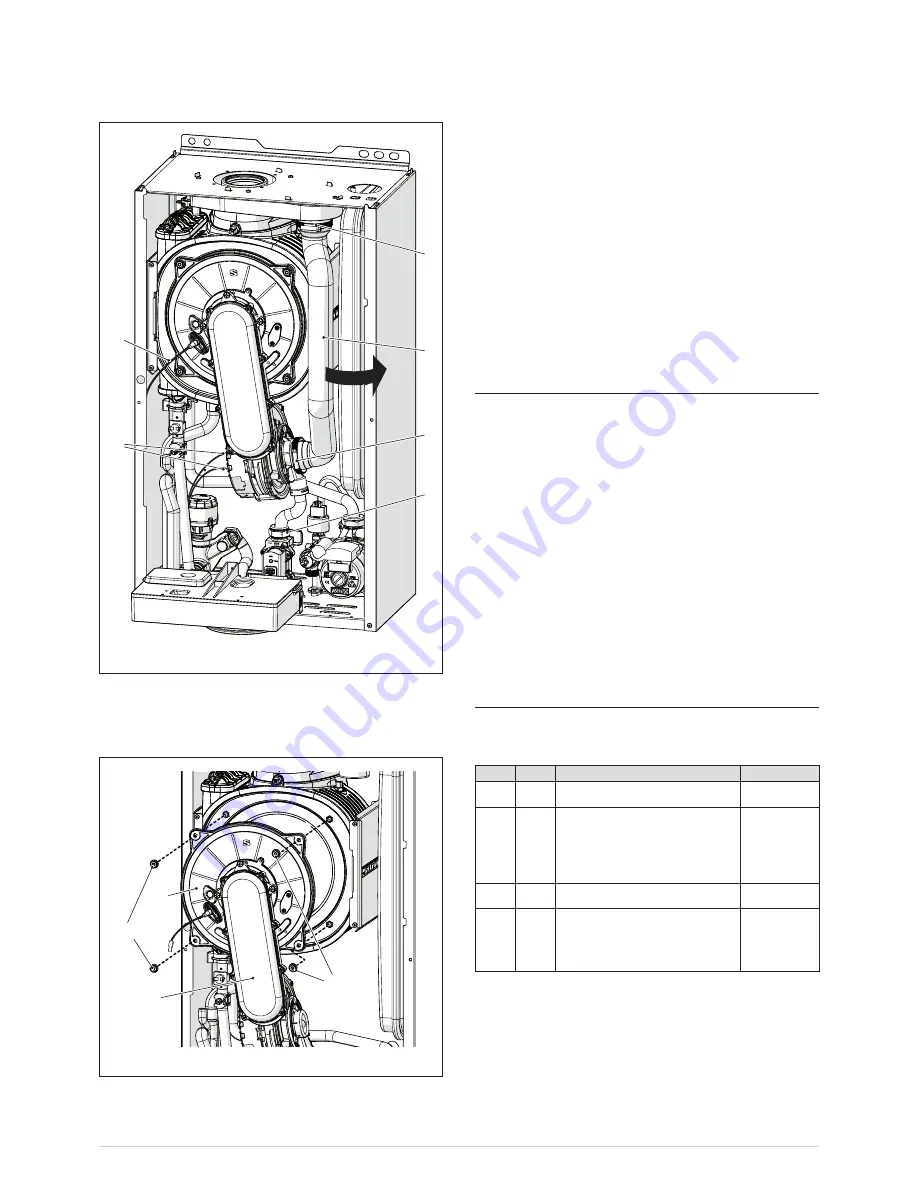
28
– loosen the clips (6) and extract the air inlet pipe (7)
– unscrew the swivel joint (8)
– extract the connectors (9) from the fan and disconnect the
electrode cable (10)
6
8
6
7
9
10
Fig. 40
– unscrew the four nuts (11) securing the combustion cham-
ber door (12)
– pull the fan-sleeve-door assembly (13) forwards and re-
move it.
11
11
13
12
Fig. 41
m
CaUTiON
work carefully when removing the assembly (13) to pre-
vent any damage occurring to the internal insulation of
the combustion chamber and the door seal.
4.3.2 Cleaning the burner and the combustion
chamber
the combustion chamber and the burner do not require any
particular maintenance. simply brush them with a soft brush.
4.3.3 Final operations
after having cleaned the combustion chamber and the burner:
– remove any carbon residue
– check the state of the ignition/detection electrode and re-
place if necessary
– check that the seal and the insulation of the door (12) to the
combustion chamber are integral. Replace if necessary
– refit the assembly by carrying out the same operations for
removal but in the reverse order and tighten the screws (11)
of the door to the combustion chamber
– reconnect the connections to the fan and the electrode.
4.4
Checks
4.4.1 Checking the smoke duct
It is recommended that the user checks that the combustion
air inlet duct and smoke outlet duct are integral and airtight.
4.4.2 Checking the expansion vessel pressure
It is recommended that the expansion vessel on the water side
is drained and that the prefilling pressure is not less than 1
bar
. If this is not the case, pressurize it to the correct value
(see sectionExpansion vessel".
once the checks described above have been completed:
– refill the boiler as described in section "REFiLL operations"
– check that the siphon has been filled correctly
– activate the "Chimney sweep function" and carry out a
smoke analysis and/or measure the combustion efficiency
– refit the front panel securing it with the two screws which
were removed previously.
4.5
Unscheduled maintenance
If replacing the electronic board, the user must set the param-
eters as indicated in the table.
Type
No.
Description
Setting
PaR
01
Index showing boiler power in kW
0=24; 1=25; 2=30; 3=35; 4=40
1
PaR
02
Hydraulic configuration
0 = rapid
1 = storage tank with thermostat or
heating only
2 = hot water tank with sensor
3 = two programmer
1 or 2
PaR
03
Gas type Configuration
0 = G20; 1 = lPG
0 or 1
PaR
04
Combustion configuration
0 = sealed chamber with combus-
tion control
1 = open chamber with smoke
thermostat
0