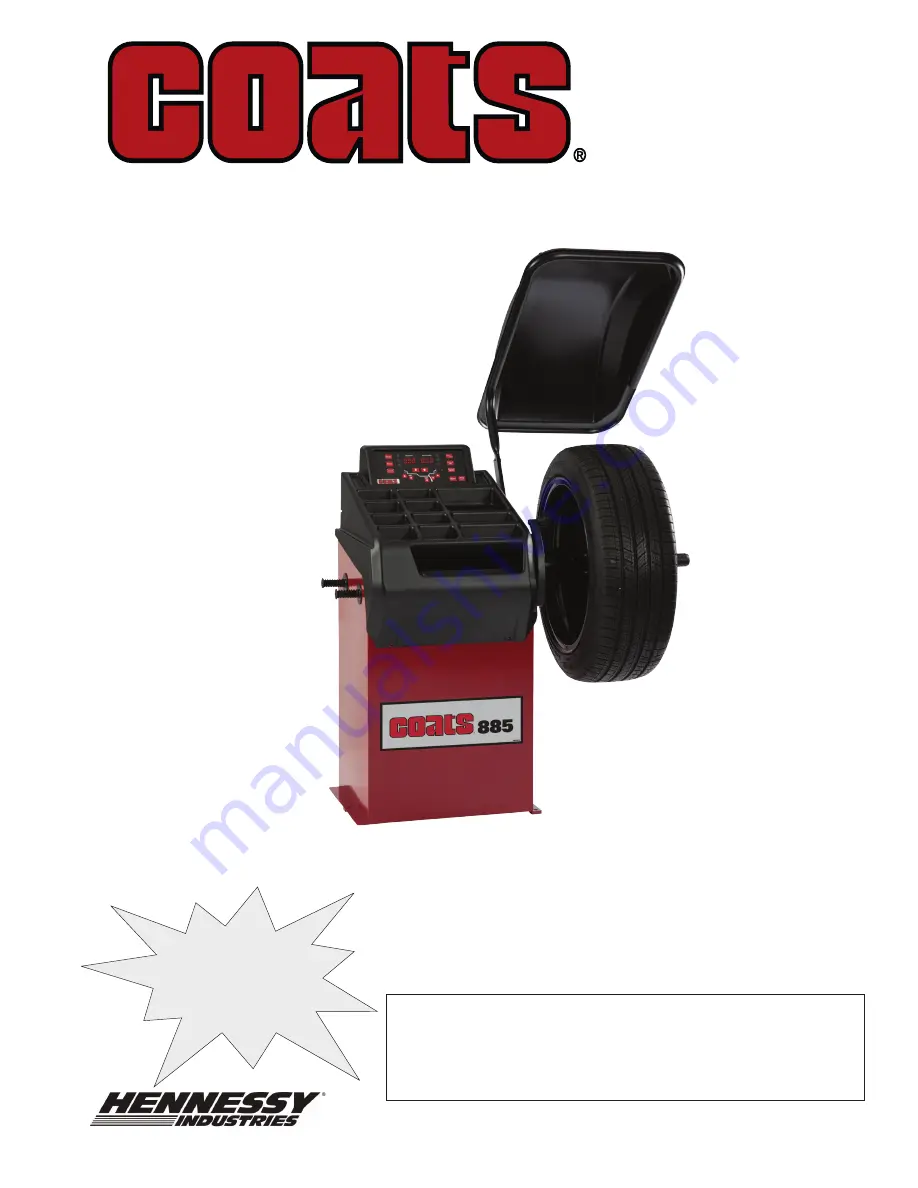
Manual Part No.: 85611582 00
Revision:
05/19
See
Balancing Your
First Tire
on page 1.
885 Wheel Balancer
Safety Instructions
Set Up Instructions
Operation Instructions
Maintenance Instructions
READ these instructions before placing unit in
service. KEEP these and other materials delivered
with the unit in a binder near the machine for ease
of reference by supervisors and operators.
1601 J. P. Hennessy Drive, La Vergne, TN USA 37086 615/641-7533 800/688-6359 www.coatsgarage.com
HENNESSY INDUSTRIES LLC Manufacturer of COATS®, AMMCO® and BADA® Automotive Service Equipment and Tools.