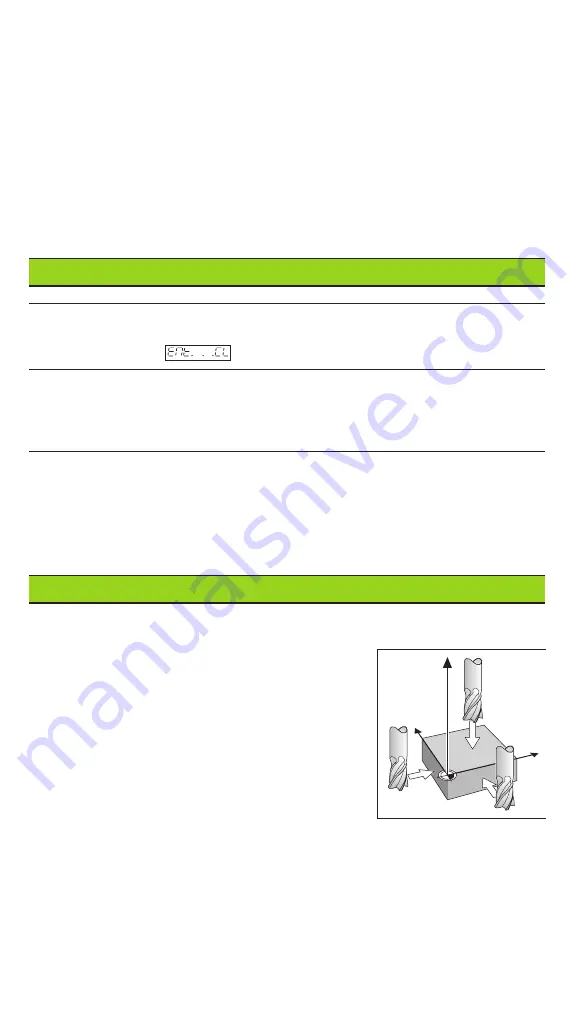
Touching the workpiece
The ND 510 and ND 550 digital readouts accept HEIDENHAIN linear encoders with
sinusoidal output signals.
These linear encoders have one or more reference marks, preferably of the distance-
coded
type. When a reference mark is crossed over, a signal is generated which
identifies that position as a reference point.
After switch-on, simply crossing over the reference mark restores the relationship
between axis positions and display values last defined by datum setting.
With distance-coded reference marks, a maximum traverse of only 20 mm is suffi-
cient to re-establish the relationship between axis positions and display values after
switch-on.
Switch-On
Turn on the power
➤
The power switch is located on the rear panel.
The display shows and
REF blinks
.
Turn on reference mark evaluation
➤
Press the ENT key.
The display shows the value last assigned to the reference mark position, the
REF
indicator glows
and the
decimal point blinks
.
Cross over the reference mark in each axis
➤
Move the axes one after the other until the display becomes active and the
decimal point glows
.
The display unit is now ready for operation.
If you do
not
wish reference mark evaluation, press
CL
instead of ENT.
Setting the Datum
The datum setting procedure assigns a display value to a specific axis position.
Two separate datum points can be defined.
You can switch from one datum to the other
at the touch of a key.
Use datum 2 if you want to display
incremental values.
➤
Select the
datum
.
➤
Select the
coordinate axis
in which the tool moves,
for example the X-axis.
➤
Touch
the workpiece with the tool.
➤
Enter the
position
of the tool center
with the numeric keypad, for example X = –5 [mm]. The
minus sign
can only be
entered when at least one digit is shown in the display.
➤
Press
ENT
.
The display unit stores the value for this tool position.
Follow the above procedure for other axes.
Y
X
Z