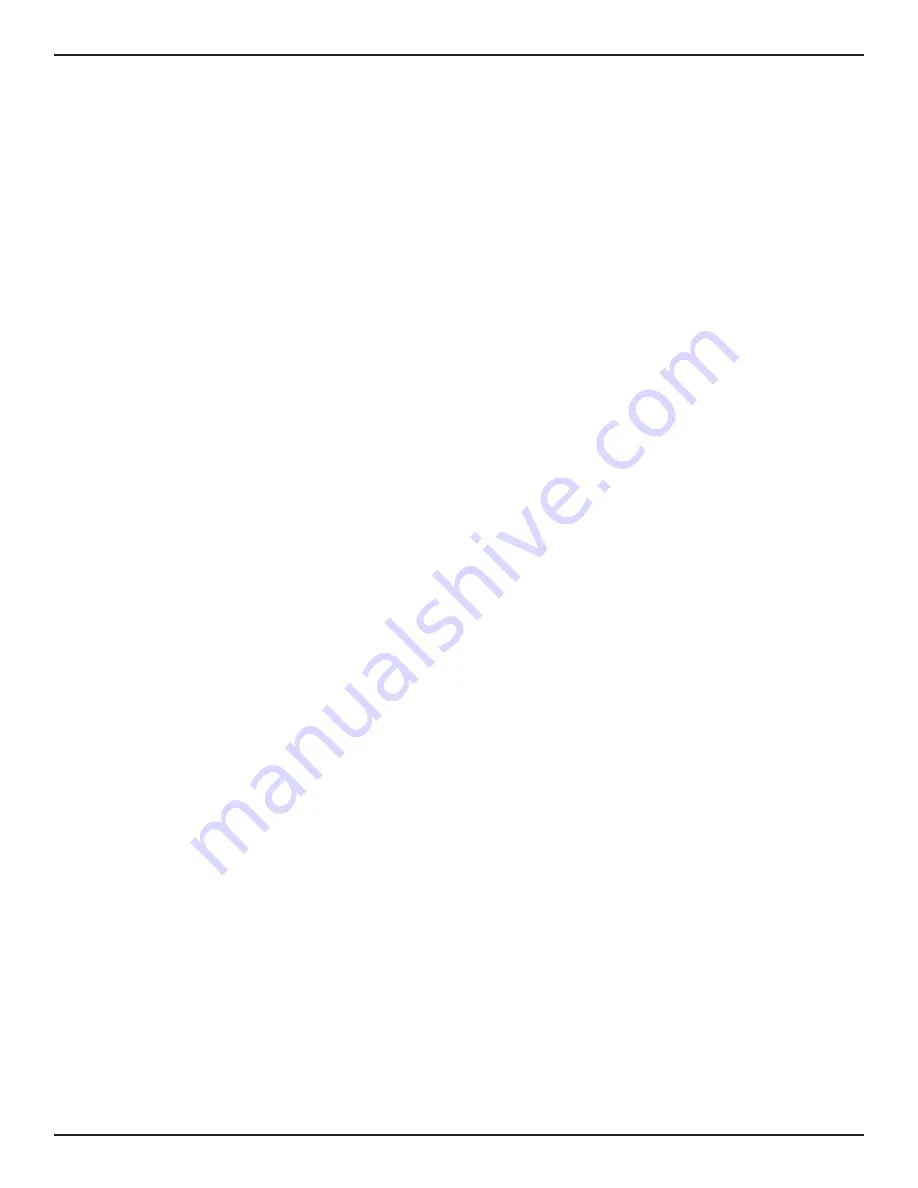
- 6 -
ABRASIVE SELECTION
1.
The kind of media you choose will greatly influence the amount of time needed to clean a given
surface area. Abrasive media materials include glass bead, crushed garnet, crushed walnut shell
etc… DO NOT USE SAND OR SILICA BASED ABRASIVES.
2.
A high moisture content of the media can cause blockage in the media metering valve. Be sure to
use dry media that is stored in a low-humidity environment. Only use O.S.H.A. recommended abra-
sives.
3.
If you elect to reuse media, remember it does wear out. If the sharp edges become more round
and are less effective, then replace with fresh media.
LOADING ABRASIVE MEDIA INTO THE TANK
1.
Check your abrasive to be sure it’s dry and won’t clog the meter valve (18B), sand outlet pipe (22),
hose (24), or other components.
2.
Put on the protective clothing.
3.
Turn the air supply valve (18) to the off (horizontal) position.
4. Open the nozzle shut off valve (42) (vertical position).
5.
Watch the pressure gauge (15) and make sure it reads zero pressure.
6.
Remove the filler cap (12) from the top of the tank.
7.
Insert the funnel (29) and pour the abrasive media into the funnel. Be sure to get enough into the
tank to do the job at hand. But if this is a big job, fill the tank only ¾ full. It is better to reduce the
amount of abrasive, load it more frequently, and empty the water trap more often. This will reduce the
possibility of clogging the bottom of the tank or the line.
8.
With the correct amount of abrasive in the tank, close the filler cap (12).
9.
Close the nozzle shut-off valve (42) and open the air supply valve (18).
10.
Check for air leaks at the filler cap as you begin to pressurize the tank from the compressor.
MAINTENANCE
1.
You should make every effort to protect your air compressor from any damage it may receive from
your abrasive media work. Your best option is to keep the compressor in a room separate from the
pressure pot. Use a long hose to provide the PSI needed to do your work. A second choice is to keep
the compressor up wind from the work area. The greater the distance, the better. Other than that, you
should continue standard maintenance procedures for the compressor.
2.
Some parts of the pressure pot will wear much more rapidly than others. The parts needing close
attention carry the air/abrasive mixture starting with the media hose (24) and going through the metal
fittings, the shut off valve (42C) and the ceramic nozzles (37/38).
3.
If air leaks develop in any of these parts you should stop all work and find what needs to be re
-
paired or replaced. When it’s new, the media hose (24) has 2 cord piles and the walls are ¼” thick.
As the interior diameter has media running through it, this wall becomes thinner and thinner. One way
to inspect the hose and other parts affected by the blasting is to put on your protective clothing. The
pressurized the system and close the nozzle shut off valve (42C). Close your hand loosely around the
hose and run it up and down the hose across the fittings and nozzles. You’ll be able to feel any leaks.
You can also spot places in the hose where the wall is getting very thin. These show up as blisters in
the hose. If you find such a blister, get a new hose immediately. If that blister breaks, the abrasive will
come out of the side of the hose at 65 or more PSI.
Summary of Contents for RD00913191
Page 2: ...2...