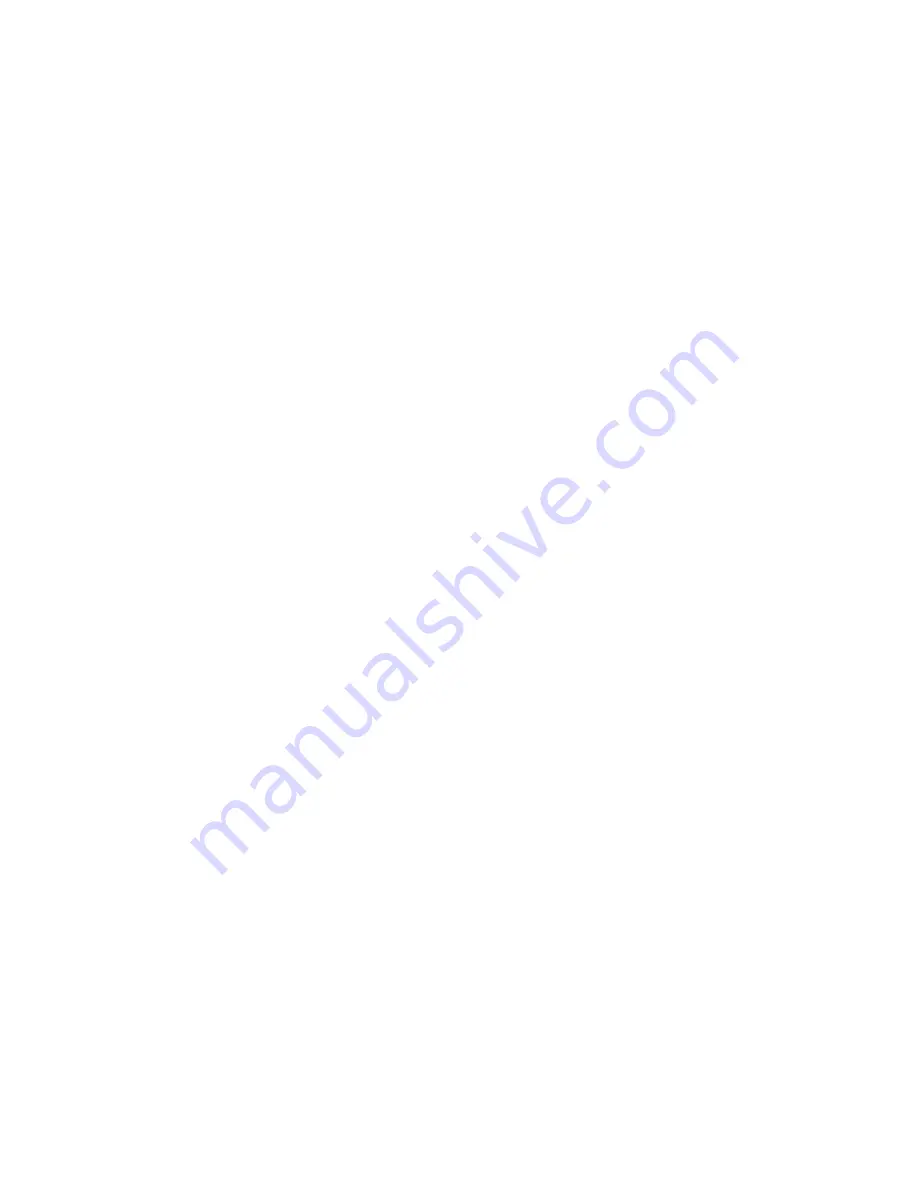
8
F100d
JAN 2011
INTRODUCTION TO DEFROSTING
While the most important component of the defrost
system is the controller, it is important to understand
the reasoning behind each defrost step as well as
other elements which contribute to a successful
and efficient defrost sequence. It is obvious that an
evaporator in defrost will not have a cooling effect on
the refrigerated space, therefore a minimum amount
of time in defrost is desirable. However, it is more
important to operate a safe and efficient defrost
than a speedy one. Defrosting of industrial/large
commercial evaporator coil surfaces is predominately
accomplished by the use of refrigerant hot (discharge)
gas. Other possible methods include: water, air,
electric assisted, or combination of several. Even
though hot gas defrosting is explained here, the
principles are generally the same whatever method
is used.
Key elements of a successful defrost system include
a reliable hot gas supply, control valves and a defrost
controller. The hot gas supply at the evaporator
should be free of condensate, sufficient in pressure
and quantity to effectively remove ice and frost from
the coil surfaces. Valves must be in place to control
the flow of hot gas into the evaporator, maintain
the pressure inside evaporator above an equivalent
saturation pressure of 32ºF (0°C) during defrost,
facilitate the removal of refrigerant liquid condensate,
limit the entry of hot gas to suction line and minimize
pressure shock when normal refrigeration is resumed.
The defrost controller should sequence control valves
in a manner which minimizes stress to evaporators,
piping and compressors. It should stop normal
refrigeration and pumpout the evaporator to expose
more internal coil surface to the incoming hot gas.
Optionally introduce hot gas via a smaller valve to
reduce pressure shock to evaporator, then continue
by opening a larger hot gas supply valve, but not for
an excessive amount of time. Reduce the pressure
inside the evaporator before opening main suction
valve to avoid suction pressure shock. Start normal
refrigeration but delay the fans until remaining water
droplets freeze to coil surfaces.
On the next page are typical application examples of
hot gas defrosting evaporators with control valves.
Although there are many ways to circuit a defrost
system, these illustrate some basic methods which
apply to most. In general, hot gas is introduced into
the top of the evaporator for even heat distribution
throughout coil. Refrigerant condensate is removed
from the bottom of the evaporator to minimizes the
amount of hot gas entering the suction line and to
provide a means of oil removal. Typically the defrost
relief regulator is set at about 70 psig (5 bar) for
ammonia. When a defrost condensate liquid drainer is
used, an outlet pressure regulator in the hot gas supply
line should be used to limit the internal evaporator
pressure. Check valves are installed after the liquid
solenoid valve to prevent higher pressure gas from
entering the liquid supply line during defrost. Also,
check valves are placed between the evaporator and
drain pan to keep the pan from accumulating frost
during the refrigeration cycle.
SOFT GAS VALVE
The purpose of the soft gas valve is to gradually
increase the pressure inside evaporator before
introducing full flow hot gas. This reduces the
possibility of pressure shock to coil which often has
residual liquid from the refrigeration cycle. The soft
gas valve should open several minutes prior to the main
hot gas valve. The evaporator need not be completely
at full hot gas pressure before hot gas valve is opened.
Generally, a soft gas valve should be used when the
hot gas solenoid valve is 1½” or larger. However, the
installation of a soft gas valve could be considered
on smaller circuits if the evaporator temperature is
below 0°F (-18°C) or it exhibits disturbances upon
opening of the hot gas valve.
The ideal soft gas valve size depends on many factors
including: evaporator volume, the use of a pumpout
step which removes residual refrigerant liquid, the
quality and quantity of the hot gas supply pressure,
etc. In most cases, a ½” port soft gas valve should
be sufficient; such as Hansen Type HS8A. A hand
expansion valve (regulator) or globe valve can be
installed just after the soft gas valve to fine tune
sizing.
EQUALIZE VALVE
The purpose of an equalize valve is to prevent
disturbances when opening main valve leading from
newly defrosted evaporator to suction pressure.
The equalize valve is to be opened several minutes
prior to the main valve. The evaporator need not be
completely equalized to suction pressure, rather the
purpose is to reduce the pressure differential to an
acceptable level. In general, it is recommended that
an equalize valve be installed on evaporators having
15 tons (53 kW) or greater capacity or a 2½” and larger
suction line. However, equalize valves may need to
be installed on smaller evaporators depending on
degree of disturbance upon opening main suction
valve. Many factors can increase the degree of
disturbance, including: the pressure difference
between evaporator and suction, the amount of
liquid remaining in evaporator, the size of valves, the
complexity of piping, and etc.
The equalize valve size is a function of the evaporator
volume and the pressure difference. The valve typically
can be 3 or 4 sizes below main valve, but not less than
½” port. A hand expansion valve (regulator) or globe
valve can be installed just after the equalize valve to
fine tune sizing.