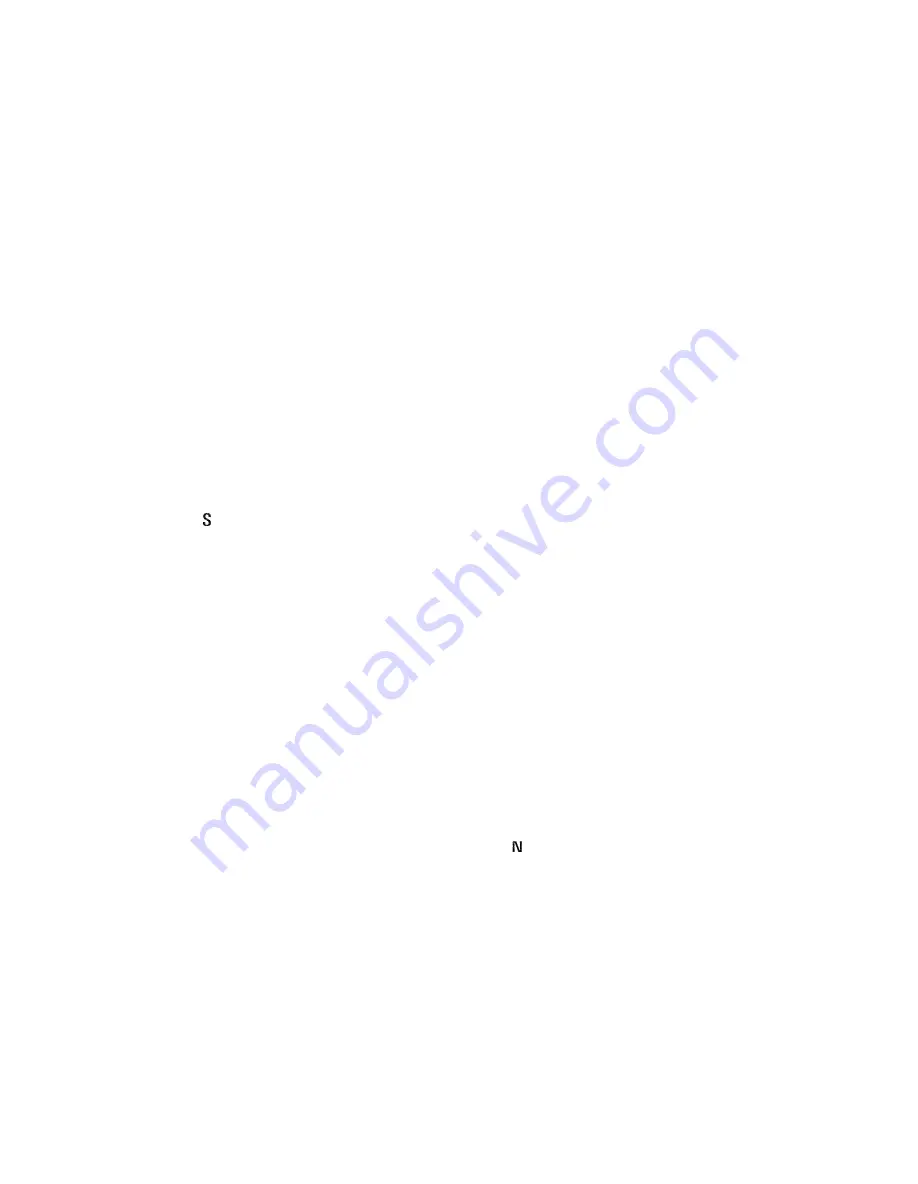
If it is impossible to get sufficient oil pressure, check
the oil pump and pressure gauge by unscrewing the
pressure gauge until oil seeps out around the threads
during operation of the compressor. This will indicate
that oil pressure is reaching the system and confirms
operation of the pressure gauge. The compressor requires
oil pressure to pump and to operate intake valve un-
loaders. Lack of pumping ability is a good indication of
loss of oil pressure. If oil appears at the threads of the
gauge and the oil pressure gauge indicates no pressure,
the gauge is probably faulty and should be replaced. If
no oil appears at the threads of the gauge, this is an
indication of possible oil pump failure.
If the oil pump must be replaced, refer to the “Oil
Pump Replacement” section for instructions on removal
and repair of the oil pump housing. In cases of low (not
zero) pressure, the cause may be excessive wear in the
pumping unit. Pump up time should be checked against
the table. Listen for unusual knocks which might indicate
worn bearings.
1/4 HP..
. . . . . . . . . . . . . . . . .
.OverYear
1/2 HP. . . . . . . . . . . . . . . . . . .
.OverYear
3/4 HP..
. . . . . . . . . . . . . . . . . .
Over Year
1 HP . . . . . . . . . . . . . . . . . . . . . .
*Over Year
1-1/2 HP..
. . . . . . . . . . . . . . . . .
*Over Year
2 H P
. . . . . . . . . . . . . . . . . . . . . . .
280Days
3HP . . . . . . . . . . . . . . . . . . . . . . .
190Days
5HP . . . . . . . . . . . . . . . . . . . . . . .
115Days
7-1/2 HP.
. . . . . . . . . . . . . . . . . . .
75Days
10 HP. . . . . . . . . . . . . . . . . . . . . . .
55 Days
15 HP
.......................
40Days
20
HP. . . . . . . . . . . . . . . . . . . . . . . 28 Days
2. Make certain the proper grade of oil is being used
AND THE COMPRESSOR IS NOT BEING OVER-
FILLED. Over filling always causes high oil con-
sumption Oil level should never be above the high
mark on the dipstick.
3. Check for leaks.
4, Check intake filter/piping and crankcase breather
valve for cleanliness and obstructions. Restricting
the intake air will cause higher oil consumption.
OIL LEAK
Most common oil leaks occur around screws and
gaskets. They generally can be corrected by tightening
the screw or replacing the gasket. If you are unable to
locate the source of the leak, clean the unit thoroughly
and sprinkle the areas suspected with baby powder.
Make certain not to get any baby powder into the intake.
Recheck the device after several hours and the leak
should be more easy to locate.
Excessive oil on the after cooler pipe or compressor
head usually indicates air leaks. Locate these with a soap
and water solution when the unit is operating. The un-
loaders should also be checked while the compressor is
in the “off” cycle because they are pressurized during
that time.
EXCESSIVE OIL CONSUMPTION
Oil consumption is a difficult problem to resolve and
the following steps should be taken before any repairs
begin.
1. Confirm the Complaint-Oil at the tank drain does
not necessarily indicate high oil consumption.
A 20 HP unit may consume a pint of oil in two
weeks and still be within specification, Since oil
is commonly available in quarts, the following is
the minimum number of days a quart should last
(assuming 50 percent or less operating cycle).
5. Check for excessive oil pressure or high percent
operation. If after performing the above, it is still
considered an oil consumer with no apparent ex-
ternal cause, then:
a. With the valve to the system closed, check
pump up and cycle pressures against the values
in the data table. Differences greater than 10
percent indicate worn parts.
b. Remove valves (the l/2 HP unit does not have
removable valves so the head must be removed)
and examine piston top. Oil wetted is acceptable
but any accumulation of oil indicates a defective
pump .
OISY PUMP
The most common rea son for a noisy pump is a loose
flywheel or motor pulley. Check these first; then check:
1. Oil pressure-if low, check pump as described above.
Lack of oil pressure may have caused bearing
damage.
2. Valve assemblies-make certain they are tight.
3. Wrist pin or connecting rod bearings-stop pump
and remove belts. Rotate pump back and forth a
couple of inches, using the flywheel. If knock can
be heard, it is probably a bad wrist pin or
5
75-7131
Summary of Contents for WP230A-M
Page 19: ......