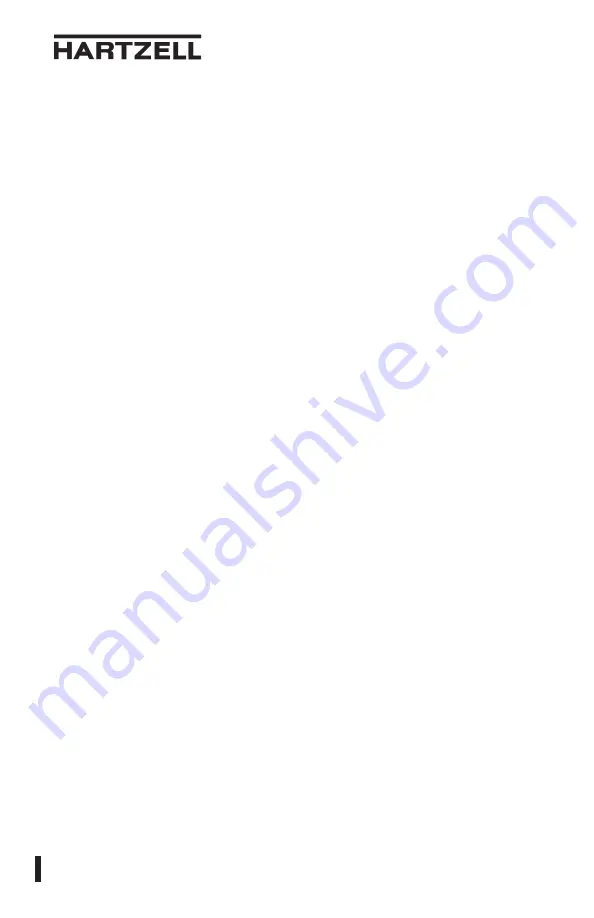
Propeller Owner’s Manual
139
DESCRIPTION AND OPERATION
61-00-39
Page 2-6
Rev. 17 Apr/20
While the propeller is operating, the following forces are
constantly present: 1) spring force, 2) counterweight force,
3) centrifugal twisting moment of each blade, and 4) blade
aerodynamic twisting forces. The spring and counterweight
forces attempt to rotate the blades to higher blade angle,
while the centrifugal twisting moment of each blade is
generally toward lower blade angle. Blade aerodynamic
twisting force is usually very small in relation to the other
forces and can attempt to increase or decrease blade angle.
The summation of the propeller forces is toward higher
pitch (low RPM) and is opposed by a variable force toward
lower pitch (high RPM). The variable force is oil under
pressure from a governor with an internal pump, which
is mounted on and driven by the engine. The oil from the
governor is supplied to the propeller and hydraulic piston
through a hollow engine shaft. Increasing the volume of oil
within the piston and cylinder will decrease the blade angle
and increase propeller RPM. Decreasing the volume of oil
will increase blade angle and decrease propeller RPM. By
changing the blade angle, the governor can vary the load on
the engine and maintain constant engine RPM (within limits),
independent of where the power lever is set. The governor
uses engine speed sensing mechanisms that allow it to
supply or drain oil as necessary to maintain constant engine
speed (RPM).
If governor supplied oil is lost during operation, the propeller
will increase pitch and feather. Feathering occurs because
the summation of internal propeller forces causes the oil to
drain out of the propeller until the feather stop position is
reached.
Normal in-flight unfeathering is accomplished when the pilot
positions the propeller condition lever into the normal flight
(governing) range and restarts the engine. As engine speed
increases, the governor supplies oil to the propeller, and the
blade angle decreases.