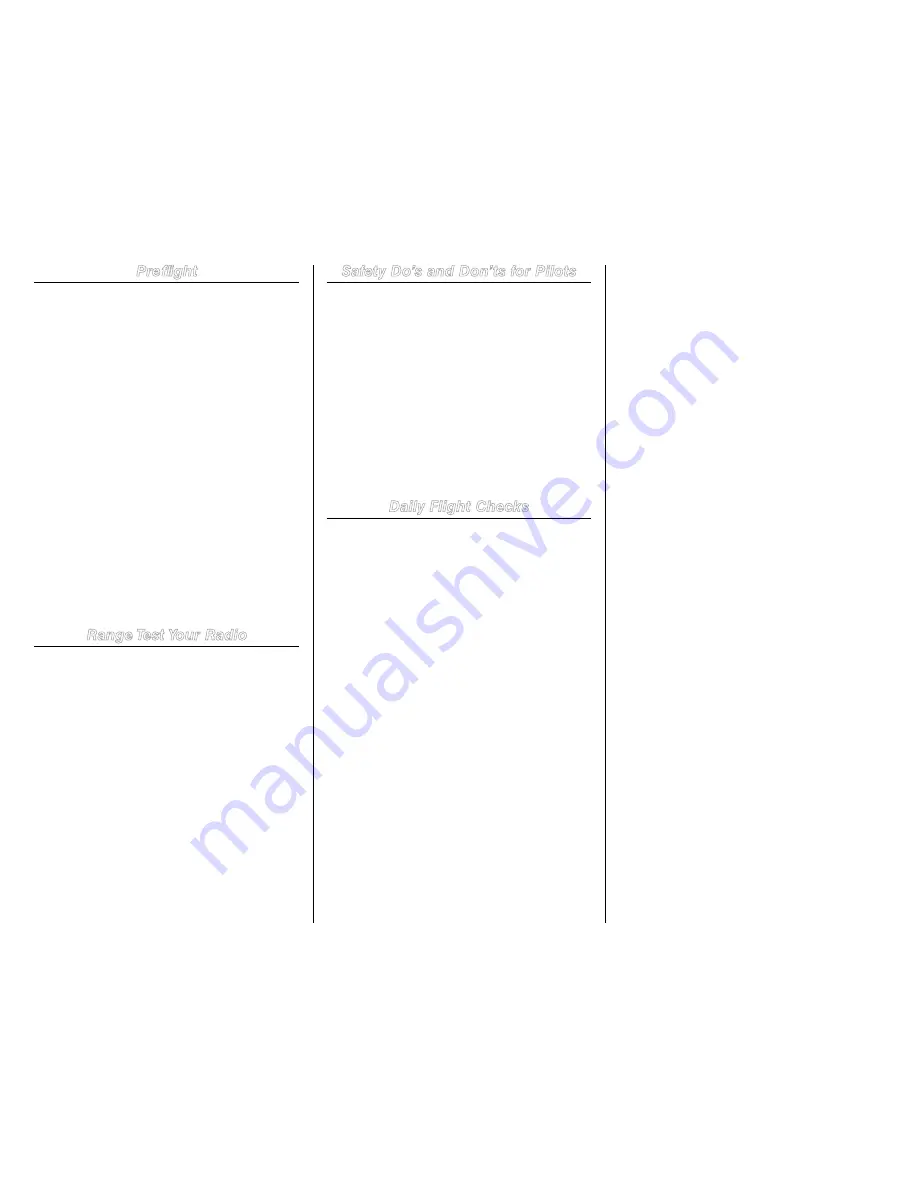
39
35% Extra 300 ARF Assembly Manual
Preflight
Check Your Radio
Before going to the field, be sure your batteries are
fully charged per your radio’s instructions. Charge the
transmitter and motor battery for your airplane. Use the
recommended charger supplied with your particular radio
system, following the instructions provided with the radio.
In most cases, the radio should be charged the night before
going out flying.
Before each flying session, be sure to range check your
radio. See your radio manual for the recommended
range and instructions for your radio system. Each radio
manufacturer specifies different procedures for their radio
systems. Next, run the motor. With the model securely
anchored, check the range again. The range test should not
be significantly affected. If it is, don’t attempt to fly! Have
your radio equipment checked out by the manufacturer.
Double-check that all controls (aileron, elevator, rudder and
throttle) move in the correct direction.
Check the radio installation and make sure all the control
surfaces are moving correctly (i.e., the correct direction and
with the recommended throws).
Check all the control horns, servo horns, and clevises to
make sure they are secure and in good condition.
Range Test Your Radio
Before each flying session, and especially with a new model,
it is important to perform a range check. It is helpful to have
another person available to assist during the range check. If
you are using a Spektrum transmitter, please refer to your
transmitter’s manual for detailed instructions on the range
check process.
Safety do’s and don’ts for Pilots
• Check all control surfaces prior to each takeoff.
• Do not fly your model near spectators, parking areas or
any other area that could result in injury to people or
damage of property.
• Do not fly during adverse weather conditions. Poor
visibility can cause disorientation and loss of control of
your aircraft. Strong winds can cause similar problems.
• Do not take chances. If at any time during flight
you observe any erratic or abnormal operation, land
immediately and do not resume flight until the cause of
the problem has been ascertained and corrected. Safety
can never be taken lightly.
• Do not fly near power lines.
daily Flight Checks
• 1. Check the battery voltage of the transmitter battery.
Do not fly below the manufacturer’s recommended
voltage. To do so can crash your aircraft.
When you check these batteries, ensure you have the
polarities correct on your expanded scale voltmeter.
• 2. Check all hardware (linkages, screws, nuts, and bolts)
prior to each day’s flight. Be sure that binding does not
occur and that all parts are properly secured.
• 3. Ensure all surfaces are moving in the
proper manner.
• 4. Perform a ground range check before each day’s
flying session.
• 5. Prior to starting your aircraft, turn off your
transmitter, then turn it back on. Do this each time you
start your aircraft. If any critical switches are on without
your knowledge, the transmitter alarm will sound a
warning at this time.
• 6. Check that all trim levers are in the proper location.
• 7. All servo pigtails and switch harness plugs should be
secured in the receiver. Make sure the switch harness
moves freely in both directions.