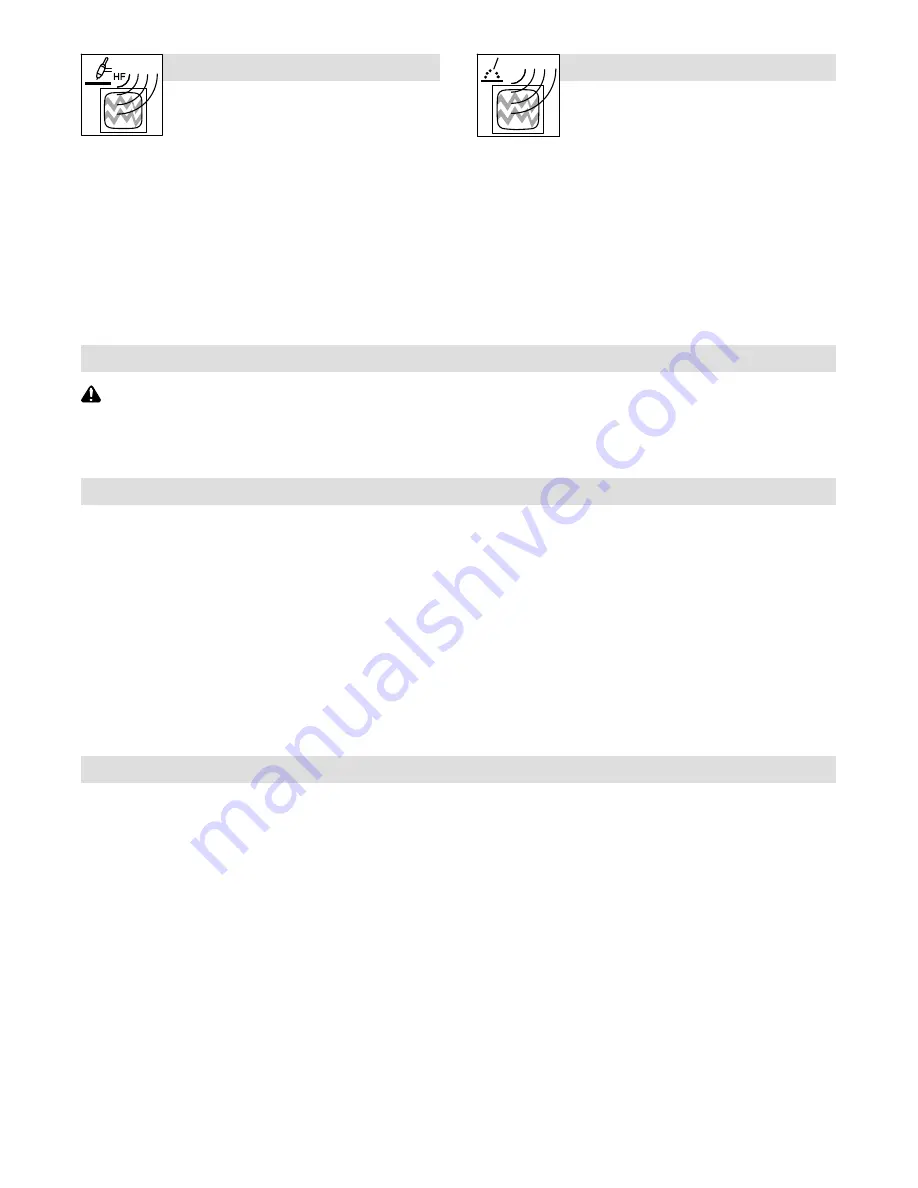
OM-284833 Page 4
H.F. RADIATION can cause interference.
D
High-frequency (H.F.) can interfere with radio
navigation, safety services, computers, and
communications equipment.
D
Have only qualified persons familiar with electronic equipment
perform this installation.
D
The user is responsible for having a qualified electrician prompt-
ly correct any interference problem resulting from the installa-
tion.
D
If notified by the FCC about interference, stop using the
equipment at once.
D
Have the installation regularly checked and maintained.
D
Keep high-frequency source doors and panels tightly shut, keep
spark gaps at correct setting, and use grounding and shielding to
minimize the possibility of interference.
ARC WELDING can cause interference.
D
Electromagnetic energy can interfere with
sensitive electronic equipment such as
computers and computer-driven equipment
such as robots.
D
Be sure all equipment in the welding area is electromagnetically
compatible.
D
To reduce possible interference, keep weld cables as short as
possible, close together, and down low, such as on the floor.
D
Locate welding operation 100 meters from any sensitive elec-
tronic equipment.
D
Be sure this welding machine is installed and grounded
according to this manual.
D
If interference still occurs, the user must take extra measures
such as moving the welding machine, using shielded cables,
using line filters, or shielding the work area.
1-4. California Proposition 65 Warnings
WARNING: This product can expose you to chemicals in-
cluding lead, which are known to the state of California to
cause cancer and birth defects or other reproductive
harm.
For more information, go to www.P65Warnings.ca.gov.
1-5. Principal Safety Standards
Safety in Welding, Cutting, and Allied Processes,
American Welding
Society standard ANSI Standard Z49.1. Website: www.aws.org.
Safe Practice For Occupational And Educational Eye And Face Protec-
tion,
ANSI Standard Z87.1 from American National Standards Institute.
Website: www.ansi.org.
Safe Practices for the Preparation of Containers and Piping for Welding
and Cutting,
American Welding Society Standard AWS F4.1 from Glob-
al Engineering Documents. Website: www.global.ihs.com.
Safe Practices for Welding and Cutting Containers that have Held Com-
bustibles,
American Welding Society Standard AWS A6.0 from Global
Engineering Documents. Website: www.global.ihs.com.
National Electrical Code,
NFPA Standard 70 from National Fire Protection
Association. Website: www.nfpa.org and www. sparky.org.
Safe Handling of Compressed Gases in Cylinders,
CGA Pamphlet P-1
from Compressed Gas Association. Website:www.cganet.com.
Safety in Welding, Cutting, and Allied Processes,
CSA Standard
W117.2 from Canadian Standards Association.
Website: www.csagroup.org.
Standard for Fire Prevention During Welding, Cutting, and Other Hot
Work,
NFPA Standard 51B from National Fire Protection Association.
Website: www.nfpa.org.
OSHA
Occupational Safety and Health Standards for General Industry
,
Title 29, Code of Federal Regulations (CFR), Part 1910.177 Subpart N, Part
1910 Subpart Q, and Part 1926, Subpart J. Website: www.osha.gov.
OSHA
Important Note Regarding the ACGIH TLV, Policy Statement on
the Uses of TLVs and BEIs.
Website: www.osha.gov.
Applications Manual for the Revised NIOSH Lifting Equation
from
the
National Institute for Occupational Safety and Health (NIOSH).
Website: www.cdc.gov/NIOSH.
1-6. EMF Information
Electric current flowing through any conductor causes localized electric
and magnetic fields (EMF). The current from arc welding (and allied pro-
cesses including spot welding, gouging, plasma arc cutting, and
induction heating operations) creates an EMF field around the welding
circuit. EMF fields can interfere with some medical implants, e.g. pace-
makers. Protective measures for persons wearing medical implants
have to be taken. For example, restrict access for passers
−
by or con-
duct individual risk assessment for welders. All welders should use the
following procedures in order to minimize exposure to EMF fields from
the welding circuit:
1. Keep cables close together by twisting or taping them, or using a
cable cover.
2. Do not place your body between welding cables. Arrange cables
to one side and away from the operator.
3. Do not coil or drape cables around your body.
4. Keep head and trunk as far away from the equipment in the
welding circuit as possible.
5. Connect work clamp to workpiece as close to the weld as
possible.
6. Do not work next to, sit or lean on the welding power source.
7. Do not weld whilst carrying the welding power source or wire
feeder.
About Implanted Medical Devices:
Implanted Medical Device wearers should consult their doctor and the
device manufacturer before performing or going near arc welding, spot
welding, gouging, plasma arc cutting, or induction heating operations.
If cleared by your doctor, then following the above procedures is recom-
mended.