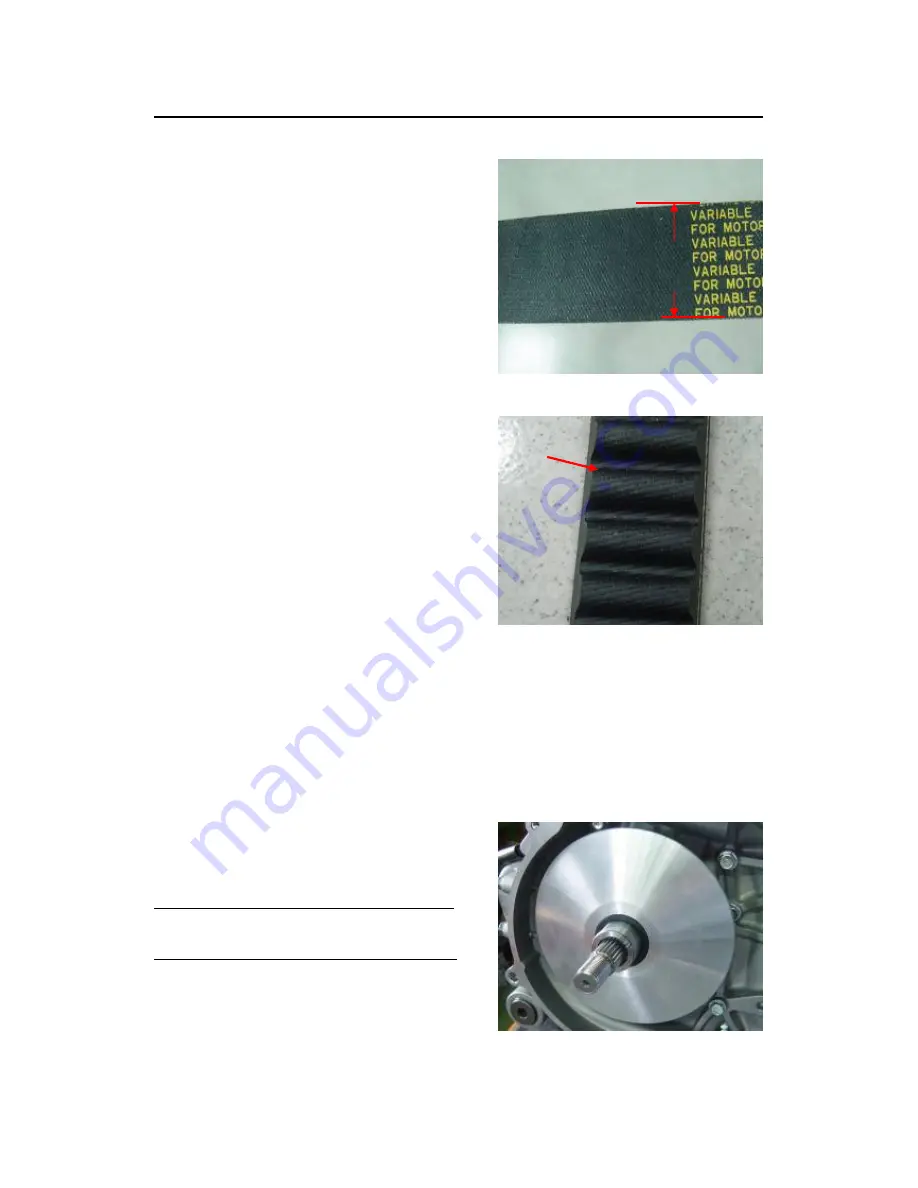
Chapter 1 Engine, Transmission & Gear
I-41
INSPECTION
Check the drive belt for cracks, separation or
abnormal or excessive wear.
Measure the drive belt width.
Service Limit: 23.0 mm (0.9055 in)
INSTALLATION
Lay the drive belt on the driven pulley.
Squeeze the driven pulley to widen its faces then
set the drive belt on the drive pulley face collar.
Reinstall the drive pulley face and recoil dish,
hold the drive pulley and tighten the nut.
Torque: 80 – 100 N.m (58 – 72 ft.lb)
Reinstall the left crankcase cover.
Drive Pulley
REMOVAL
Remove the left crankcase cover.
Remove the drive belt.
Remove the moveable drive face assembly.
NOTE
。
If the spline fitting is tight, use a commercially
available bearing puller.
DISASSEMBLY
Remove the ramp plate.
Remove the weight rollers.
Min. 23 mm
Summary of Contents for 2002 ATV-320 S
Page 14: ...Chapter 1 Engine Transmission Gear I 5 Cylinder Head Cover 1 5 2 3 7 6 4 8 11 10 9 5 5 5 9...
Page 15: ...Chapter 1 Engine Transmission Gear I 6 Cylinder Head 2 3 4 4 5 6 7 8 9 11 10 12 12 13 14 18...
Page 16: ...Chapter 1 Engine Transmission Gear I 7 Camshaft Valve Cam...
Page 29: ...Chapter 1 Engine Transmission Gear I 20 Cylinder Piston Crankshaft...
Page 36: ...Chapter 1 Engine Transmission Gear I 27 Crankcase...
Page 40: ...Chapter 1 Engine Transmission Gear I 31 Right Crankcase Cover...
Page 42: ...Chapter 1 Engine Transmission Gear I 33 Cooling system...
Page 47: ...Chapter 1 Engine Transmission Gear I 38 Left Crankcase Cover...
Page 54: ...Chapter 1 Engine Transmission Gear I 45 Transmission...
Page 61: ...Chapter 2 Fuel System Carburetion II 3 3 CARBURETOR...
Page 65: ...Chapter 2 Fuel System Carburetion II 7 7 FUEL TANK...
Page 68: ...Chapter 2 Fuel System Carburetion II 10 10 AIR CLEANER ASSEMBLY...
Page 70: ...Chapter 2 Fuel System Carburetion II 12 12 EXHAUST SYSTEM...
Page 78: ...Chapter 3 Ignition and Starting System III 7 Recoil Backup Starting System...
Page 81: ...Chapter 4 Frame Cover IV 2 FRAME BODY 320S...
Page 82: ...Chapter 4 Frame Cover IV 3 FRAME BODY 320U...
Page 83: ...Chapter 4 Frame Cover IV 4 BODY COVER SEAT 320S...
Page 84: ...Chapter 4 Frame Cover IV 5 BODY COVER SEAT 320U...
Page 91: ...Chapter 5 Wheels Tires Brakes V 2 HANDLE BAR...
Page 92: ...Chapter 5 Wheels Tires Brakes V 3 STEERING MPH...
Page 95: ...Chapter 5 Wheels Tires Brakes V 6 FRONT REAR WHEEL...
Page 98: ...Chapter 5 Wheels Tires Brakes V 9 FRONT SUSPENSION...
Page 99: ...Chapter 5 Wheels Tires Brakes V 10 REAR SUSPENSION SWING ARM SUB ASS Y...
Page 103: ...Chapter 5 Wheels Tires Brakes V 14 HYDRAULIC BRAKE SYSTEM...
Page 104: ...Chapter 5 Wheels Tires Brakes V 15 BRAKE CALIPER...
Page 114: ...Chapter 6 Alternator Electrical Equipment VI 2 Alternator Starter Gear...
Page 125: ...Chapter 6 Alternator Electrical Equipment VI 13 Wire Diagram...