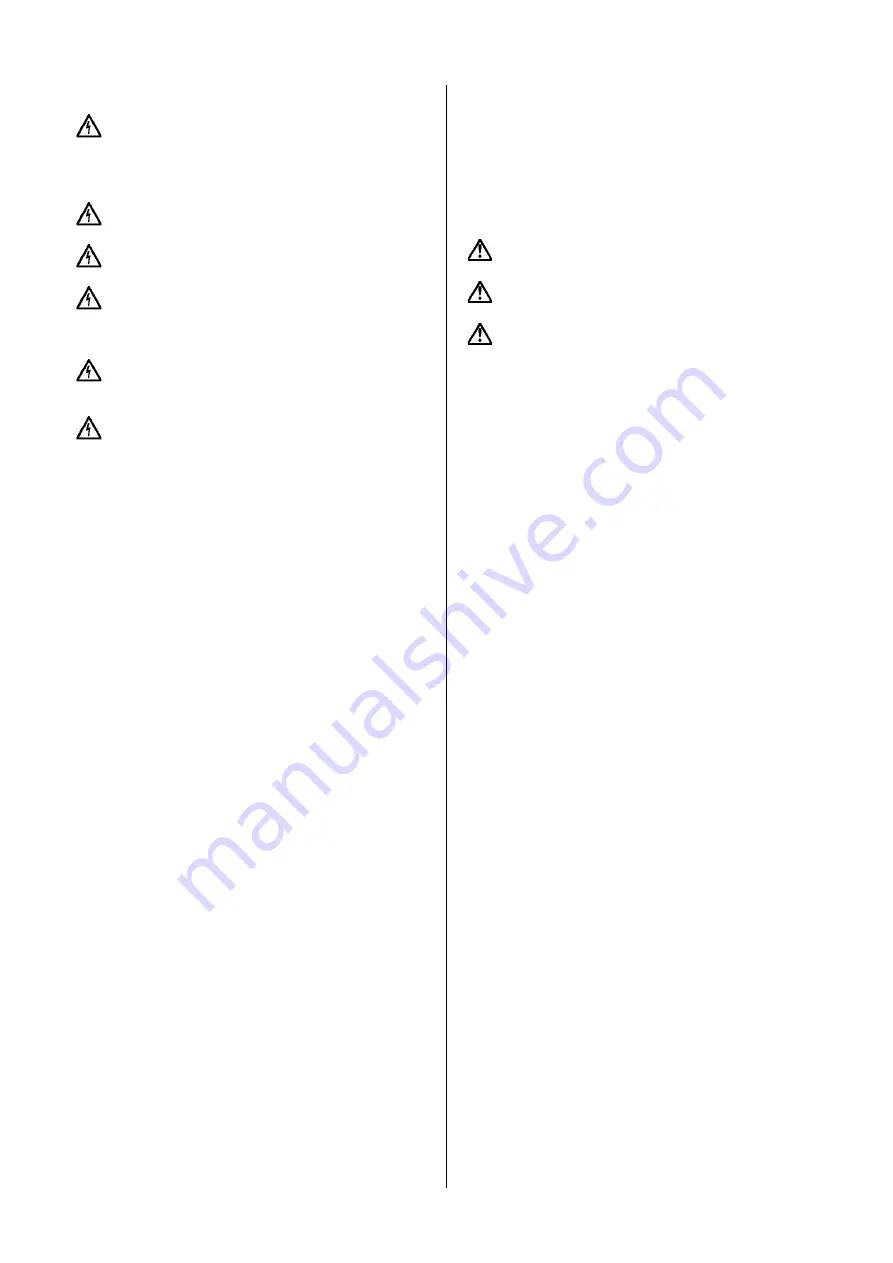
11
6. Electrical Connection
Before operation, an expert check must secure that
the required electrical protection measures exist. The
connection to ground, earthing, isolating transformer, fault
current breaker or fault voltags circuit must correspond to
the guidelines set forth by the responsible power plant.
The voltage required in the technical data sheet
must correspond to the existing line voltage.
Submersible pumps used outside of buildings must
have a cable with a minimum length of 10m.
Make sure that the electrical pin-and-socket connec-
tions are installed flood- and moisture-safe. Before start-
ing operation check the cable and the plug against dam-
ages.
The end of the pump power supply cable must not be
submerged in order to prevent water from penetrating
through the cable into the motor.
The normal separate motor starter/control box of
standard as well as of explosion proof pumps must
not be installed in explosive enviroments.
6.1. Connection of 1 Ph-Motors
H 501 and H 505 pumps with 1Ph-motors are supplied
with 10 m of cable and plug.
H 502 and H 506 pumps with 1Ph-motors are supplied
with or must be connected to a seperate control box with
motor starter and operating capacitor. If any other than an
original HOMA control unit is used, make sure that the
thermal relay in the motor starter is set according to the
nominal current consumption of the pump motor (see
data on pump label).
6.2. Connection of 3 Ph-Motors
Pumps with 3Ph-motors are supplied with or must be
connected to a separate control box with motor starter,
available from the HOMA accessory program. If any other
than an original control unit is used, make sure that the
thermal relay in the motor starter is set according to the
nominal current consumption of the pump motor (see
data on pump label).
6.3. Temperature Sensors
The pumps have a set of temperature sensors built in the
stator windings. The contact of these sensors opens in
case of overtemperature and switches off the motor
power supply.
6.4. Check of Direction of Rotation
1 Ph-pumps do not require any check, as they always run
with the correct direction of rotation.
3 Ph-pumps must be checked for correct direction of rota-
tion before start-up. On original HOMA control boxes a
control-light is illuminated, if the direction of rotation is not
correct.
With smaller pumps the direction of rotation may be
checked by watching the start-jerk.
Put the pump ver-
tical on the ground and lift one edge. Start the motor.
Viewed from above, the unit must jerk anti-clockwise, as
the correct direction of rotation is clockwise. With bigger
pumps the check may also be done by watching the rota-
tion of the impeller
through the discharge or the suc-
tion inlet. Pumps which are already installed, the
check may be done by comparing head (pump pressure)
and flow (quantity of water) at different direction of rota-
tion.
The direction that gives hig-her head and flow is
the correct one
.
If the direction of rotation is wrong, interchange two of the
phases of the electric power supply. Using an original
HOMA control box with CEE-plug, this may be done by a
180° turning of the small round pole-socket at the plug-
end with a screwdriver.
7. Installation
Pay attention to the maximum depth of immersion
(see pump label).
If the pump is installed in a sump, the sump opening
must be covered with a tread-safe cover after installation.
The operator has to prevent damage through the
flooding of rooms caused by defects of the pump through
the use of appropriate measures (e.g. installation of alarm
units, backup pump or like that).
7.1. Submerged installation
⇒
Fix the pressure tube at the Storz-fixed hose-coupling
(equipment supplied at H 502 and H 506) or STA
hose-coupling at the central top discharge. Make sure
that the hose is not snap off. The hose must co-
ordinate with inside diameter from the discharge.
⇒
Place the pump into the medium. If the bottom of the
sump is soft or muddy then it is recommended that a
solid foundation of stones or something similar is pro-
vided. Make sure that the inlet suction strainer of the
pump is free and clear of any obstructions.
7.2 Automatic Float Switch Control
The pumps may be supplied with float switch level con-
trollers. They start and stop the pump according to the
liquid level in the pit.
The difference in level between start and stop must be
adjusted by adjusting the free swinging length of the ca-
ble between the float switch and the cable fastening.
Long cable end:
Large difference in level.
Short cable end:
Small difference in level.
Never place the float switch from the three phase pumps
in the sump without fixing the float switch cable to a fixed
point in the sump, because the float switch needs a rota-
tion around the fixing point of the cable to operate without
any problems. Non-observance may cause an overflow
because the pump does not start running or a dry run of
the pump in fact that the pump does not stop, which will
destroy the pump.
The stop level must be adjusted in such a way, that the
pump stops before the liquid level is lowered below the
top of the pump volute.
The start level must in any case be below the bottom of
the liquid inlet pipe of the pit.
Note: Only the proper adjustement and fixing of the float
switch cable will guarantee a reliable pump operation. Af-
ter any modification of the float switch adjustment the
function must be checked by a test-run of the pump.
Summary of Contents for H 501 Series
Page 2: ...2 Inhalt Contents Seite 3 Page 9 Seite 12 Page 12 DEUTSCH ENGLISH Bauma e Dimensions...
Page 14: ...14 13 Bauma e Dimensions in mm...
Page 15: ...15 Notizen...
Page 16: ...16...