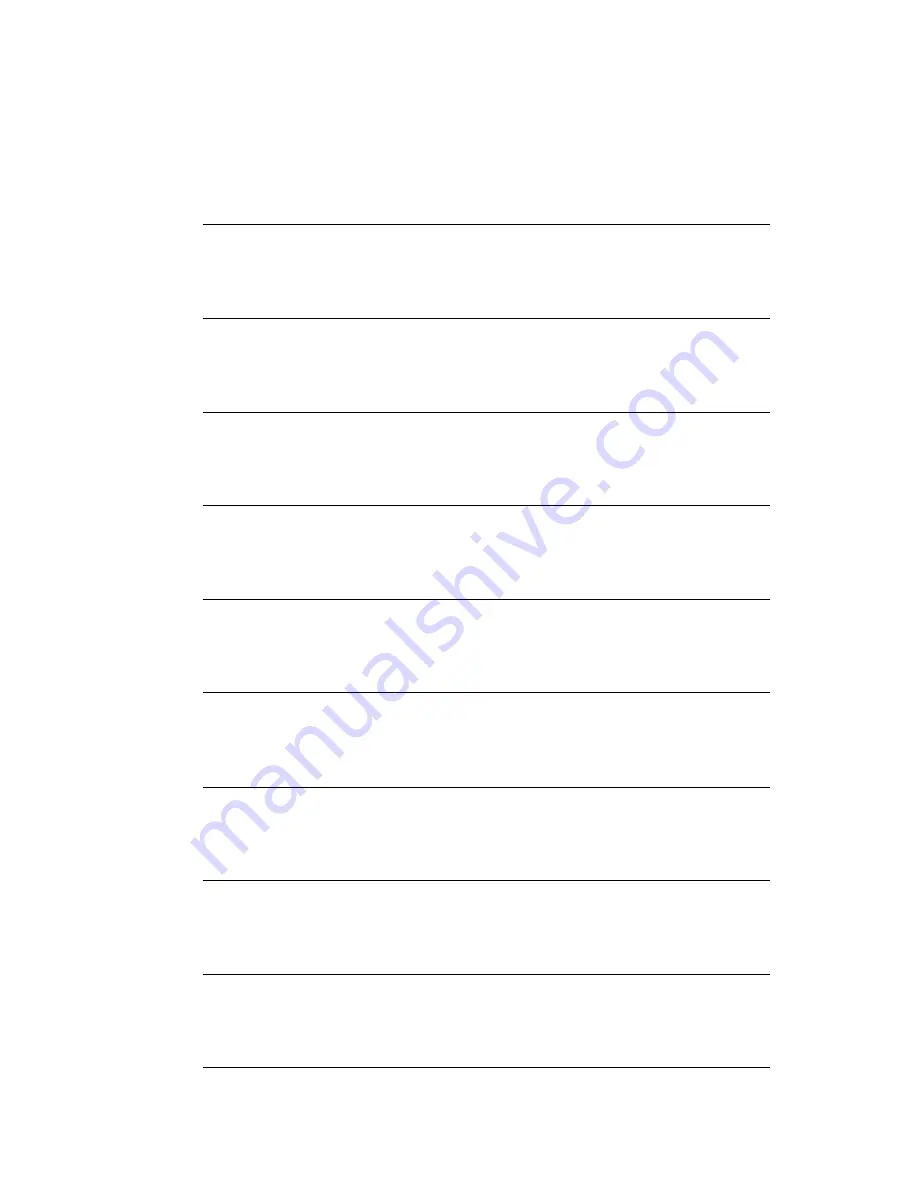
TO PREVENT SERIOUS INJURY OR DEATH
NEVER OPERATE THIS UNIT UNLESS EMERGENCY STOP FUNCTIONS PROPERLY
W A R N I N G
-10-
1. Pushing the emergency stop bar rearward or
pulling the trip cables will activate the stop to
disengage position.
2. Activating emergency stop only stops box
functions. The PTO shaft will continue to rotate.
3. Keep excessive slack out of trip cables.
4. Trip emergency stop occasionally, and when
starting the unit after periods of storage to
insure proper function.
5. To reset, move lever (A) clockwise to engage
position.
UNLOADING - FRONT UNLOAD
1. Park forage box on level ground whenever
possible during unloading. Lock tractor parking
brake.
2. Connect PTO to tractor, locking securely in
place. USE 540 PTO ONLY.
3. Engage PTO.
4.To engage cross conveyor INTERMITTENTLY,
rotate clutch lever (A) clockwise and hold with
hand pressure. If hand pressure is removed,
the cross conveyor will stop.
5.To engage the cross conveyor CONTINUOUSLY,
rotate clutch lever (A) clockwise until it locks in
the engaged position. Cross conveyor speed is
controlled by tractor RPM only.
A B
6. Quickly engaging/disengaging beaters (lever B) will allow beaters to clear material a little at a time to
avoid exceeding blower capacity.
7. When beaters are clear of material, move control lever (B) to apron speed positions. Variable speed
drive offers you a number of unloading speeds to choose from. With experience and depending on the
type of forage, you will be able to select a speed which will match your blower capacity.
Unloading speed may also be varied by increasing or decreasing engine speed of tractor.
PIN MUST BE IN END OF
DESIRED UNLOADING ONLY.
INSERT PIN UNTIL FLUSH.
TURN CLOCKWISE UNTIL LOCKED.
INSERT QUICK PIN TO
LOCK IN POSITION.
31300
FIGURE 12
CROSS CONVEYOR CLUTCH - BELT DRIVE
-
51
-
ITEM
PART NO.
DESCRIPTION
2.
S335
Front Clutch Plate
3.
S341
Idler-Stop Assembly
4.
S337
Handle Lever
5.
S332
Drive Belt Set
6.
S342
Pulley
7.
S339
Handle Mount
8.
S343
Shifting Rod
9.
11S19
Sprocket 50B20
10.
S340
Tightener Pivot Shaft
11.
S338
Handle Lever
12.
4C7
Bearing Flange
13.
X85
Bearing Flange Sheared
14.
K156
Idler Pulley
15.
S458
Input Pulley Shaft
16.
4C8
Bearing
17.
S347
Shifter Rod End
18.
23N211
Spring 5/8’’
19.
X111
3/8’’ x 1’’ Bolt GR.5
20.
BFR320
3/8’’ x 1-3/4’’ Bolt GR.2
21.
S352
Internal Star Washer
22.
K60
3/8’’ Nut
23.
B68
3/8’’ Lockwasher
24.
S355
3/8’’ Jam Nut
25.
K25
3/8’’ Locknut
26.
16SV91
1/2’’ x 3-1/4’’ Bolt GR.5
27.
R11
1/2’’ Top Locknut
28.
5B10
1/4’’ x 1’’ Woodruff Key
29.
---
3/8’’ Setscrew
30.
---
5/16’’ Setscrew
31.
A14
3/8’’ Nylock Nut
32.
X67
3/8’’ Flatwasher
33.
S344
Clutch Rod Slide
34.
S348
Spring Bracket
35.
S349
Drive Pulley Shaft
36.
S438
Clip Pin
37.
4C9
Bearing Lock Collar
38.
S345
Spacer (.074) (As Needed)
39.
K99
Spacer, 7/8’’
40.
BFR335
5/16’’ x 2’’ Expansion Pin
41.
K68
1/2’’ Flat Washer
Spacer, 9/16’’
Spacer, 1/2’’
Cable Clamp
Thimble
42.
23N94
43.
K106
44.
BFR220
45.
ES4
46.
ES5
Cable Compression Sleeve
47.
S361
Stop Cable Stiffener
48.
S358
Emergency Stop Cable
49.
S362
Handle Lever Grip
50.
S369
Spring, 3/4’’
51.
ES7
Hair Pin
52.
R35
1/2” Lock Washer (As Needed)
53.
S135
1/4” x 1-1/4” Square Key
Summary of Contents for HDNR 7+4
Page 3: ......
Page 4: ......
Page 6: ...INTENTIONALLY LEFT BLANK 4...
Page 13: ...11...
Page 34: ...32 FIGURE 2...
Page 36: ...34 FIGURE 3...
Page 38: ...36 FIGURE 4...
Page 40: ...38 FIGURE 5...
Page 42: ...40 FIGURE 6...
Page 44: ...FIGURE 7 42...
Page 46: ...44 FIGURE 8...
Page 48: ...46 FIGURE 9...
Page 52: ...50 FIGURE 12...
Page 54: ...52 FIGURE 13...
Page 58: ...56 SERVICE NOTES...
Page 59: ......
Page 60: ...H S MFG CO products approved for the FEMA SEAL OF QUALITY...