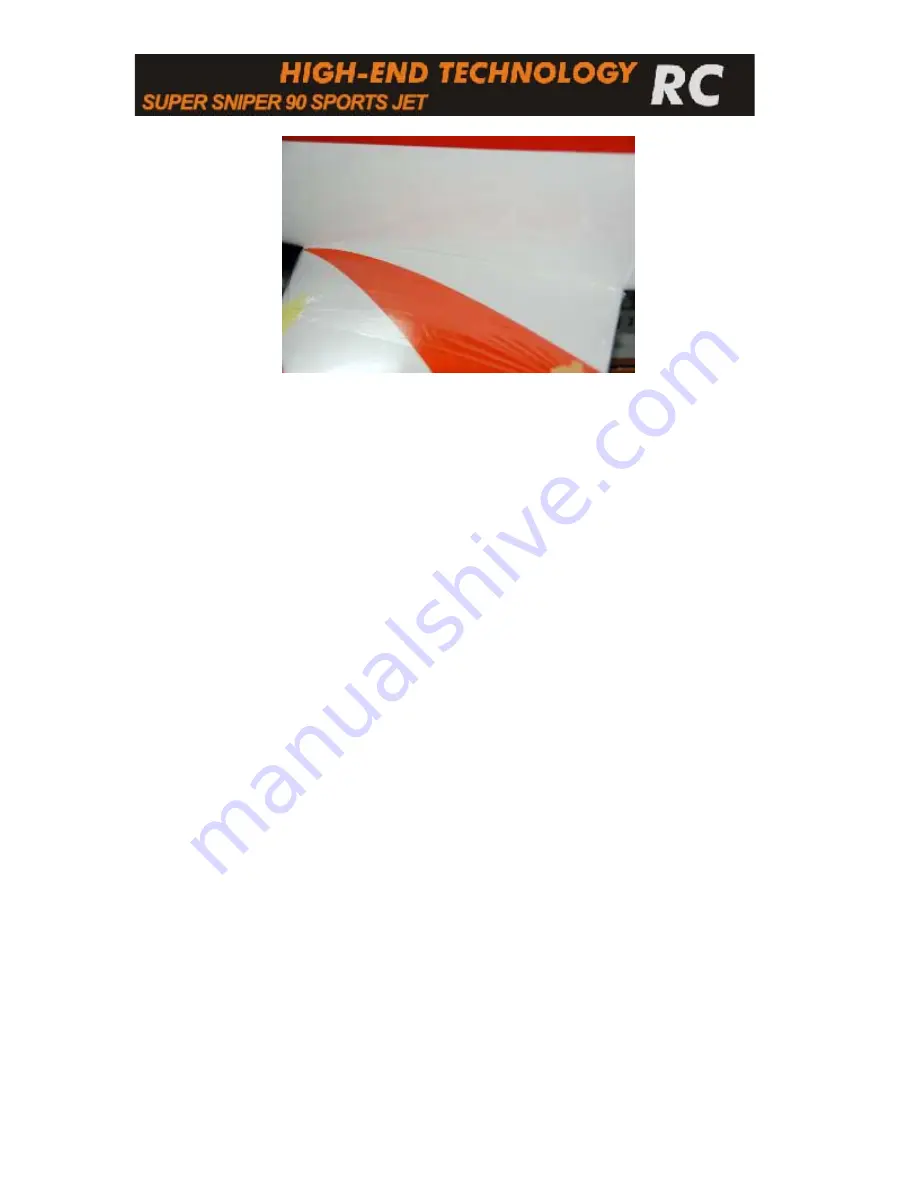
Page 11/34
Apply some oil to the mounting screw and blind nut thread and mount the wing in place.
The oil will prevent the screw from getting locked in case a little bit of epoxy will come
to close. Turn the plane around.
Epoxy/Micro Balloon paste should have been pushed out between the wing and the
fuselage. Use a cloth and lots of cleaning alcohol to clear all excess epoxy before it cures.
Make sure you get a smooth transition between fuselage and wing.
In case you still have a gap or cleaned away to much epoxy push some of the paste into
the gap (with a scrap piece of balsa or a medical syringe).
Once cured remove the wing. The wing should now sit perfectly on the fuselage.