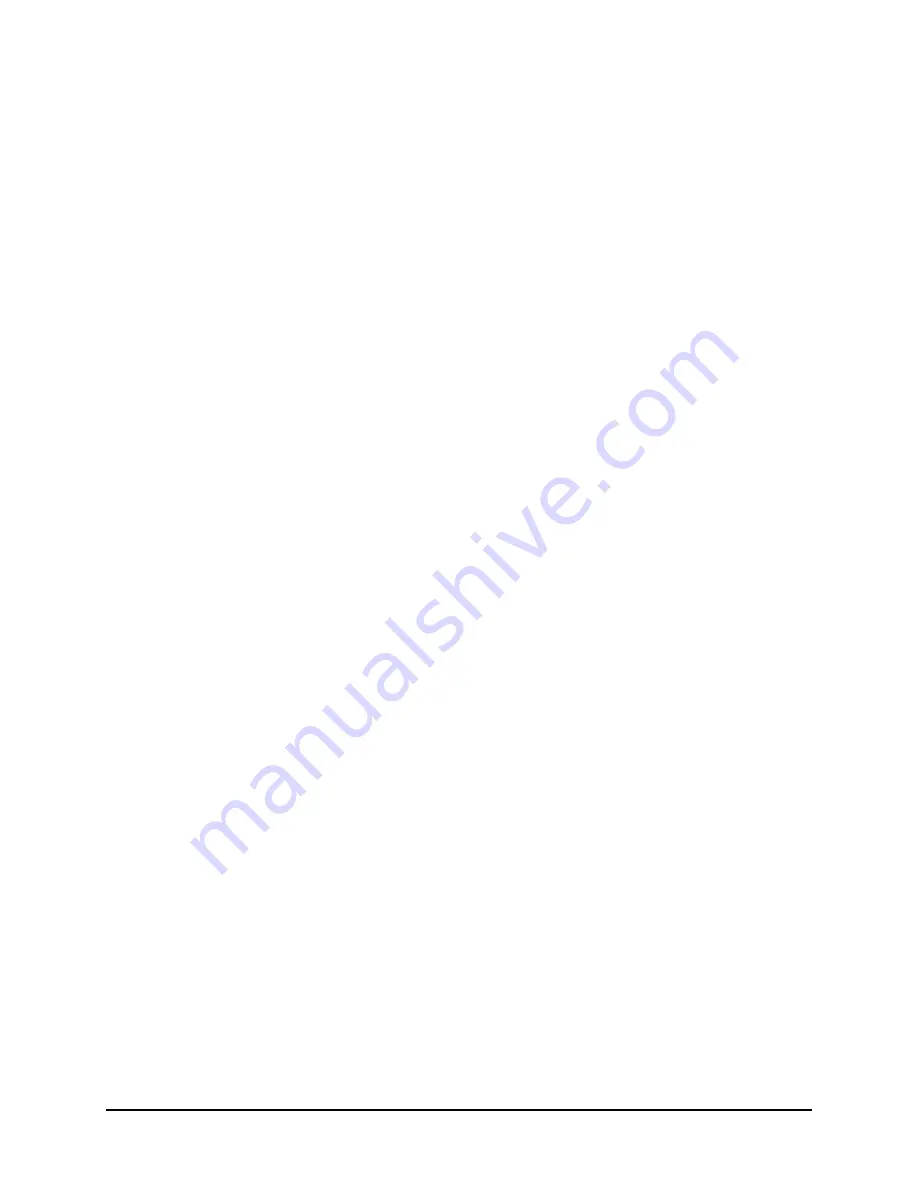
ii
DC1010/1020/1030/1040 Product Manual
8/05
Copyright
,
Notices and Trademarks
Printed in Taiwan - © Copyright 2005 by Honeywell
Revison 1 - August 2005
WARRANTY/REMEDY
Honeywell warrants goods of its manufacture as being free of defective materials and faulty
workmanship. Contact your local sales office for warranty information. If warranted goods are
returned to Honeywell during the period of coverage, Honeywell will repair or replace without charge
those items it finds defective. The foregoing is Buyer's sole remedy and is
in lieu of all other
warranties, expressed or implied, including those of merchantability and fitness for a
particular purpose
. Specifications may change without notice. The information we supply is
believed to be accurate and reliable as of this printing. However, we assume no responsibility for its
use.
While we provide application assistance personally, through our literature and the Honeywell web
site, it is up to the customer to determine the suitability of the product in the application.
Industrial Measurement and Control
Honeywell Korea
191 HanGangRo 2ga, YongSanGu
Seoul, Korea
Summary of Contents for DC1000 SERIES
Page 48: ...Configuration 40 DC1010 1020 1030 1040 Product Manual 8 05 ...
Page 59: ......