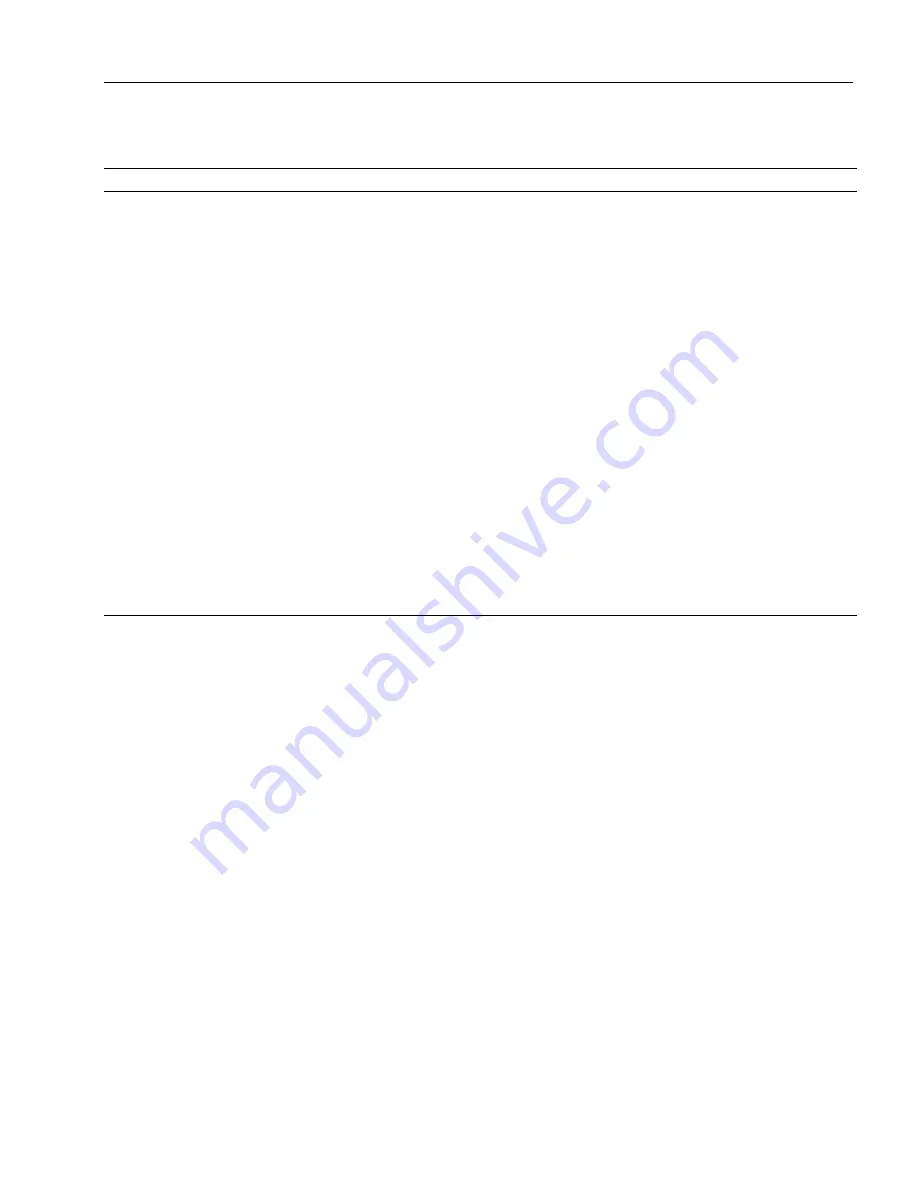
Drawings
Rev A 05/01/01 // SB
190113_A
35
DRAWING 5B. CONSOLE DS350/1318 - PARTS LIST - continued
GRAPHIC CONSOLE (HORIZONTAL), PARTS LIST
PART NO
.
PAT 050-350-061-318
NO.
PART NO.
QTY
DESCRIPTION
01
031-300-110-049
1
CONSOLE ACCY, FRONT FACE & DIS.
02
050-150-300-052
1
BOARD, PUSHBUTTON SET(KEYBRDS)
03
003-051-905-235
1
SWITCH, KEY
04
050-350-110-139
1
KEY, SPARE
05
002-053-703-101
6
SCREWS, FRONT PANEL MOUNTING
06
050-150-300-050
1
BOARD
07
050-150-300-051
1
TERMINAL BOARD
08
050-000-050-625
1
SEALING, FRONT PANEL
09
050-000-100-180
1
HOUSING
10
050-350-110-263
1
MOUNTING KIT FOR HOUSING
11
021-448-161-213
1
STRAIN RELIEF, PG13.5 GREY/WHT
12
031-300-100-173
1
GASKET
13
031-300-100-392
1
CANNON CONN., 7-SOCKET RECPT.
14
031-300-100-024
1
DUST CAP
15
000-208-010-210
1
TOOTHWASHER, M12
16
000-214-210-013
1
LOCKNUT, PG13.5
17
050-350-300-076
1
BOARD, TERMINAL INTERFACE FOR
LIGHTBAR
38 Years Specializing
in Crane Electronic Repair & Parts Sales
Call Us. We are glad to help
Bode Technical Services Inc
Email: [email protected]
Phone No.: +1.303.433.8878