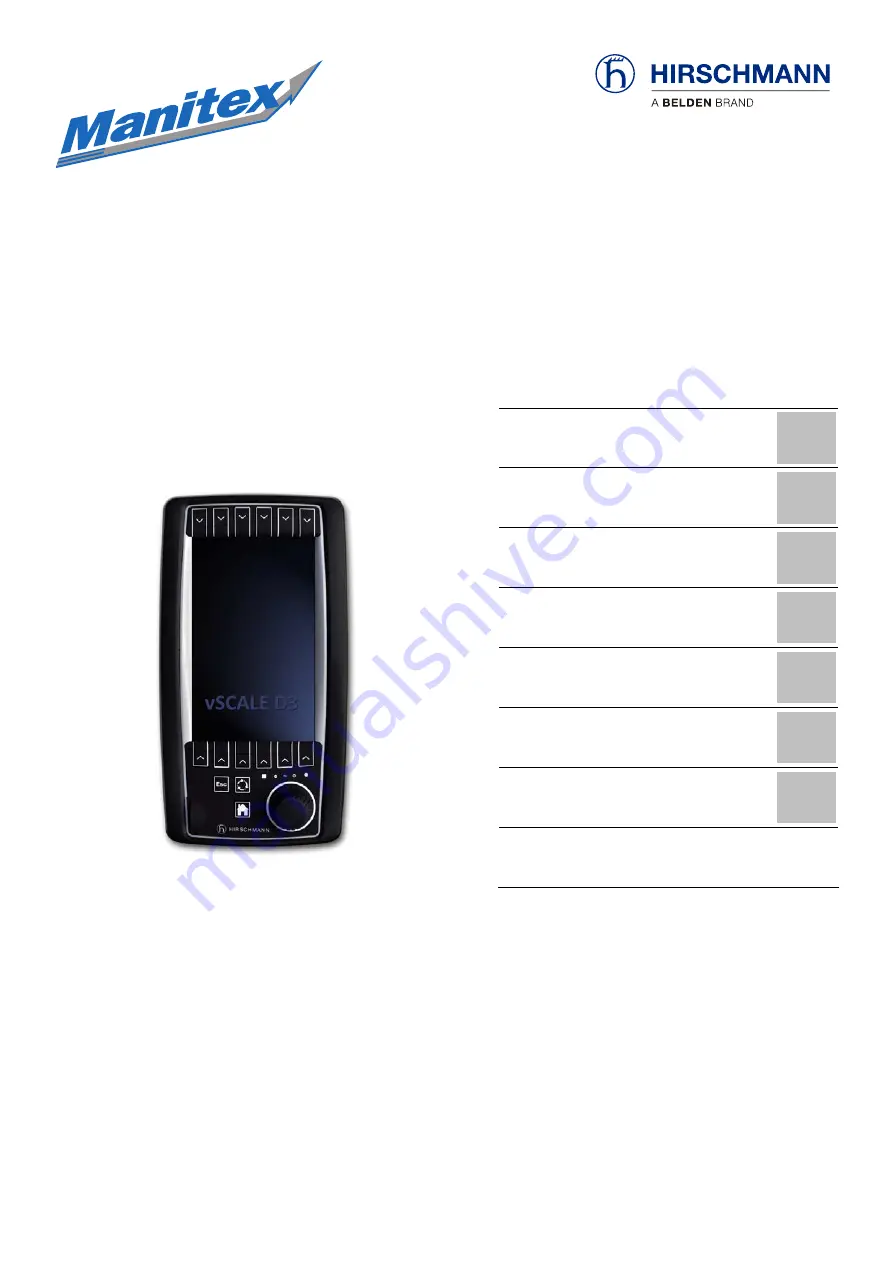
vSCALE
D3
Operating console
SLI system
Manitex Telescopic Crane
Contents
Safety instructions
Product description
Installation / Wiring
Commissioning
Operation
Maintenance / Repair
Appendix
User manual
Issue B - 03/2012
This document has the order no.
50-700-19-2001_422175_en
Pub Mtx p/n: 7600004-023
Date:
April 2012
For System:
4800850-001