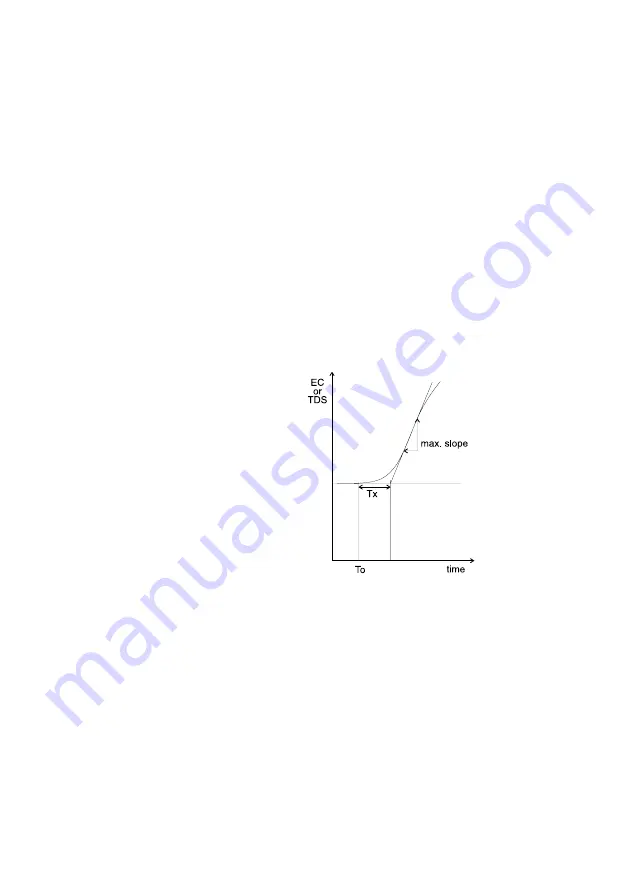
22
Note
User can disable the derivative and/or integrative action (for P or PI controllers) by
setting Td = 0 and/or Ti = MAX (Ti) respectively through the setup procedure.
SIMPLE TUNING PROCEDURE
The following procedure uses a graphical technique of analyzing a process response
curve to a step input.
1. Starting from a solution with an EC or TDS value quite different from the dosed liquid,
turn on the dosing device at its maximum capacity without the controller in the loop
(open loop process). Note the starting time.
2. After some delay (T
0
) the EC or TDS starts to vary. After more delay, the EC or TDS
will reach a maximum rate of change (slope). Note the time that this maximum slope
occurs and the EC or TDS value at which it occurs. Note the maximum slope in EC or
TDS per minute. Turn the system power off.
3. On the chart draw a tangent to the maximum slope point until intersection with the
horizontal line corresponding to the initial EC or TDS value. Read the system time
delay Tx on the time axis.
4. The deviation, Ti and Td can be calculated from the following:
• Deviation = Tx * max. slope (EC/TDS)
• Ti = Tx / 0.4 (minutes)
• Td = Tx * 0.4 (minutes).
5. Set the above parameters and restart the system with the controller in the loop. If the
response has too much overshoot or is oscillating, then the system can be fine-tuned
slightly increasing or decreasing the PID parameters one at a time.