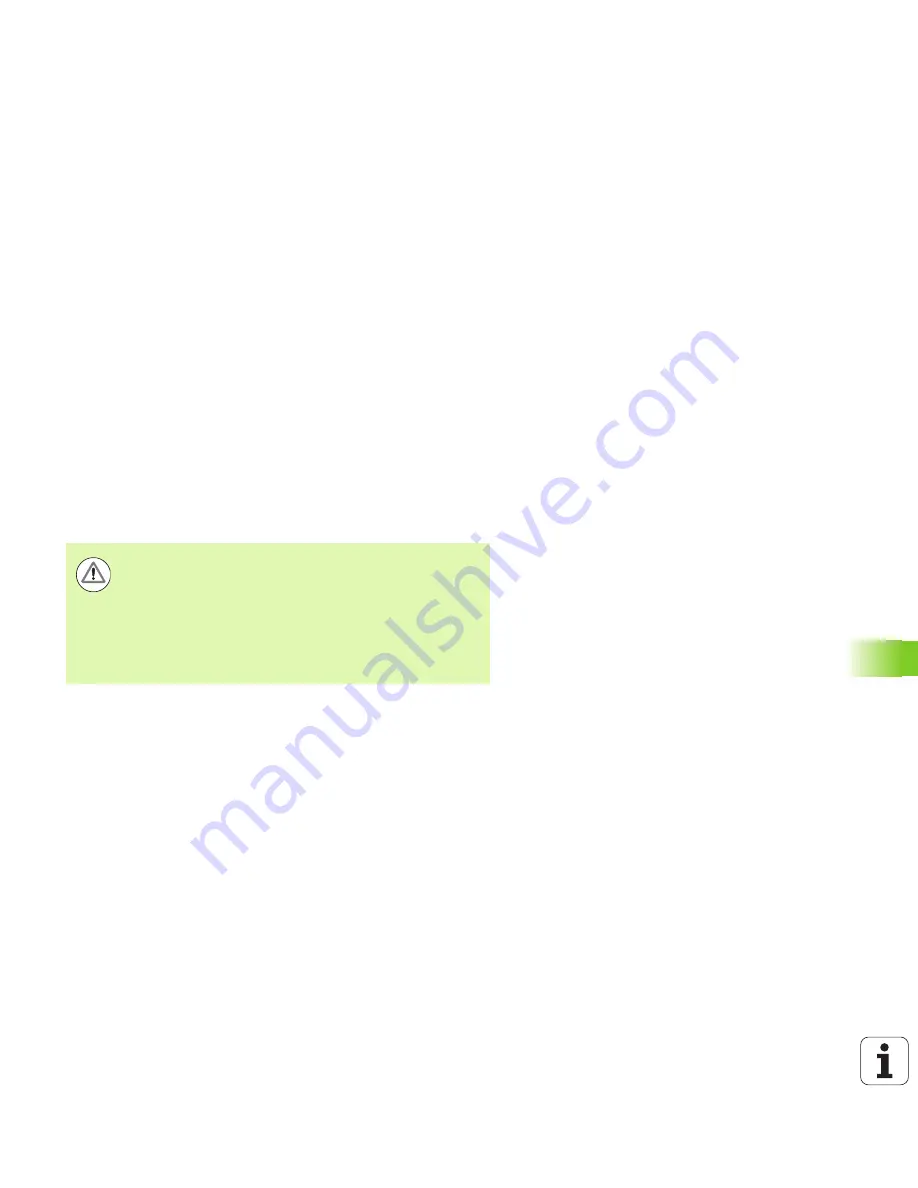
HEIDENHAIN iTNC 530
495
14.1
0
Tilting the W
o
rk
ing Plane (Sof
tw
ar
e Option
1)
Traversing the reference points in tilted axes
With tilted axes, you use the machine axis direction buttons to cross
over the reference points. The TNC interpolates the corresponding
axes. Be sure that the function for tilting the working plane is active in
the Manual Operation mode and that the actual angle of the tilted axis
was entered in the menu field.
Setting the datum in a tilted coordinate system
After you have positioned the rotary axes, set the datum in the same
manner as for a non-tilted system. The behavior of the TNC during
datum setting depends on the settings of Machine Parameter 7500 in
your kinematics table:
MP 7500, bit 5=0
With an active tilted working plane, the TNC checks during datum
setting in the X, Y and Z axes whether the current coordinates of the
rotary axes agree with the tilt angles that you defined (3D-ROT
menu). If the tilted working plane function is not active, the TNC
checks whether the rotary axes are at 0° (actual positions). If the
positions do not agree, the TNC will display an error message.
MP 7500, bit 5=1
The TNC does not check whether the current coordinates of the
rotary axes (actual positions) agree with the tilt angles that you
defined.
Datum setting on machines with rotary tables
If you use a rotary table to align the workpiece, for example with
probing cycle 403, you must set the table position value to zero after
alignment and before setting the datum in the linear axes X, Y and Z.
Otherwise, the TNC generates an error message. Cycle 403 provides
you with an input parameter for this purpose (see User’s Manual for
Touch Probe Cycles, “Basic Rotation Compensation via Rotary Axis”).
Danger of collision!
Always set a reference point in all three reference axes.
If your machine tool is not equipped with axis control, you
must enter the actual position of the rotary axis in the
menu for manual tilting: The actual positions of one or
several rotary axes must match the entry. Otherwise the
TNC will calculate an incorrect datum.
Summary of Contents for ITNC 530 - 6-2010 DIN-ISO PROGRAMMING
Page 1: ...User s Manual DIN ISO Programming iTNC 530 NC Software 606 420 01 606 421 01 English en 6 2010...
Page 4: ......
Page 16: ...Changed functions 606 42x 01 since the predecessor versions 340 49x 06 16...
Page 18: ......
Page 41: ...First Steps with the iTNC 530...
Page 61: ...Introduction...
Page 83: ...Programming Fundamentals File Management...
Page 130: ...130 Programming Fundamentals File Management 3 4 Working with the File Manager...
Page 131: ...Programming Programming Aids...
Page 153: ...Programming Tools...
Page 187: ...Programming Programming Contours...
Page 217: ...Programming Data Transfer from DXF Files...
Page 235: ...HEIDENHAIN iTNC 530 235 Programming Subprograms and Program Section Repeats...
Page 252: ...252 Programming Subprograms and Program Section Repeats 8 6 Programming Examples...
Page 253: ...Programming Q Parameters...
Page 301: ...Programming Miscellaneous Functions...
Page 325: ...Programming Special Functions...
Page 380: ...380 Programming Special Functions 11 8 Working with Cutting Data Tables...
Page 381: ...Programming Multiple Axis Machining...
Page 417: ...Programming Pallet Editor...
Page 437: ...Manual Operation and Setup...
Page 499: ...Positioning with Manual Data Input...
Page 505: ...Test Run and Program Run...
Page 536: ...536 Test Run and Program Run 16 7 Optional Program Run Interruption...
Page 537: ...MOD Functions...
Page 574: ...574 MOD Functions 17 21 Configuring the HR 550 FS Wireless Handwheel...
Page 575: ...Tables and Overviews...
Page 604: ...604 Tables and Overviews 18 4 Exchanging the Buffer Battery...