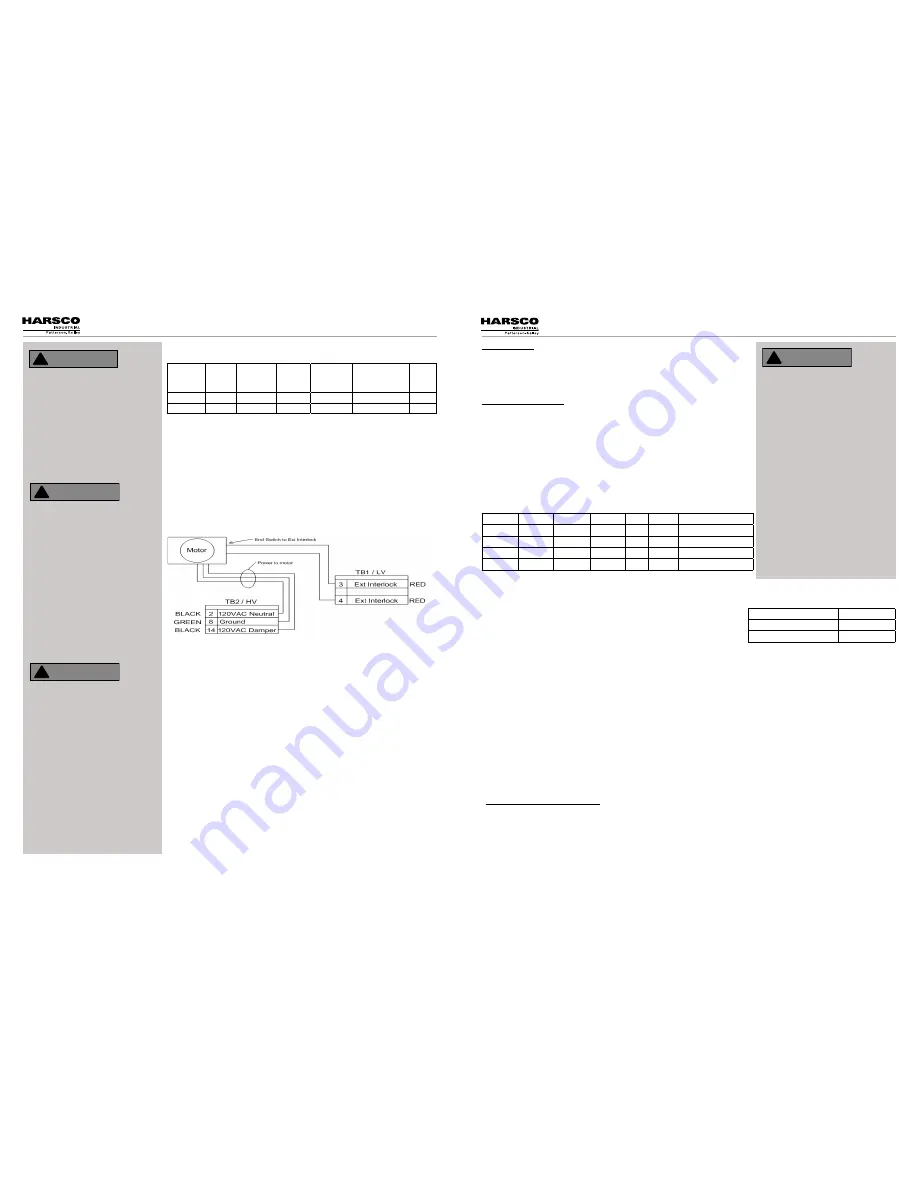
12
Harsco Industrial, Patterson-Kelley Technical Service 1.877.728.5351
INST
ALLA
TION
Gas Fired Boiler
13
Harsco Industrial, Patterson-Kelley Technical Service 1.877.728.5351
INST
alla
TION
Gas Fired Boiler
Design and installation of venting
systems should be done only
by qualified and knowledgeable
venting systems personnel and
in accordance with vent system
manufacturer’s installation
instructions. Installing a boiler
or vent system using improper
installation methods or materials
can result in serious injury or
death due to fire or asphyxiation.
!
WARNING
Before connecting a boiler to a
venting system, it must be
determined whether the boiler is
to be installed in a conventional
or direct vent configuration. In the
US, provisions for combustion
and ventilation air must be in
accordance with
NFPA 54/ANSI
Z223.1
, National Fuel Gas Code,
latest edition, or applicable
provisions of the local building
codes. In Canada, combustion
and ventilation air openings shall
comply with
CAN/CSA B-149.1
Natural Gas and Propane
Installation Code.
!
WARNING
The venting materials listed are
intended for the venting of gas
burning appliances only. Do not
use these venting materials for
venting liquid or solid fuel (such
as oil, kerosene, wood or coal)
appliances.
Maintain clearances to
combustibles as listed in the
vent manufacturer’s installation
instructions or as set forth in the
codes and standards listed in this
section.
Do not use these vent pipes for
incinerators of any sort.
This boiler is not certified for
use with PVC venting. Use of
PVC venting may result in vent
failure and possible serious
injury or death.
!
WARNING
For correct installation of vent
system, read all of these
instructions and refer to vent
manufacturer’s instructions.
Failure to use a proper vent
system (types and materials),
as described in this manual will
void the boiler warranty and may
result in rapid deterioration of the
venting system, creating a health
or life safety hazard.
Faulty vent installation can allow
toxic fumes to be released into
living areas. This may cause
property damage, serious bodily
injury or death.
!
WARNING
Boiler size
Nom.
vent
size
stainless
Vent
Adapter
Vent
adapter
size
Boiler
Combustion
Air inlet
Combustion air
N.C. motorized
Damper
length
SC-3000
10”
2640000133 10”
12”
1004906946
12”
SC-4000
10”
2640000133 10”
12”
1004906989
14”
Required stainless steel Vent Adapters and Category II motorized Dampers
This table is for information only. Combustion air dampers and vent
adapters are listed for use of design and may or may not be specific to
your application.
The optional, but required for Category II venting, normally-closed
motorized combustion air damper operates on 120
VAC
and features an
end limit switch wired into the boiler’s external interlock circuit. Upon a
call for heat, the boiler’s combustion air damper relay will energize and
drive the damper open. Once the damper reaches the fully-open position,
the end limit switch makes contact and closes the external interlock circuit
allowing the boiler to fire. The diagram below shows the wiring necessary
to install the normally-closed motorized damper.
3.5.1.1 Gas Vent Categories
Several codes and standards have categorized appliances in accordance
with the flue gas temperature and pressure produced by the appliance.
The applicable categories are defined as follows:
•
Category II:
An appliance that operates with a non-positive vent
static pressure and with a vent temperature that may cause excessive
condensate production in the vent.
•
Category IV:
An appliance that operates with a positive vent static
pressure and with a vent temperature that may cause excessive
condensate production in the vent.
•
Direct Vent:
An appliance that is constructed and installed so that all
air for combustion is derived directly from outdoors and all flue gases are
discharged to the outdoors.
3.5.1.2 Venting materials for Flue/exhaust systems
The
P-K SONIC™
boilers are dual certified as a Category II and Category IV
appliances, which vents with a temperature that is likely to cause condensation
in the vent. Therefore, any venting system used with the
P-K SONIC™
boiler
must comply with the requirements for either Category II or Category IV
venting systems as specified in the latest edition of
NFPA 54/ANSI Z223.1
in the
US or the latest edition of
CAN/CSA B-149.1
in Canada.
Acceptable materials for Venting systems
Manufactured Venting Systems
us and Canada:
AL29-4C Stainless Steel Vent Systems listed and labeled to UL1738 Venting Systems for Gas-Burning Appliances,
Categories II, III, and IV
316L Stainless Steel where certified and warranted by the vent manufacturer for venting of Category II, III, or IV appliances
As per ANsI Z21.13b-2012 * CsA 4.9b-2012:
•
The use of cellular core PVC, CPVC and Radel as venting materials is
prohibited.
•
The use of external insulation on plastic vent pipe is prohibited.
model
Country Al29-4C 316l ss PVC
CPVC
POlyPROPyleNe
SC-3000
US
Yes
Yes
No
Yes
Note 2
SC-4000
US
Yes
Yes
No
Yes
Note 2
SC-3000 Canada
Yes
Yes
No
Note 1
Note 1
SC-4000 Canada
Yes
Yes
No
Note 1
Note 1
Acceptable Venting materials
Note 1: When this material is used for venting, it must be listed to ULC-S636.
Note 2: When this material is used for venting, it must be listed to UL-1738.
CPVC Venting
us:
CPVC pipe conforming to ASTM F441. Sch 80 fittings conforming to ASTM
F439. Joints are to be sealed with solvent conforming ASTM 493.
Canada:
CPVC Pipe, Fitting and Sealant listed and labeled to ULC S-636
Standard for Type BH Venting Systems.
Polypropylene Venting
us and Canada:
Polypropylene such as InnoFlue from Centrotherm
or PolyPro from DuraVent or other listed manufacturers. When used, the
same manufacturer's material must be used throughout the system. It is not
permissible to use material from different manufacturers within the same system.
3.5.2 Combustion Air materials and sizes
The air intake duct can be fabricated from PVC, CPVC, single wall
galvanized steel, or other suitable materials. The duct must be rigid
enough to maintain the full required cross sectional area under all
operating conditions. Proper sealing of the intake ductwork is necessary
to prevent infiltration of air from conditioned space. Joints in PVC or CPVC must be cemented. For galvanized
duct, wrap each joint and seam with adhesive aluminum tape or other sealant. The installation of a bird screen on
the intake termination is recommended. Ensure that the screen does not become blocked with snow, ice, insects
etc. Combustion air duct should be designed with maximum 0.22” wc friction loss.
Combustion air must be free from dust, lint, etc. The presence of such materials in the air supplied to the burner
could cause nuisance "Low Air" shutdowns or premature burner failure. The boiler should not be operated during
construction while the possibility of drywall dust, demolition dust, etc. exists.
The combustion air supply must be completely free of chemical fumes which may be corrosive when burned in
the boiler. Common chemicals which must be avoided are fluorocarbons and other halogenated compounds,
most commonly present as refrigerants or solvents, such as Freon, trichloroethylene, perchloroethylene, chlorine,
etc. These chemicals, when burned, form acids which quickly attack the boiler and the boiler stack. The result is
improper combustion and premature boiler failure.
P-K sONIC™ Boiler model Required sCFm
SC-3000
629
SC-4000
839
Table 3.5.1
Table 3.5.1.2
Table 3.5.3