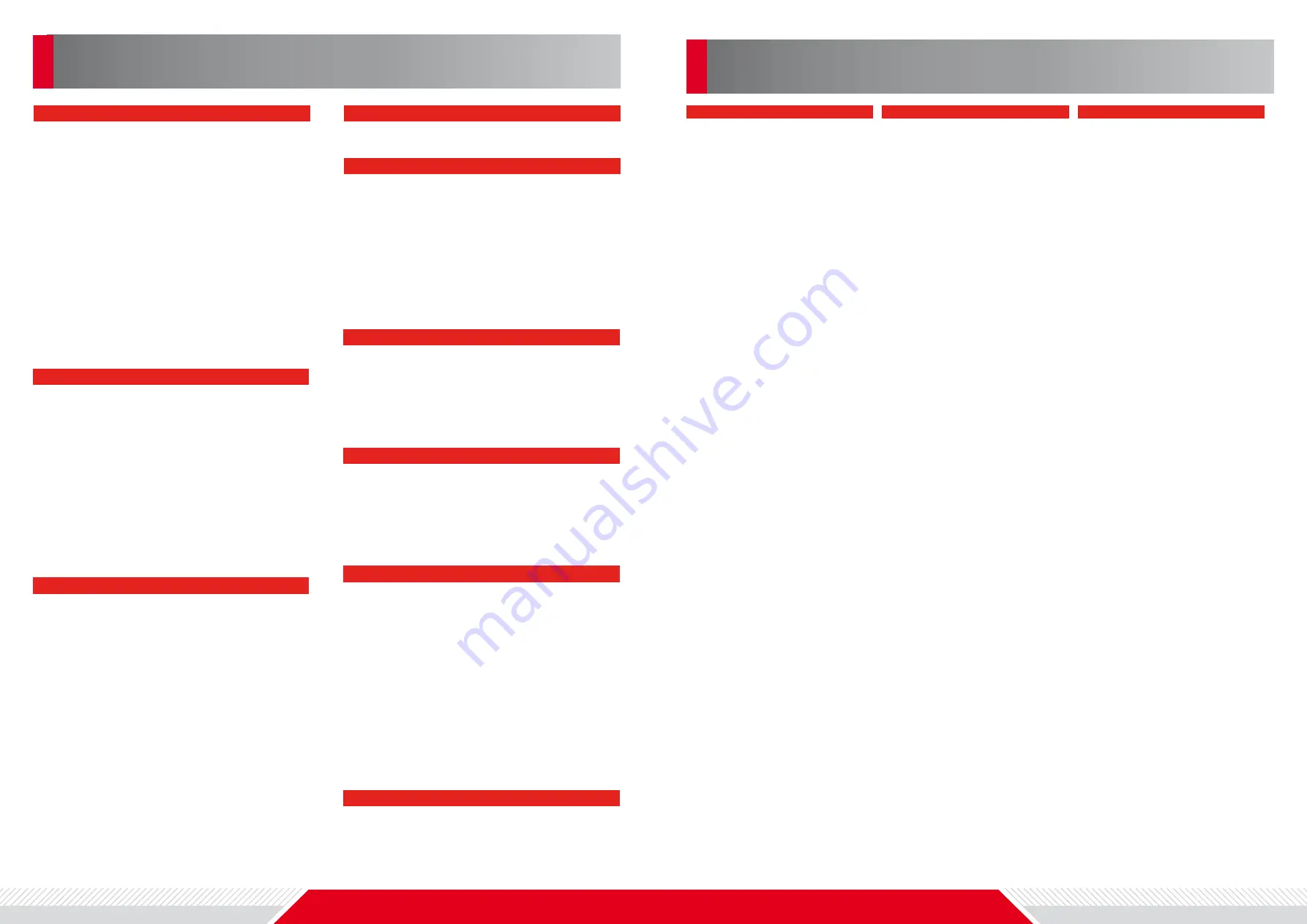
www.holzmann-maschinen.at
Open the BELT GUARD (1)
Loosen the BELT TENSION LOCK HANDLE (3)
Loosen the belts with the BELT TENSION
HANDLE (4)
Arrange the belts into position according
to the DRILL SPEED CHART (2)
Tension the belts accordingly (Do not
overtension or you will ruin the bearings)
with the BELT TENSION HANDLE (4) and
fix the chosen tension level with the BELT
TENSION LOCK HANDLE (3).
Close the BELT GUARD (1) again
Loosen the SUPPORT LOCK (24)
You can vary the table height with the TA
-
BLE CRANK (9)
You can swing the TABLE (13) around the
column, the rack will follow.
You can tilt the TABLE (13) by loosening
the TABLE BEVEL LOCK (25) and tilting
the table to the desired angle, which
you can read off from the TABLE BEVEL
SCALE(23)
Be sure to keep chuck and arbor tidy and
dry.
Insert the ARBOR in to the CHUCK (18)
Insert the arbor into the quill
To remove the drill chuck turn the Quill
down with the FEED HANDLE (6) and in
-
sert the WEDGE KEY into the slot.
Hit the key end with a wooden or rubber
hammer to release the arbor.
Hold with your left hand the chuck in or
-
der to prevent it from dropping onto the
table.
CHANGE SPEED
CHANGE TABLE POSITION
CHUCK INSTALLATION
With the DRILL ON-OFF SWITCH (21)
Set DEPTH SCALE INDICATOR (16) to
Zero.
Move Chuck downwards with FEED HAND
-
LE (6) until desired depth is reached.
Read depth off the DEPTH SCALE
INDICATOR(16)
Tighten the DEPTH SCALE LOCK (17).
With the SB 4132LR model you can choo
-
se the running direction of the spindle with
the switch on the gearhead.
Put the switch into 0 Position and wait until
the spindle stands still before you change
running direction.
You can adjust the feed tension with the
FEED SPRING ADJUSTMENT without re
-
moving the SPRING CAP (20).
This makes sense when the quill returns
too fast or too slow.
All ball bearings are sealed and require no
further lubrication.
You should lubricate the table elevation
mechanism, namely the rack, wormgear
and handle.
Furthermore lubricate with grease the
spindle/quill.
Coat regularily the table and ground plate
as well as all other non coated metal parts
with a thin layer of anticorrosion oil-based
solvent.
Frequently blow out any dust that may ac
-
cumulate inside the motor.
Clean the table etc. from metal and wood
chips and dust after every usage.
SWITCH MACHINE ON/OFF
DETERMINE DRILLING DEPTH
FEED SPRING ADJUSTMENT
LUBRICATION
4. OPERATION & MAINTENANCE
CLEANING
5. TROUBLESHOOTING
Noisy Operation
Drill bit burns
Drill bit leads off to a direc
-
tion, hole not round
Wood splinters on undersi
-
de
Drill bit stalls in material
Excessive drill bit runout or
wobble
Quill returns too slow / too
fast
Chuck does not stay atta
-
ched to spindle or it falls off
when trying to install it
PROBLEM
PROBABLE CAUSE
SOLUTION
1.
Incorrect belt tension
2.
Dry Spindle
3.
Loose Spindle pulley
4.
Loose motor pulley
1.
Incorrect speed
2.
Chips not coming out
of hole
3.
Dull drill bit
4.
Feeding too slow
5.
Not lubricated
1.
Hard grain in wood
2.
Cutting lips of bit not
equally long or have
not equal angles
3.
bent drill bit
4.
Spindle bearings too
loose
1. No back-up material
on underside of
workpiece
1.
To high feed rate
2.
dull drill bit
3. Inproper belt tension
4.
Bit not suitable for
material or material
too hard (e.g. some
stainless steel types)
1.
Bent drill bit
2.
Worn spindle bearings
3.
Drill not properly
installed in chuck
4.
Chuck defect
5.
arbor or chuck
surface dirty
1. Inproper spring
tension
1.
arbor, chuck or quill
surface dirty, greasy
1.
Adjust tension
2.
Lubricate spindle
3.
Check tightness of
retaining nut on
pulley and tighten if
necessary
4.
Tighten setscrews in
pulleys
1.
Change speed
2.
Retract drill bit
frequently to clear
chips.
3.
Resharpen drill bit
4.
Faster feed speed
5.
Lubricate drill bit
1.
try to avoid
2.
resharpen or change
3.
change bit
4.
Fasten Nut pulley
(19) tighter
1.
Place a scrap wood as
back-up material
under your workpiece
1. Reduce feed rate
2.
sharpen/replace
3.
Increase belt tension
4.
Choose correct bit
1.
Replace
2.
Replace
3.
Check
4.
Check/replace
5.
Check/clean
1.
Adjust spring tension
1. Check and clean if
necessary
RUNNING DIRECTION (ONLY LR)