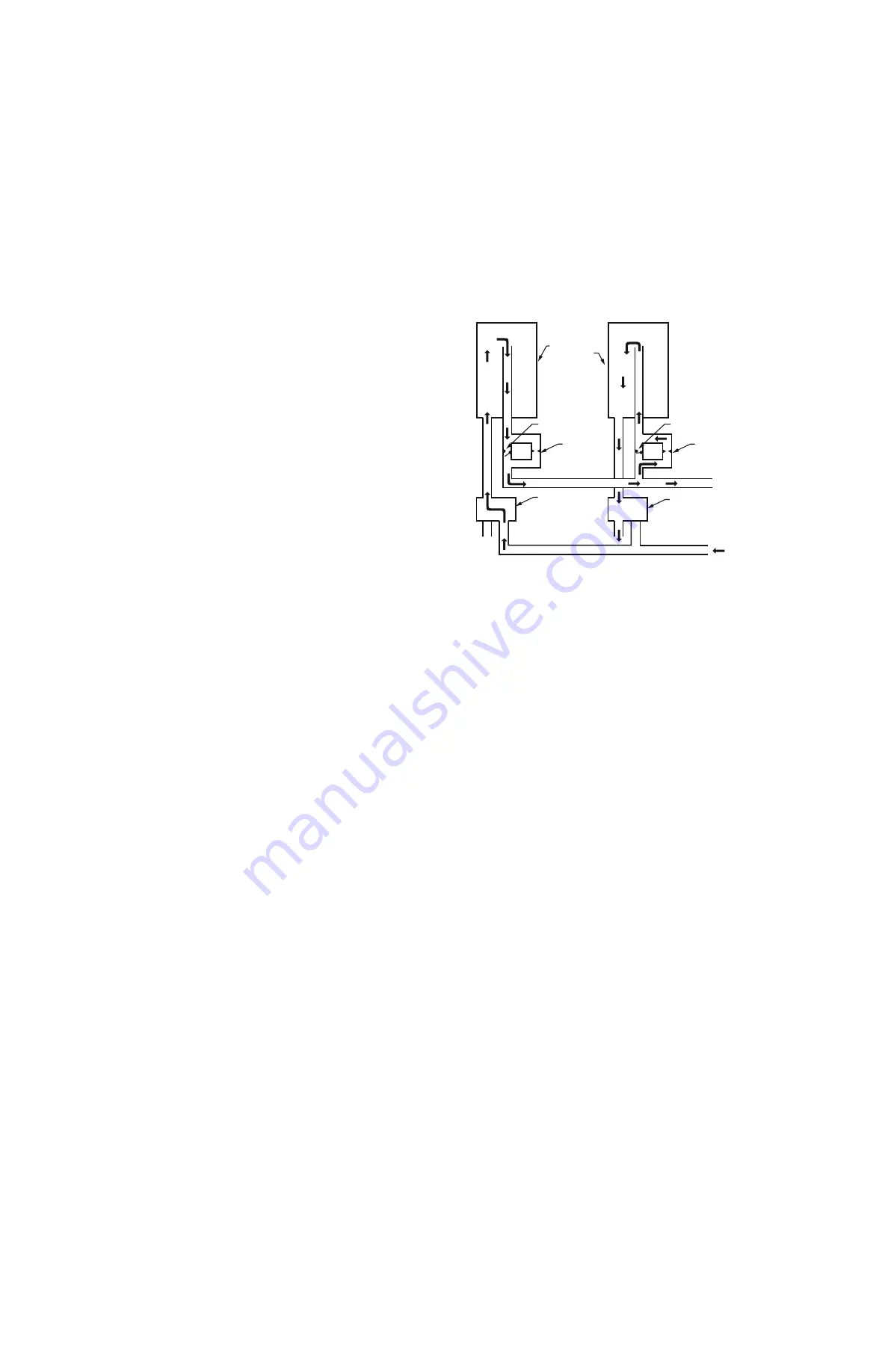
Air Supply Equipment
132
customer.honeywell.com
70-6925
The refrigerant dryer uses a non cycling operation with a hot
gas bypass control on the refrigerant flow to provide a constant
dew point of approximately 35F at the tank pressure. The
refrigeration circuit is hermetically sealed to prevent loss of
refrigerant and lubricant and to protect against dirt.
The heat exchanger reduces the temperature of the
compressed air passing through it. A separator/filter condenses
both water and oil from the air and ejects the condensate
through a drain. A temperature-sensing element controls the
operation of the refrigeration system to maintain the
temperature in the exchanger.
With a dew point of 35F and an average compressor tank
pressure of 80 psi, air is dried to a dew point of 12F at 20 psi.
Under severe winter conditions and where piping and devices
are exposed to outside temperatures, the 12F dew point may
not be low enough.
DESICCANT DRYING
A desiccant is a chemical that removes moisture from air. A
desiccant dryer is installed between the compressor and the
PRV. Dew points below -100F are possible with a desiccant
dryer. The desiccant requires about one-third of the process air
to regenerate itself, or it may be heated. To regenerate,
desiccant dryers may require a larger compressor to produce
the needed airflow to supply the control system and the dryer.
It may be necessary to install a desiccant dryer after the
refrigerant dryer in applications where the 12F dew point at 20
psi mainline pressure does not prevent condensation in air lines
(e.g., a roof-top unit exposed to severe winters).
The desiccant dryer most applicable to control systems uses
the adsorbent principle of operation in which porous materials
attract water vapor. The water vapor is condensed and held as
a liquid in the pores of the material. The drying action continues
until the desiccant is saturated. The desiccant is regenerated by
removing the moisture from the pores of the desiccant material.
The most common adsorbent desiccant material is silica gel,
which adsorbs over 40 percent of its own weight in water and is
totally inert. Another type of adsorbent desiccant is the
molecular sieve.
A desiccant is regenerated either by heating the desiccant
material and removing the resulting water vapor from the
desiccant chamber or by flushing the desiccant chamber with
air at a lower vapor pressure for heatless regeneration. To
provide a continuous supply of dry air, a desiccant dryer has
two desiccant chambers (Fig. 15). While one chamber is being
regenerated, the other supplies dry air to the system. The
cycling is accomplished by two solenoid valves and an electric
timer. During one cycle, air passes from the compressor into the
left desiccant chamber (A). The air is dried, passes through the
check valve (B), and flows out to the PRV in the control system.
Fig. 15. Typical Heatless Desiccant
Dryer Airflow Diagram.
Simultaneously, some of the dried air passes through the orifice
(G) to the right desiccant chamber (E). The air is dry and the
desiccant chamber is open to the atmosphere, which reduces
the chamber pressure to near atmospheric pressure. Reducing
the air pressure lowers the vapor pressure of the air below that
of the desiccant, which allows the moisture to transfer from the
desiccant to the air. The timer controls the cycle, which lasts
approximately 30 minutes.
During the cycle, the desiccant in the left chamber (A) becomes
saturated, and the desiccant in the right chamber (E) becomes
dry. The timer then reverses the flow by switching both of the
solenoid valves (D and H). The desiccant in the right chamber
(E) then becomes the drying agent connected to the
compressor while the desiccant in the left chamber (A) is dried.
The process provides dry air to the control system continually
and requires no heat to drive moisture from the desiccant. A
fine filter should be used after the desiccant dryer to filter out
any desiccant discharged into the air supply.
A heated dryer also has two chambers where one is heat-
regenerated while the other dries the compresses air.
Periodically, the regenerating and drying action is switched.
Pressure Reducing Valve Station
The pressure reducing valve station is typically furnished with
an air filter. The filter, high-pressure gage, high pressure relief
valve, pressure reducing valve (PRV), and low-pressure gage
are usually located together at one point in the system and may
be mounted directly on the compressor. The most important
elements are the air filter and the PRV.
C1889
DESICCANT
CHAMBERS
CHECK
VALVE
CHECK
VALVE
ORIFICE
ORIFICE
SOLENOID
A
B
C
D
DRY AIR OUT
H
G
F
E
AIR FROM COMPRESSOR
SOLENOID
Summary of Contents for VP525C
Page 58: ...50 customer honeywell com 70 6925 ...
Page 120: ...112 customer honeywell com 70 6925 ...