed afterward if necessary. The
1/2 HP unit is held on with a keyed shaft and setscrew
and will probably need a puller. All others use a split
hub and key and can be removed by removing hub bolts
and nuts and driving a wedge into split.
Remove pump intake filter and the unloader air
supply line (3/4 HP and up). Remove pump hold down
bolts and remove pump. (CAUTION: If flywheel has not
7
75-7131
Summary of Contents for WP230A-M
Page 19: ......