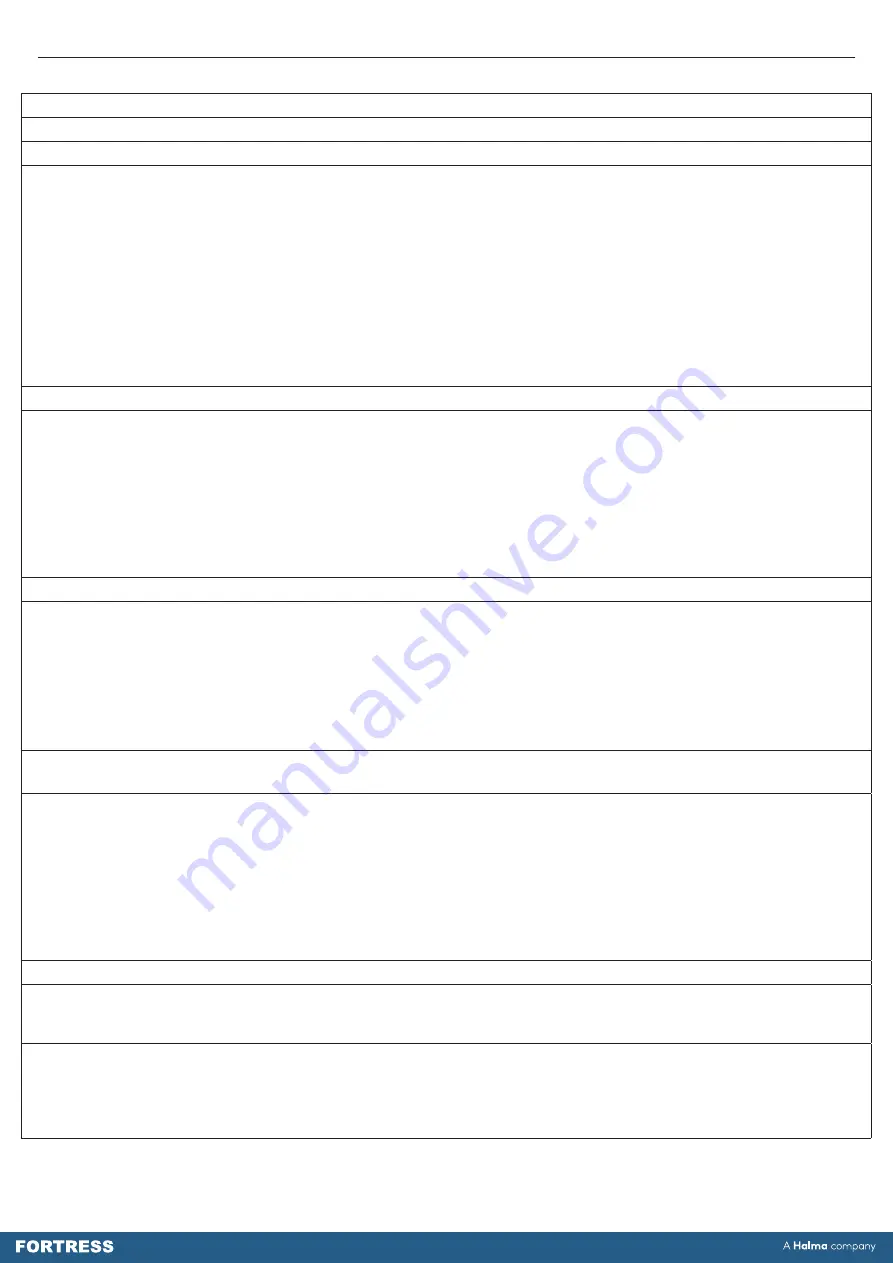
Operating Instructions: Alfred Solenoid Controlled Guard Lock
14
Mounting and Installation Instructions
Mechanical Mounting and Installation
Tools and Fixings Required
• Up to 4 x M8 screws
for securing Actuator assembly.
• 1 x M8 screw
for securing Head Module.
• Up to 6 x M8 screws
for securing Key Adaptor assemblies.
• 4 x M8 screws
for securing Ex Rated Solenoid Module.
◦
All screws must be suitable length for a minimum of 10mm thread engagement.
◦
All screws must be security type to prevent unauthorised removal or tampering.
◦
All screws must be of type A2-70 Stainless Steel.
◦
Required torque setting; 25 Nm.
• Driver suitable for securing M8 screws.
• TX40 Driver Bit
(provided).
• Adhesive Threadlocker to secure mounting fixings from loosening due to vibration.
◦
Threadlocker must be ‘middle strength’ or greater.
Mounting
1.
Locate the complete Alfred Solenoid Controlled Guard Lock product so that is in a suitable position for full
operation and functionality and is within reach for easy user operation.
2.
Secure the Actuator assembly to the Door / Gate of the guarded area (See Figures 4, 5 & 6 for location of
mounting hole positions).
3.
Secure the remainder of the complete Alfred Solenoid Controlled Guard Lock, including the Ex rated Solenoid
module, using M8 screws fixed into the rear of the product. (See Figures 2 & 3 for location of mounting hole
positions).
4.
Perform Mechanical Function tests before completing installation and commission. See Mechanical Function test
section for more details.
General mounting requirements and cautionary notes:
• Mount the complete Alfred Solenoid Controlled Guard Lock product in the correctly assembled condition.
• All mounting surfaces should be flat and stable.
• The complete Alfred Solenoid Controlled Guard Lock product must be located so that all scheduled inspection and
maintenance procedures are all easily possible.
• All fixing screws used to mount the complete Alfred Solenoid Controlled Guard Lock product must be permanently
prevented from removal. If mounting fixings are visible, they must be secured against removal by personnel using standard
tools, manipulation and un-authorised or un-identifiable removal. If mounting fixings are not visible or hidden, they must be
secured against removal or loosening due to vibration. In both cases, a middle strength adhesive threadlocker is required.
Additional mounting requirements if Alfred Solenoid Controlled Guard Lock product is used for Machine
Guarding:
• The Alfred Solenoid Controlled Guard Lock product must not be used as a mechanical stop. Where applicable, precautions
must be made to ensure the door or gate of any guarded area has sufficient support and stops to prevent the impact on the
product.
• The complete machine guarding installation must conform to all relevant design, construction and installation standards and
guidelines.
• Any gap around the perimeter of the machine and guarding when under operation (Safety Outputs High) must not exceed
the limits specified in ISO 13857 & ISO 14120.
• The installation and operation of the complete Alfred Solenoid Controlled Guard Lock product must take into account the
requirements of EN ISO 14119; in particular Section 7 – Design for minimising defeat possibilities.
Lid Assembly Requirements
During electrical wiring and installation, the lid of the Ex Rated Solenoid Module needs to be removed for access. Care must
be taken during Lid dis-assembly and re-assembly in order to maintain Ingress Protection (IP) level and maintain enclosure
protection levels of ATEX and IECEx ratings.
To remove the Lid assembly from the Ex Rated Solenoid Module;
1.
Remove the 10 x M8 Torx screws securing the Lid assembly to the Solenoid Switch enclosure using the supplied TX40
driver bit.
2.
Lift off the Lid Assembly.
3.
Set Lid Assembly aside safely to protect internal gasket assembly.