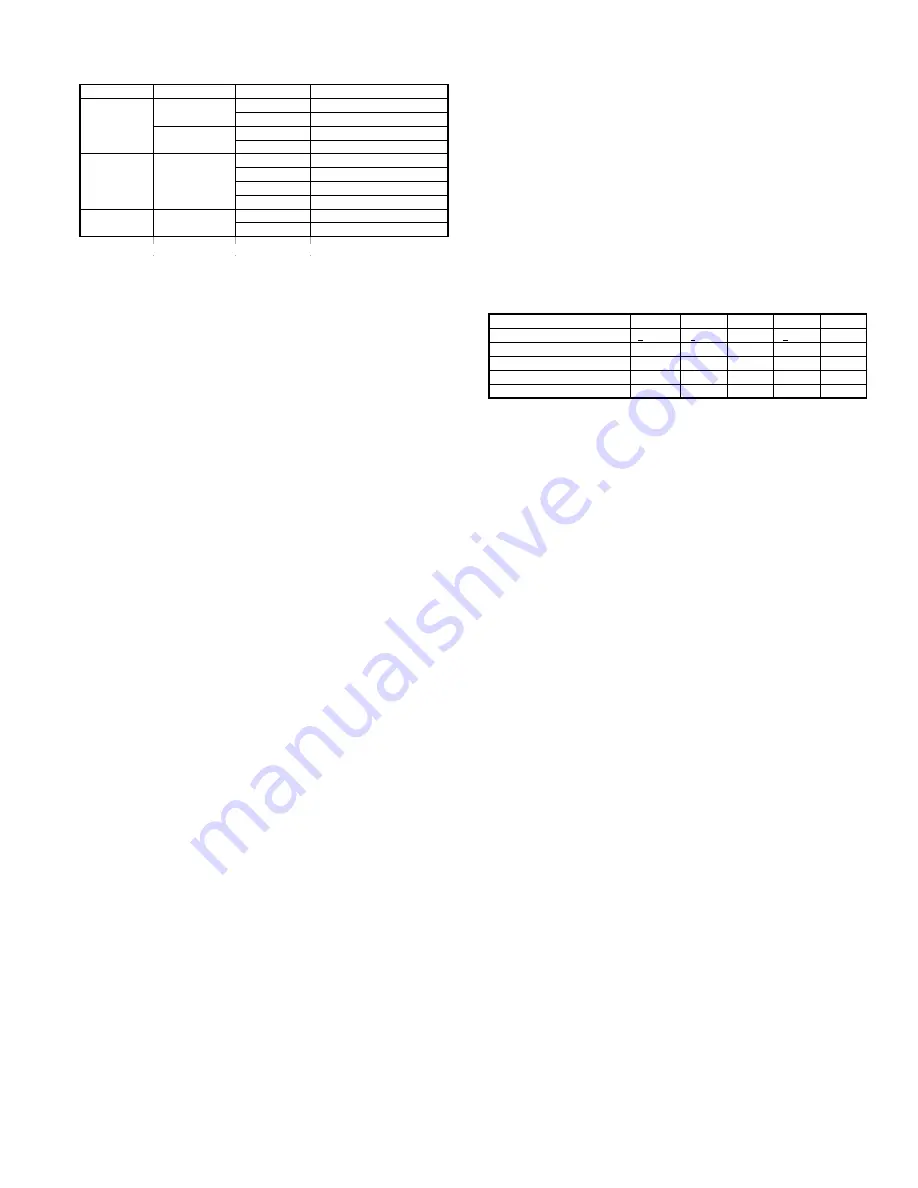
7
A100h
JANUARY 2020
• MODBUS flag for warm-up is set.
• Buzzer is off.
• Relay state is “no alarm.”
• Gas reading is invalid.
3. Observe normal operation:
• Green LED is steady on.
• MODBUS flag for warm-up is cleared.
• Buzzer is off.
• Relay state is “no alarm.”
• Gas reading is valid.
The detector may also enter several special states, these
are indicated below by the specific analog output levels
indicated:
GAS DETECTOR TESTING
Field testing of the gas detector is normally done for three
reasons. The first is to determine if the gas detector is
responding to the specific gas. This test is sometimes
called a “bump” test. The frequency of the test is usually
stated in the facilities Process Safety Management (PSM)
document, but not less than every six months.
The second reason for gas detector testing is to be sure
the gas detector is properly calibrated. Depending on
the sensor element type, the sensor element sensitivity
will change with time. In particular, electrochemical
sensor elements use a material that is depleted with
time. The length of time varies depending on the amount
of exposure to the target gas, the ambient temperature
and humidity, and changes to temperature and humidity
range. Atmospheres that are very dry or very humid will
shorten the life of a sensor element.
The third reason is to be sure the gas detector
output triggers the alarms on the monitor, PLC, Gas
Alert System, horn or lights. All gas detectors are
recommended to be recalibrated at least every 6 months.
All detectors should be recalibrated immediately after
exposure to a large concentration of the target gas.
Note:
Insurance companies, local and state agencies may
require more frequent testing and calibration; refer to
insurance carrier mandates as well as local and state codes
DETECTOR BUMP TEST
A bump test is a live test of the detector to verify the
detector responds to the target gas and all connected
alarm devices are operating accordingly. Prior to test, it
is recommended all involved persons are informed about
the test as certain alarms might have to be inhibited.
1. Connect adapter and proper PPM gas cylinder to
the sensor element.
2. If desired, disable or silence audible alarms.
3. Apply a sufficiently high concentration of the
target gas to trigger alarm condition, but NOT
pure refrigerant or hydrocarbons.
MODBUS RTU RS-485 INTERFACE
For the MODBUS RS-485 network use a 16 to 24 AWG
3-core, 2 twisted pair+ ground, shielded cable with 120
ohm characteristic impedance (recommended Belden
3106A or equivalent).
The MODBUS address, baud rate, stop bit, parity and
child termination is configured through the setup menu.
No jumpers or hardware switch settings are required.
Ensure the communication parameters within the network,
including any user supplier PLC, are configured identically.
To ensure optimal performance of the MODBUS network,
ensure the following guidelines are implemented:
• Detectors are configured in a single bus topology,
connecting multiple buses in parallel or branching
multiple units from the main bus may introduce
impedance mismatches, reflections, and/or signal
distortions.
• Avoid long stubs when connecting detectors to the
bus (should be less than 3’).
• Detectors at end of bus have 120 ohm terminating
resistor enabled. Terminating resistors may be
enabled via Hansen Gas Detector App.
• A/B signal polarity is maintained throughout RS-
485 network .
• Connect cable shield to drain to physical earth or
ground at the controller only.
• Connect cable shield to (SH) terminal at sensor
• Cable shield integrity is maintained throughout RS-
485 network.
• Do not use shield connection for signal ground.
Use cable that provides dedicated ground
conductor for signal ground. Connect signal
ground to (GND) terminal of sensor.
After all wiring has been completed, power the sensor and
perform a bump test to verify instrument functionality.
START-UP SEQUENCE
After applying power, the instrument will go through a
start-up sequence (initialization, audible/visual test and
self-test sequence). After start-up sequence completes,
the instrument will enter a warm-up period to allow the
sensor element to stabilize before reporting a valid output.
1. Switch power on.
2. Observe the start-up sequence and warm-up phase:
• Green LED will blink at 0.5 HZ for about 5 minutes.
Connec4on
Descrip4on
Label
Wiring Termina4on
Power
24 VDC/VAC in
24V IN: -
24 VDC/VAC neutral/ground
24V IN: +
24 VDC posi4ve / VAC live
24 VDC/VAC out
24V OUT: -
24 VDC/VAC neutral/ground
24V OUT: +
24 VDC posi4ve / VAC live
Digital Output
Modbus Network
Communica4ons
MODBUS: B
RS-485 "B" (inverted)
MODBUS: A
RS-485 "A" (non-inverted)
MODBUS: GND
RS-485 GND
MODBUS: SH
RS-485 Shield
Analog Output
Voltage or Current
output
ANALOG: -
Analog output ground
ANALOG: +
Analog output signal (+)
NOTES:
1. Polarity must not be reversed. 2. for 24 VAC in a daisy chain configura4on, the neutral polarity must be
maintained for all instruments. 3. If analog output is configured for 4-20mA output, ensure the current loop is
connected to a sinking current loop monitor before powering on the instrument.
1
POWER & SIGNAL WIRING TABLE
MODE OF OPERATION
4-20mA
1-5V
0-5V
2-10V
0-10V
Instrument Fault
< 1.2 mA
< 0.3 V
N/A
< 0.6 V
N/A
Offline Mode / Maintenance
3 mA
0.75 V
N/A
1.5 V
N/A
DriH below Zero
3.8 mA
0.95V
N/A
1.9 V
N/A
Measuring Range Exceeded
20.5 mA
5.12 V
5.12 V
10.25 V
10.25 V
Fault on Analog Interface
>21 mA
> 5.25 V
> 5.25 V
> 10.5 V
> 10.5 V
1
TABLE 5
TABLE 4
Connec4on
Descrip4on
Label
Wiring Termina4on
Power
24 VDC/VAC in
24V IN: -
24 VDC/VAC neutral/ground
24V IN: +
24 VDC posi4ve / VAC live
24 VDC/VAC out
24V OUT: -
24 VDC/VAC neutral/ground
24V OUT: +
24 VDC posi4ve / VAC live
Digital Output
Modbus Network
Communica4ons
MODBUS: B
RS-485 "B" (inverted)
MODBUS: A
RS-485 "A" (non-inverted)
MODBUS: GND
RS-485 GND
MODBUS: SH
RS-485 Shield
Analog Output
Voltage or Current
output
ANALOG: -
Analog output ground
ANALOG: +
Analog output signal (+)
NOTES:
1. Polarity must not be reversed. 2. for 24 VAC in a daisy chain configura4on, the neutral polarity must be
maintained for all instruments. 3. If analog output is configured for 4-20mA output, ensure the current loop is
connected to a sinking current loop monitor before powering on the instrument.
1