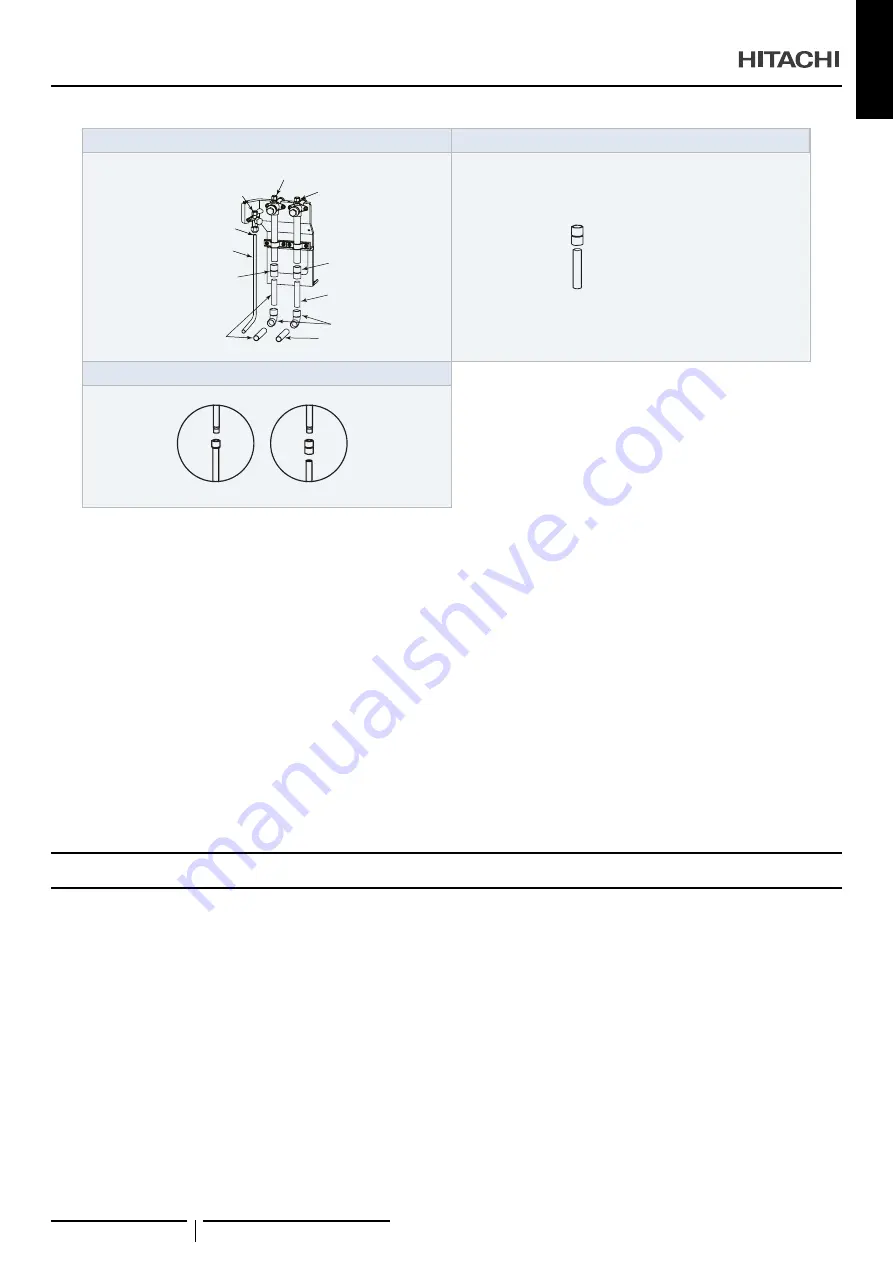
ras-18fsXnPe
(*) if longer piping is needed add the following
Stop valve
(High/low pressure gas)
Stop valve
(Low pressure gas)
Stop valve (Liquid)
Flaring
(in the field)
Adapter (field-supplied)
90º Elbow (field-supplied)
Gas "high/low pressure" pipe
(Ø22.2) (field-supplied)
Liquid pipe (Ø15.88)
(field-supplied)
Adapter (field-supplied)
Gas "low pressure" pipe
(Ø28.58) (field-supplied)
Gas "low pressure" pipe
(28.58) (field-supplied)
Adapter (field-supplied).
Gas pipe
(field-supplied)
(**) example of options for brazing the pipes at this point
Adapter
(field-supplied).
Liquid pipe
(field-supplied)
Accessory
pipe
Expand
(in the field)
.
Special care should be taken to ensure that the flame from the
blow torch does not fall on the body of the stop valve, on the
compressor and cover or on the insulation bushings; insert a
metal plate in front of the oil return pipe: see on section
Connect the indoor units to the outdoor units using copper pipes
specifically for use with refrigerant. When laying the pipes make
sure that they do not directly rest on or touch walls or other parts
of the building (when the refrigerant is flowing through the pipes,
this could cause strange noises).
Specific torques for the flared connections: see on section
.
While brazing, apply a flow of nitrogen gas inside the pipe.
Fully insulate the refrigerant pipes.
For heat pump systems (2 pipes)
•
Refer to the Accessories factory-supplied for the details of
the accessory pipes.
•
Ensure that the closing pipes of the high/low and low
pressure gas stop valves (2 parts) are removed firstly.
For heat recovery systems (3 pipes)
•
Refer to the Accessories factory-supplied for the details of
the accessory pipes.
•
Ensure that the closing pipes of the high/low and low
pressure gas stop valves (1 parts) are removed firstly.
!
D a n G e r
• Check that the gas and liquid stop valves are fully closed.
• Check that there is no gas inside the pipe before removing the
stop pipe. Otherwise, the pipe may explode when heated with
the blow torch
8.4 refriGerant CHarGe
8.4.1 Air-Tight Test
Check to ensure that spindles of the stop valves for High/Low
pressure gas, Low pressure gas and Liquid pipes are closed
completely before air-tight test.
The refrigerant used for this outdoor unit is R410A only. Use
the manifold gauge and the charging hose for exclusive use of
R410A.
Tightening check of stop valves
After connecting the pipe, remove the caps of stop valves for
high/low pressure gas, low pressure gas (for heat recovery
system only) and liquid. Tighten the open-close spindle in the
closing direction according to the following tightening torque.
Caution for operation of stop valves
a.
Remove the stop valve caps before performing the air-
tight test after connecting the refrigerant piping. Tighten
the spindle (valve) in clockwise direction according to the
following tightening torque.
b.
Perform the work after warming the spindle part with
a dryer etc. when controlling the stop valve in a cold
area. (O-ring of the spindle part will harden at the low
temperature and the refrigerant leakage may occur.)
c.
Do not apply an excessive force after fully opening the
spindle. (Tightening Torque: < 5.0N.m) (The back seat is
not provided.)
d.
When each valve is opened, remove tags “Close”
(Accessories) and attach tags “Open” instead.
e.
Tighten securely the caps according to the following
tightening torque after each spindle valve is opened.
ENGLISH
PIPING WORK AND REFRIGERANT CHARGE
PMML0479 rev.4 - 11/2018
29
Summary of Contents for RAS-10FSXNPE
Page 2: ......
Page 14: ... i RAS 8 12 FSXNSE 1725 959 784 B A ...
Page 15: ... RAS 14FSXNSE 1725 1219 784 B A ...
Page 16: ... RAS 16 18 FSXNSE 1725 1219 784 B A ...
Page 17: ... RAS 20 24 FSXNSE 1725 1609 784 B A ...
Page 18: ... RAS 5 6 FSXNPE 1725 959 784 A B ...
Page 19: ... RAS 8 14 FSXNPE 1725 1219 784 A B ...
Page 20: ... RAS 16 18 FSXNPE 1725 1609 784 A B ...
Page 119: ......
Page 169: ......