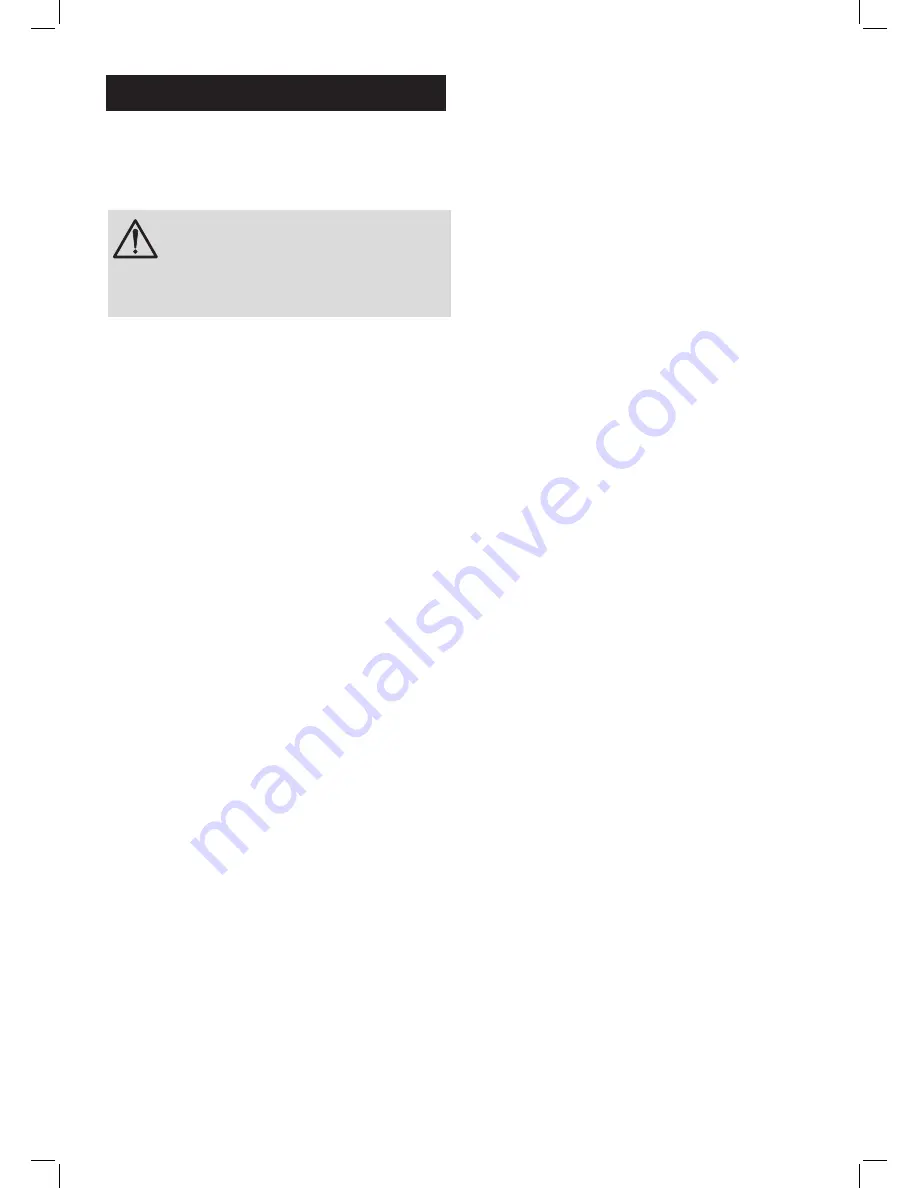
23
7. Commissioning
7.1 General
After filling the installation with water in the previous
section please follow the following steps to complete
the installation of the unit.
WARNING
DO NOT operate the immersion heaters or
primary circuit until the cylinder has been
filled with water.
7.2 Checklist before commissioning
`
Check all water connections for leaks and rectify
as necessary.
`
Turn off mains water supply.
`
Remove the pressure reducing valve head work to
access the strainer mesh, clean and re-fit.
`
Turn the water supply back on.
`
Manually open, for a few seconds, each relief valve
in turn, checking that water is discharged and runs
freely through the tundish and out at the discharge
point.
`
Ensure that the valve(s) reseat satisfactorily.
7.3 Commissioning procedure
Direct units
`
Switch on electrical supply to the immersion
heater(s) and allow the cylinder to heat up to normal
working temperature (60 - 65°C recommended).
`
If necessary the temperature can be adjusted
by inserting a flat bladed screwdriver in the
adjustment spindle on front of the immersion
heater (ELEMENT) control thermostat and rotating
(see Fig. 14 page, 20 for details of how to adjust).
The adjustment represents a temperature range of
10°C to 70°C.
`
Check the operation of thermostat(s) and that no
water has issued from the expansion relief valve
or temperature/pressure relief valve during the
heating cycle.
Indirect units
`
Fill the indirect (primary) circuit following the boiler
manufacturer’s commissioning instructions.
`
To ensure the cylinder primary heat exchanger is
filled, the 2 port motorised valve (supplied) should
be manually opened by moving the lever on the
motor housing to the MANUAL setting. When
the primary circuit is full return the lever to the
AUTOMATIC position.
`
Switch on the boiler, ensure the programmer is
set to Hot Water and allow the cylinder to heat
up to a normal working temperature (60 - 65
o
C
recommended).
`
If necessary the temperature can be adjusted by
inserting a flat bladed screwdriver in the adjustment
spindle on front of the indirect (BOILER) thermostat
and rotating (see Fig. 14, page 20 for details
of how to adjust). The adjustment represents a
temperature range of 10°C to 70°C.
`
Check the operation of thermostat(s) and that no
water has issued from the expansion relief valve
or temperature/pressure relief valve during the
heating cycle.
`
Remove the filling loop.
7.4 Benchmark
Benchmark
The cylinder is covered by the Benchmark Scheme
which aims to improve the standards of installation
and commissioning of domestic heating and hot water
systems in the UK and to encourage regular servicing
to optimise safety, efficiency and performance.
Benchmark is managed and promoted by the Heating
and Hotwater Industry Council. For more information
visit www.centralheating.co.uk.
Please ensure that the installer has fully completed the
Benchmark Checklist (see page 34) of this manual and
that you have signed it to say that you have received a
full and clear explanation of its operation. The installer is
legally required to complete a commissioning checklist
as a means of complying with the appropriate Building
Regulations (England & Wales).
All installations must be notified to Local Area Building
Control either directly or through a Competent
Persons Scheme. A Building Regulations Compliance
Certificate will then be issued to the customer who
should, on receipt, write the Notification Number on the
Benchmark Checklist.
This product should be serviced regularly to optimise
its safety, efficiency and performance. The service
engineer should complete the relevant Service Record
on the Benchmark Checklist after each service.
The Benchmark Checklist may be required in the
event of any warranty work.
Summary of Contents for Megaflo Eco 125DD
Page 34: ...34 Benchmark checklist...
Page 35: ...35 Commissioning service records...
Page 38: ...38 NOTES...
Page 39: ...39 NOTES...