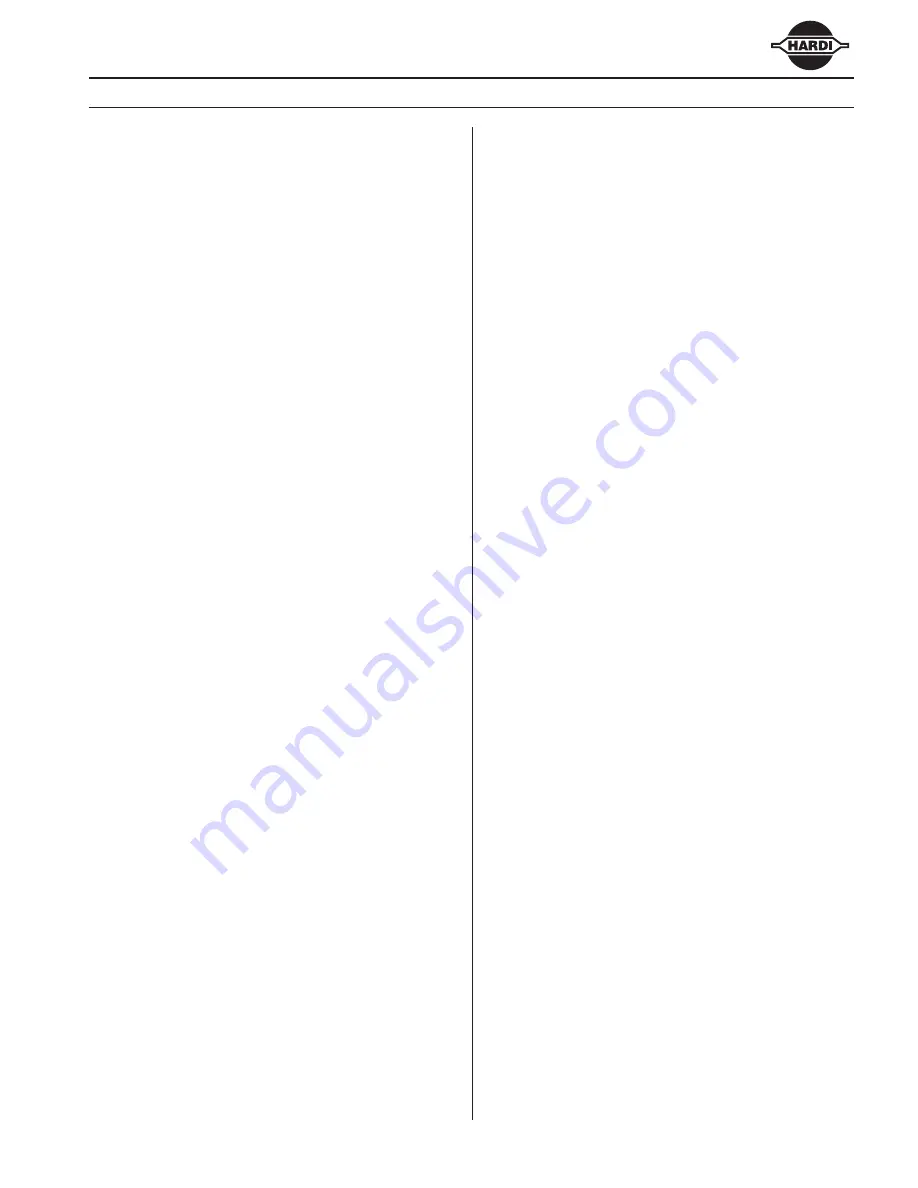
mercury
3
HARDI
®
MERCURY OPERATOR'S MANUAL
Index
Description.................................................. 5
Zone
concept........................................ 5
Basic description of the machine.......... 6
Frame ........................................... 6
Tank.............................................. 6
Pump ............................................ 6
Manifold
system ........................... 6
Axial
blower .................................. 6
Filters............................................ 6
Identifi
cation
plate ........................ 6
Use of the sprayer ................................ 7
Recommendations ............................... 7
Safety instructions ..................................... 8
Operating the sprayer safely ................ 8
Handling chemical products safely....... 9
Local poison information center ........... 9
Mistblowing
technique ........................ 10
Connecting the sprayer ............................11
Wheel
jackstand ..................................11
Drawbars ............................................ 12
Swivel
drawbar
(standard) ......... 12
Turnable hitch drawbar............... 12
Adjusting the drawbar length .............. 13
P.T.O.
shaft ......................................... 13
Installation of P.T.O. shaft........... 14
Wheel
types........................................ 15
Axle
types ........................................... 15
Suspension......................................... 16
Hydraulic
system ................................ 17
Setting up .................................................. 18
Suction
fi
lter........................................ 18
Cleaning the Suction Filter ......... 18
Pressure
fi
lters ................................... 19
Fan
................................................... 19
Main
tank............................................ 20
Clean water tank ................................ 21
Nozzles............................................... 21
Agitation.............................................. 22
Powder
mixer ..................................... 22
Operating the sprayer .............................. 23
Plumbing diagram ...................................... 23
Diaphragm
pumps .............................. 23
Manifold Valve and Pressure Valve .... 24
Pressure
Manifold
Valve............. 24
Pressure
Regulator
Valve........... 24
Hyd. controlled section valves............ 25
Axial blower units..................................... 26
Optional
defl
ectors ............................. 26
V-L
Defl
ector............................... 26
JET
Defl
ector.............................. 26
Channel
kit ................................. 26
Safety
grills......................................... 27
Angling of the fan blades .................... 28
Air outlet width adjustment ................. 30
Gearbox oil change ............................ 31
Air fl ow and power consumption charts:
UNIT
SF45 ................................. 32
UNIT
SF65 ................................. 33
UNIT
SF85 ................................. 34
Maintenance.............................................. 35
Lubrication.......................................... 35
P.T.O.
shaft ................................. 35
Diaphragm
pump........................ 35
Hyd. controlled section valves.... 35
Drawbar...................................... 36
Axles........................................... 36
Filters
and
fi
ttings ....................... 36
Diaphragm
pumps .............................. 37
Nozzles............................................... 37
Maintenance
intervals ........................ 38
Cleaning - Basic concepts....................... 39
Cleaning
procedures .......................... 39
The chemical product ................. 39
Legislation .................................. 39
Cleaning and the soakaway ....... 39
The
sprayer ................................ 39
Cleaning the sprayer .......................... 40
Unforeseen
interruptions .................... 40
Off-season storage................................... 41
Off-season
storage ............................. 41
Preparation after off-season storage .. 42
Troubleshooting ....................................... 43
Technical data........................................... 46
Dimensions......................................... 46
Weights .............................................. 46
Wheels ............................................... 46
Diaphragm
pumps .............................. 47
General specifi cations ............................. 48
Warranty Policy and Conditions ............. 50
Notes.......................................................... 52
Summary of Contents for mercury
Page 1: ...67301503 04 03 mercury Operator s Manual ...
Page 2: ......
Page 4: ......
Page 54: ...mercury 52 HARDI MERCURY OPERATOR S MANUAL Notes ...
Page 55: ......