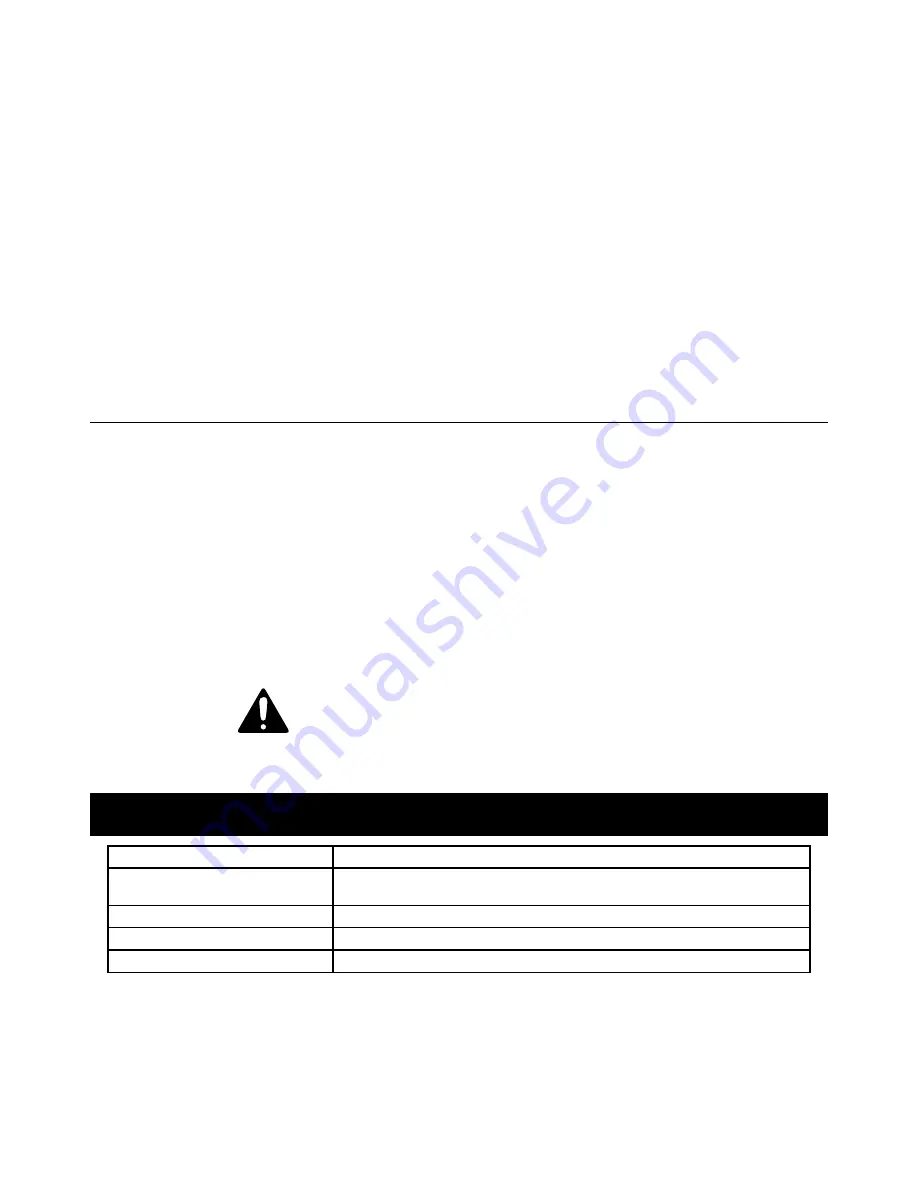
Page 4
For technical questions, please call 1-888-866-5797.
Item 63785
35.
If working on a metal wall, ceiling, etc.,
prevent ignition of combustibles on the
other side by moving the combustibles to a
safe location.
If relocation of combustibles is
not possible, designate someone to serve as
a fire watch, equipped with a fire extinguisher,
during the cutting process and for at least one
half hour after the cutting is completed.
36.
Do not weld or cut on materials having
a combustible coating or combustible
internal structure, as in walls or ceilings, without
an approved method for eliminating the hazard.
37.
Do not dispose of hot slag in containers
holding combustible materials.
38.
After welding, make a thorough examination
for evidence of fire.
Be aware that easily
visible smoke or flame may not be present
for some time after the fire has started.
39.
Do not apply heat to a container that has held
an unknown substance or a combustible
material whose contents, when heated,
can produce flammable or explosive vapors.
Clean and purge containers before applying heat.
Vent closed containers, including castings,
before preheating, welding, or cutting.
40.
Unplug before maintenance.
Unplug the Welder
from its electrical outlet before any inspection,
maintenance, or cleaning procedures.
Gas Shielded Welding - Cylinder Safety
Cylinders can explode when damaged.
1.
Do not weld on a pressurized or closed cylinder.
2.
Do not allow an electrode holder,
electrode, welding torch, or welding
wire to touch the cylinder.
3.
Keep cylinders away from any electrical circuits,
including welding circuits.
4.
Keep protective cap in place over the valve
except when the cylinder is in use.
5.
Use only correct gas shielding equipment
designed specifically for the type of welding
you will do.
Maintain this equipment properly.
6.
Protect gas cylinders from heat, being struck,
physical damage, slag, flames, sparks, and arcs.
7.
Use proper procedures to move cylinders.
SAVE THESE INSTRUCTIONS.
Specifications
Cable Length
12 - 1/2’
Duty Cycle
150 A @ 60 % duty cycle (DC)
115 A @ 60 % duty cycle (AC)
Tungsten Range
0.020″ - 5/32″ (0.5 - 4.0 mm)
Weight
5.5 lbs.
Cooling
Air cooled