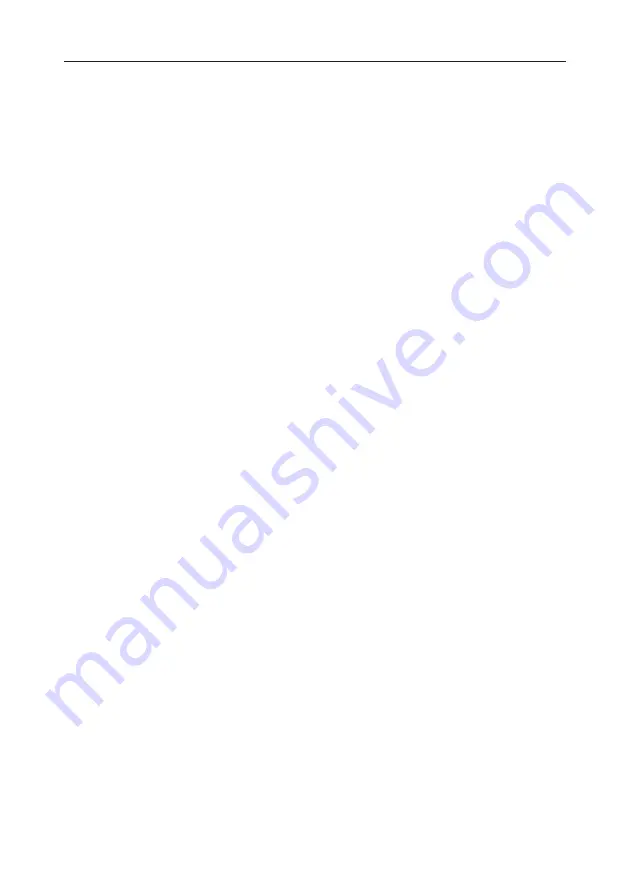
Operation Modes when using Modbus
12
4.1. MODBUS GENERAL STEPS
Prerequisite for HI520 remote operation
The controller must not be in Manual, Calibration, or Local Edit Mode as these modes prevent remote operation.
Steps
1. Ensure remote communication is enabled and serial communication parameters match the Modbus server.
`
Displayed
Й
symbol confirms connection to the server is established.
`
40195
and
40196
Holding Registers contain status and link information that is not password protected.
2. Ensure the controller has the correct Modbus ID set for use with the Modbus server.
HI520
default Modbus ID is1, and configurable range is 1 to 99.
`
Each Modbus device has a configurable ID which must be set in order for the Modbus server to
communicate with the device.
3. Determine if the unit is password protected.
`
If yes, continue with Step 4.
`
If not, skip Step 4 and continue with Step 5.
4. Send a 32‑bit password to the controller using 2 consecutive Write Single Holding register (06) Modbus
Function Codes or a single Write Multiple Holding registers (16) Function Code to the controller. The
password register addresses are:
•
40193
– Lower half of 32‑bit value (bytes 1‑0)
•
40194
– Upper half of 32‑bit value (bytes 3‑2)
`
Enter the password to enable remote operation. The password does not need to be resent unless RemLink
or RemEdit timeouts are registered or settings are saved.
`
Each Modbus transaction resets the timeout timer. (See
).
5. Continue with data reading and writing.
Note:
If during reading parameter values, a long enough communication pause causes a Remote Link timeout,
need to be repeated.