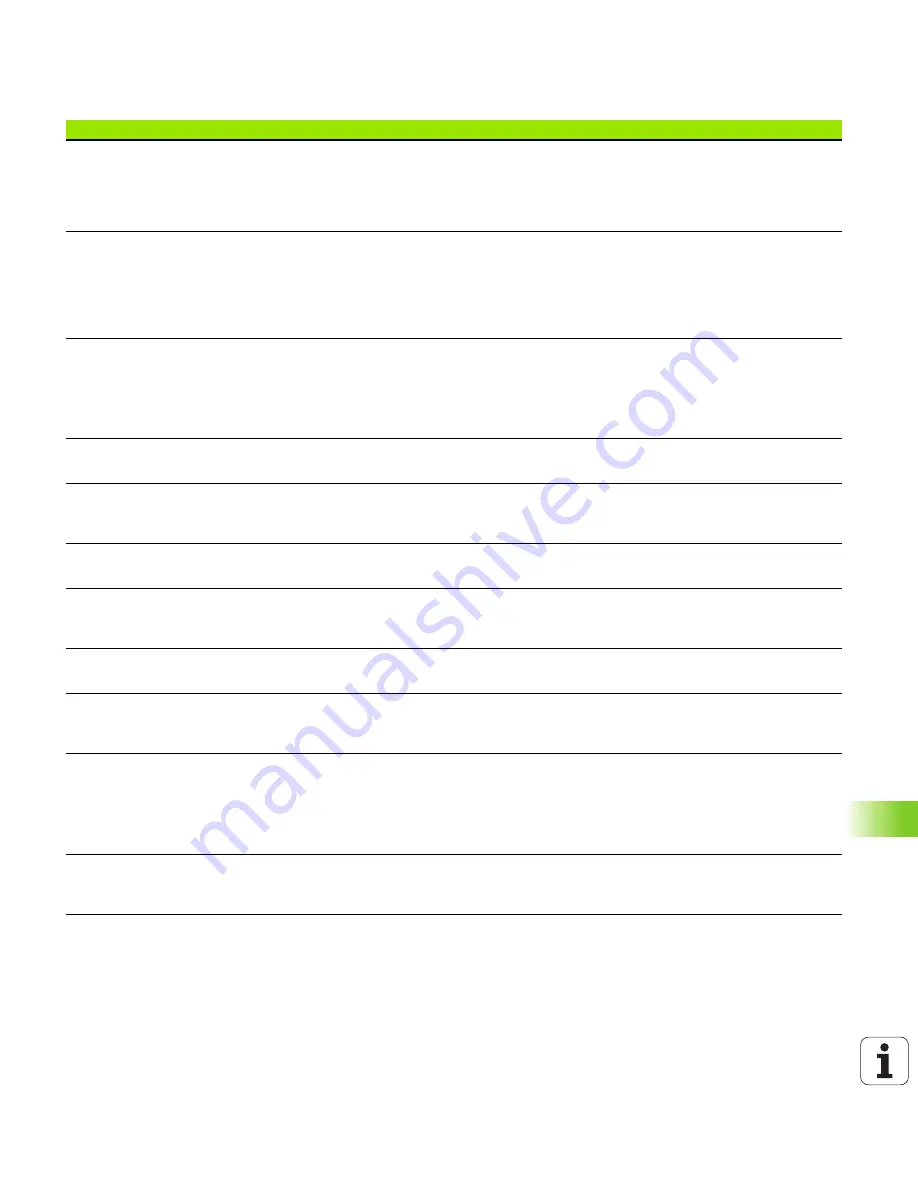
HEIDENHAIN iTNC 530
579
1
8
.1 Gener
a
l User P
a
ra
met
e
rs
Radius measurement with the TT 130 touch
probe: Probing direction
MP6505.0 (traverse range 1) to 6505.2 (traverse range 3)
Positive probing direction in the angle reference axis (0° axis):
0
Positive probing direction in the +90° axis:
1
Negative probing direction in the angle reference axis (0° axis):
2
Negative probing direction in the +90° axis:
3
Probing feed rate for second measurement
with TT 130, stylus shape, corrections in
TOOL.T
MP6507
Calculate feed rate for second measurement with TT 130,
with constant tolerance:
Bit 0 = 0
Calculate feed rate for second measurement with TT 130,
with variable tolerance:
Bit 0 = 1
Constant feed rate for second measurement with TT 130:
Bit 1 = 1
Maximum permissible measuring error
with TT 130 during measurement with
rotating tool
Required for calculating the probing feed rate in
connection with MP6570
MP6510.0
0.001
to
0.999
[mm] (recommended input value: 0.005 mm)
MP6510.1
0.001
to
0.999
[mm] (recommended input value: 0.01 mm)
Feed rate for probing a stationary tool with
the TT 130
MP6520
1
to
3 000
[mm/min]
Radius measurement with the TT 130:
Distance from lower edge of tool to upper
edge of stylus
MP6530.0 (traverse range 1) to MP6530.2 (traverse range 3)
0.001
to
99.9999
[mm]
Set-up clearance in the tool axis above the
stylus of the TT 130 for pre-positioning
MP6540.0
0.001
to
30 000.000
[mm]
Clearance zone in the machining plane
around the stylus of the TT 130 for pre-
positioning
MP6540.1
0.001
to
30 000.000
[mm]
Rapid traverse for TT 130 in the probe cycle
MP6550
10
to
10 000
[mm/min]
M function for spindle orientation during
individual tooth measurement
MP6560
0
to
999
–1
: Function inactive
Measuring rotating tools: Permissible
rotational speed at the circumference of the
milling tool
Required for calculating rpm and probe feed
rate
MP6570
1.000
to
120.000
[m/min]
Measuring rotating tools: Permissible
rotational rpm
MP6572
0.000
to
1000.000
[rpm]
If you enter 0, the speed is limited to 1000 rpm
3-D touch probes
Summary of Contents for ITNC 530 - 6-2010 DIN-ISO PROGRAMMING
Page 1: ...User s Manual DIN ISO Programming iTNC 530 NC Software 606 420 01 606 421 01 English en 6 2010...
Page 4: ......
Page 16: ...Changed functions 606 42x 01 since the predecessor versions 340 49x 06 16...
Page 18: ......
Page 41: ...First Steps with the iTNC 530...
Page 61: ...Introduction...
Page 83: ...Programming Fundamentals File Management...
Page 130: ...130 Programming Fundamentals File Management 3 4 Working with the File Manager...
Page 131: ...Programming Programming Aids...
Page 153: ...Programming Tools...
Page 187: ...Programming Programming Contours...
Page 217: ...Programming Data Transfer from DXF Files...
Page 235: ...HEIDENHAIN iTNC 530 235 Programming Subprograms and Program Section Repeats...
Page 252: ...252 Programming Subprograms and Program Section Repeats 8 6 Programming Examples...
Page 253: ...Programming Q Parameters...
Page 301: ...Programming Miscellaneous Functions...
Page 325: ...Programming Special Functions...
Page 380: ...380 Programming Special Functions 11 8 Working with Cutting Data Tables...
Page 381: ...Programming Multiple Axis Machining...
Page 417: ...Programming Pallet Editor...
Page 437: ...Manual Operation and Setup...
Page 499: ...Positioning with Manual Data Input...
Page 505: ...Test Run and Program Run...
Page 536: ...536 Test Run and Program Run 16 7 Optional Program Run Interruption...
Page 537: ...MOD Functions...
Page 574: ...574 MOD Functions 17 21 Configuring the HR 550 FS Wireless Handwheel...
Page 575: ...Tables and Overviews...
Page 604: ...604 Tables and Overviews 18 4 Exchanging the Buffer Battery...