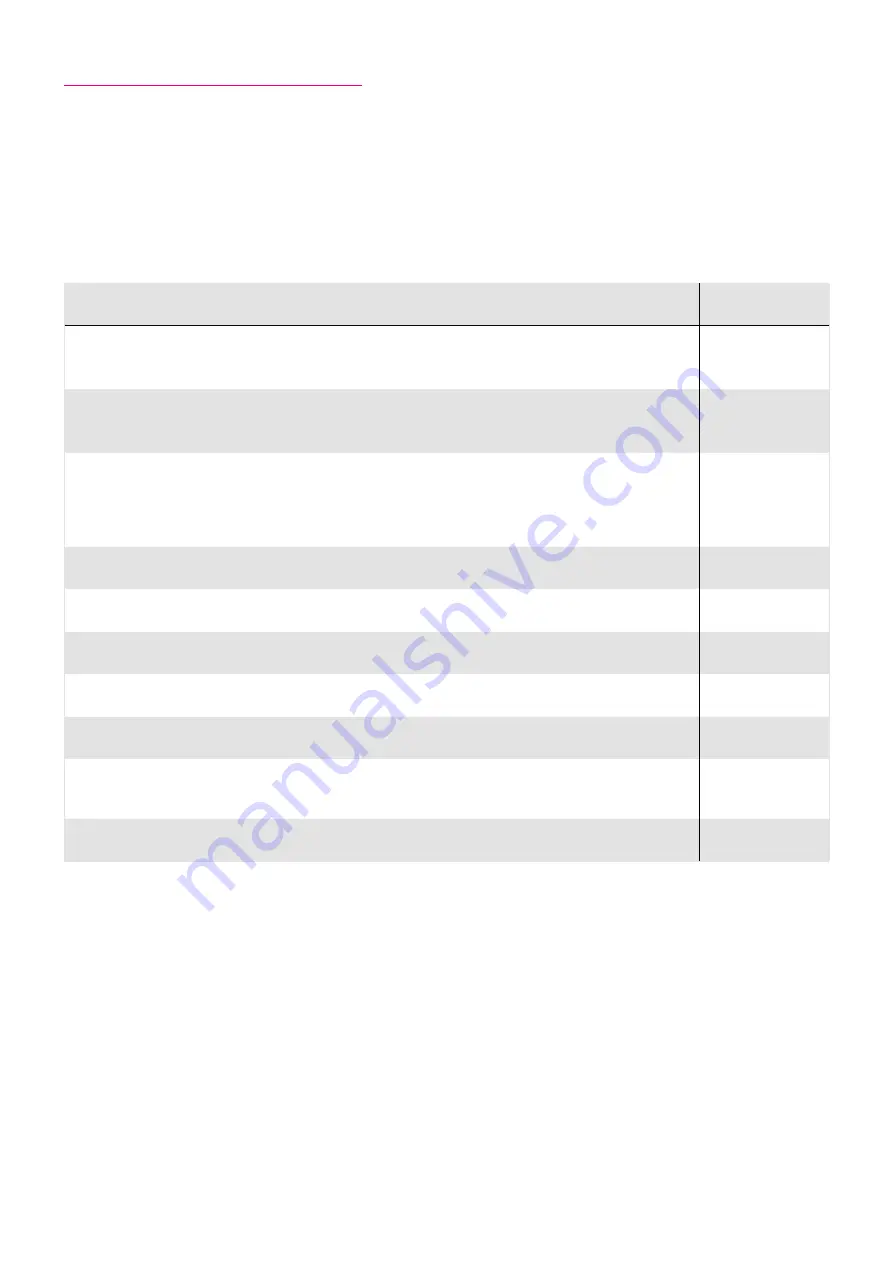
22
1019658 11/2014
* Depending on the application, a secondary gear stage may be useful. Please contact Harmonic Drive AG for more information.
Application
f
n
Slowly rotating turntables, base axes of slow moving welding robots (not laser welding), slowly rotating welding and swinging
tables, gantry robot axes
≥ 4
Base axes of revolute robots, hand axes of revolute robots with low requirements regarding dynamic perfomance, tool
revolvers, tool magazines, swivelling and positioning axes in medical and measuring devices
≥ 8
Standard applications in general mechanical engineering, tilting axes, palette changers, highly dynamic tool changers, revolvers
and magazines, hand axes of robots, scara robots, gantry robots, polishing robots, dynamic welding manipuators, base axes of
welding robots (laser welding), swivelling and positioning axes of medical equipment
≥ 15
B/C axes in 5 axis grinding machines, hand axes of welding robots (laser welding), milling heads for plastics machining
≥ 20
C axes in turning machines, milling heads for light metal machining, milling heads for woodworking (chipboards etc.)
≥ 25
Milling heads for woodworking (hardwood etc.)
≥ 30
C axes in turning machines*
≥ 35
Milling heads for metal machining*, B axes in turning milling centers for metal machining
≥ 40
Milling heads for metal machining*, B axes in turning milling centers for metal machining with high requirements regarding
surface quality*
≥ 50
Milling heads for metal machining with very high requirements regarding surface quality*
≥ 60
In addition to the “Torque Based Dimensioning” stated on page 19, we recommend that you carry out a selection based on
stiffness. For this, the values provided in table 22.1 for the individual resonance frequencies recommended for each application
should be taken into account.
4.1.3 Stiffness Based Dimensioning
Table 22.1
[Hz]