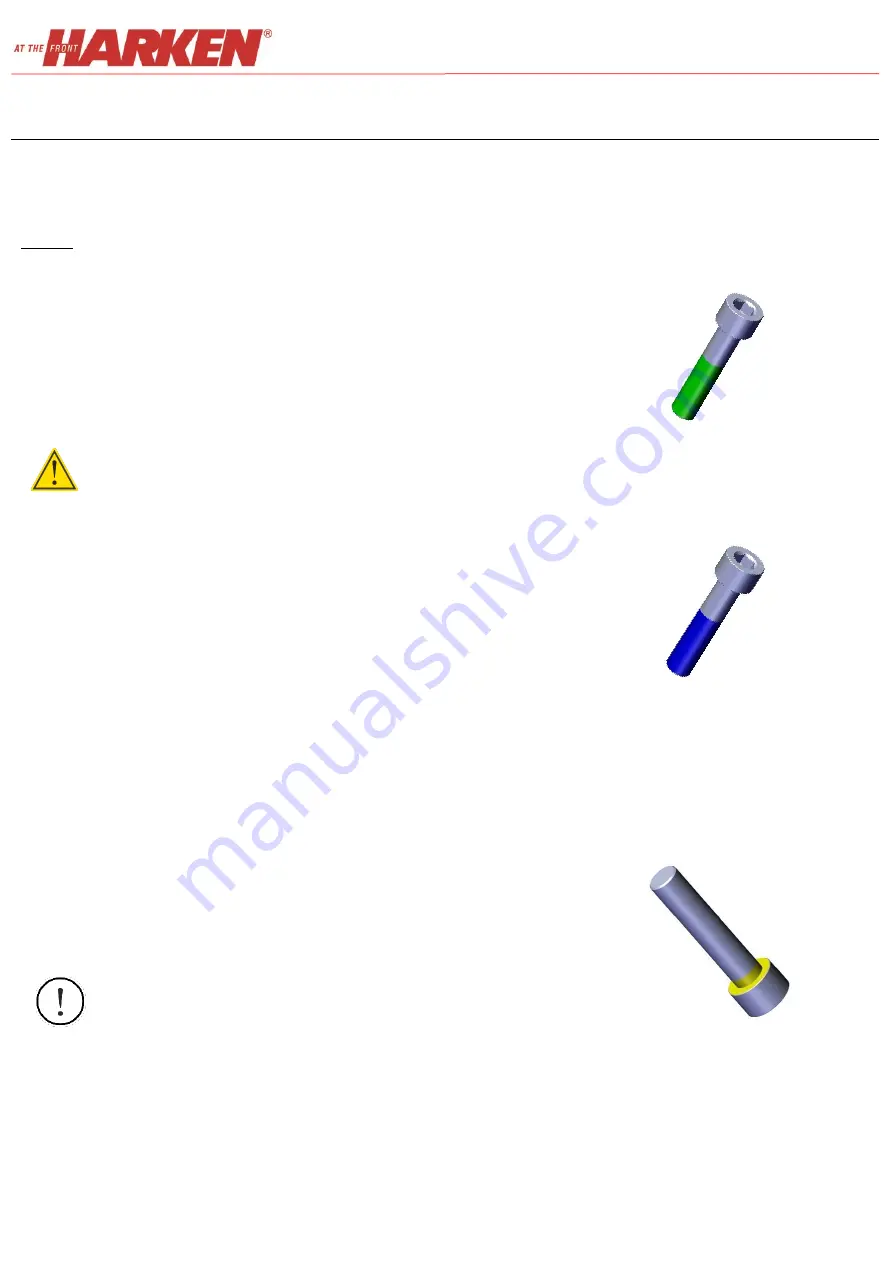
Rev.#0
35
16.1 Internal maintenance procedure
1. Maintenance products
The maintenance products listed below must be used:
Types
Strong threadlocker
– Green (i.e. LOCTITE
®
270)
Clean the parts and apply the product, spreading it all over the thread
as shown.
Assemble the parts and wait at least 45 minutes before use. To
remove screws sealed with threadlocker, you may need to heat the
parts to reduce the effect.
WARNING!
Do not apply this product to screws into carbon components.
Medium threadlocker
– Blue (i.e. LOCTITE
®
243)
Clean the parts and apply the product, spreading it all over the thread
as shown.
Assemble the parts and wait at least 45 minutes before use.
Generally, for use on all screws, requires no heating before removal.
OIL Harken - BK4521
Apply the oil to the parts indicated in the internal maintenance
pocedure below, taking care to lubricate the surfaces completely.
Rotate or slide the oiled parts to distribute the product in a uniform
way. Remember to oil the pawls and do not use grease on them.
Anti-corrosive lubricants (i.e. TEFGEL
®
)
Apply sacrificial anodes or anti corrosive lubricants to prevent
electrolytic corrosion between different metals in contact with
aluminum
NOTE! Apply the anti-corrosive lubricant with a brush on clean
surfaces.
Summary of Contents for Air 250
Page 1: ...USER AND MAINTENANCE MANUAL Winch Air 250 300...
Page 2: ...Rev 0 2...
Page 15: ...Rev 0 15 Winch Air Powered handled Base sheave Winch Air Powered handled...
Page 40: ...Rev 0 40 Step 7 Step 6 Step 8 Use anti corrosive lubricant under the head of the screws...
Page 41: ...Rev 0 41 Use anti corrosive lubricant under the head of the screws Step 9 Allen wrench size 3...
Page 42: ...Rev 0 42 Step 12 Step 10 Step 11 The pin of the spring is indexed into the housing grey item...
Page 45: ...Rev 0 45 Step 18 Step 19 Step 20 Step 21...