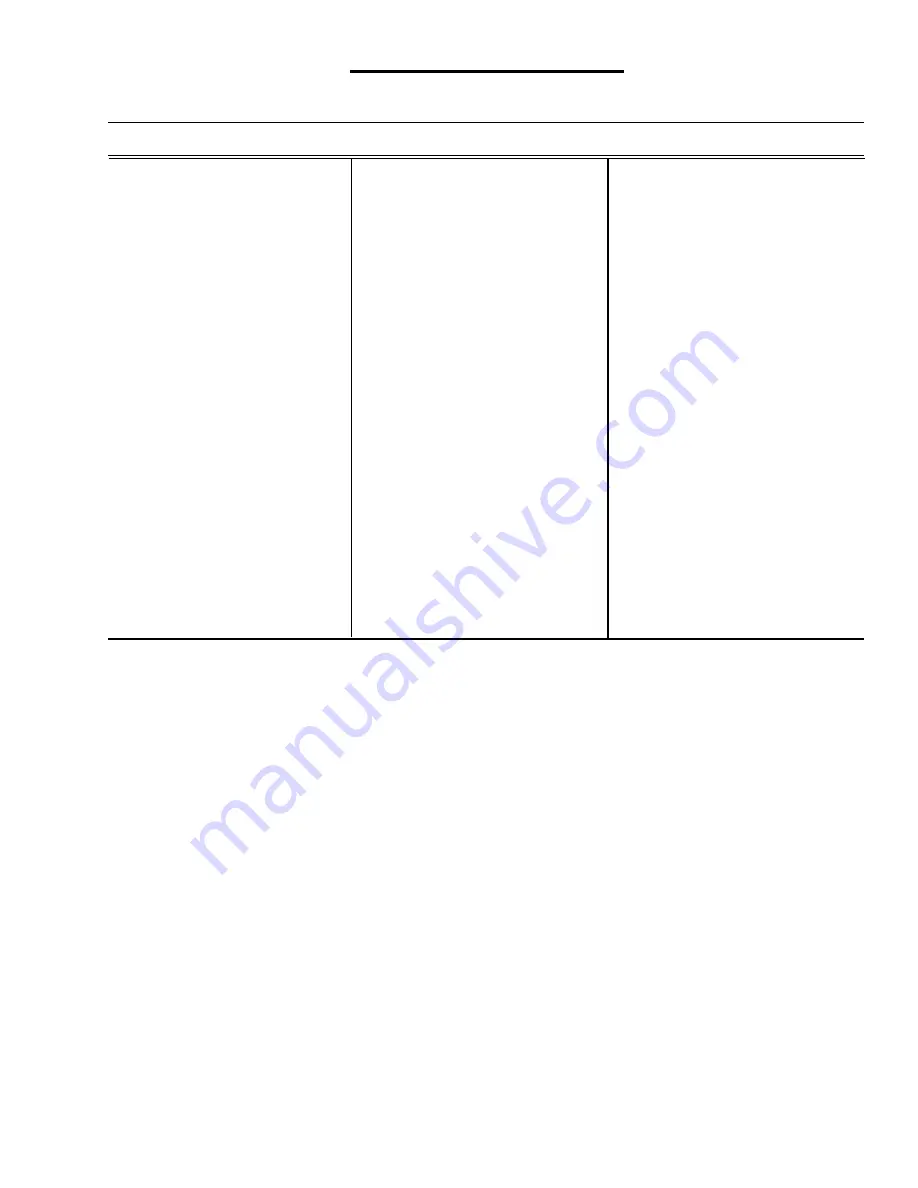
TROUBLESHOOTING
HYDRAULICS
PROBLEM
CAUSE
REMEDY
Intake Auger turns too slow.
Excessive or wet grain.
Not enough oil flow to hydraulic
pump.
Hydraulic pump defective.
Hydraulic motor defective.
SIA relief valve pressure set too
low.
SIA auger partially plugged.
SIA pressure relief valve doesn’t
function properly.
The higher the moisture content
and weight of the material that is
being conveyed, the more power
it takes. Adjust the variable speed
control valve to allow more oil to
the hydraulic motor.
Change oil filter, replace oil with
new oil and fill to proper level.
Replace hydraulic pump.
Repair or replace hydraulic motor.
Check pressure to valve, if
pressure is low adjust to factory
setting or replace if will not adjust.
Remove plugging material.
Check pressure to valve, if it will
not adjust to the factory setting,
replace the valve.
-50-
Summary of Contents for 9117
Page 3: ...1...
Page 5: ...Remove Copy At Perforation 3...
Page 6: ...Intentionally Left Blank 4...
Page 8: ...6 Intentionally Left Blank...
Page 10: ...8 Intentionally Left Blank...
Page 14: ...SAFETY INFORMATION 12...
Page 15: ...SAFETY INFORMATION 13...
Page 17: ...15...
Page 18: ...HYDRAULIC FITTING TORQUE SPECIFICATIONS 16...
Page 19: ...17 HYDRAULIC FITTING TORQUE SPECIFICATIONS...
Page 46: ...DECAL LOCATION 44 1494P 82907A 093020 093020 82907B 093020 82907G 82907L 9194A 82907G...
Page 53: ...SERVICE NOTES 51...
Page 54: ...SERVICE NOTES 52...
Page 55: ......
Page 56: ...H S MFG CO products approved for the FEMA SEAL OF QUALITY...