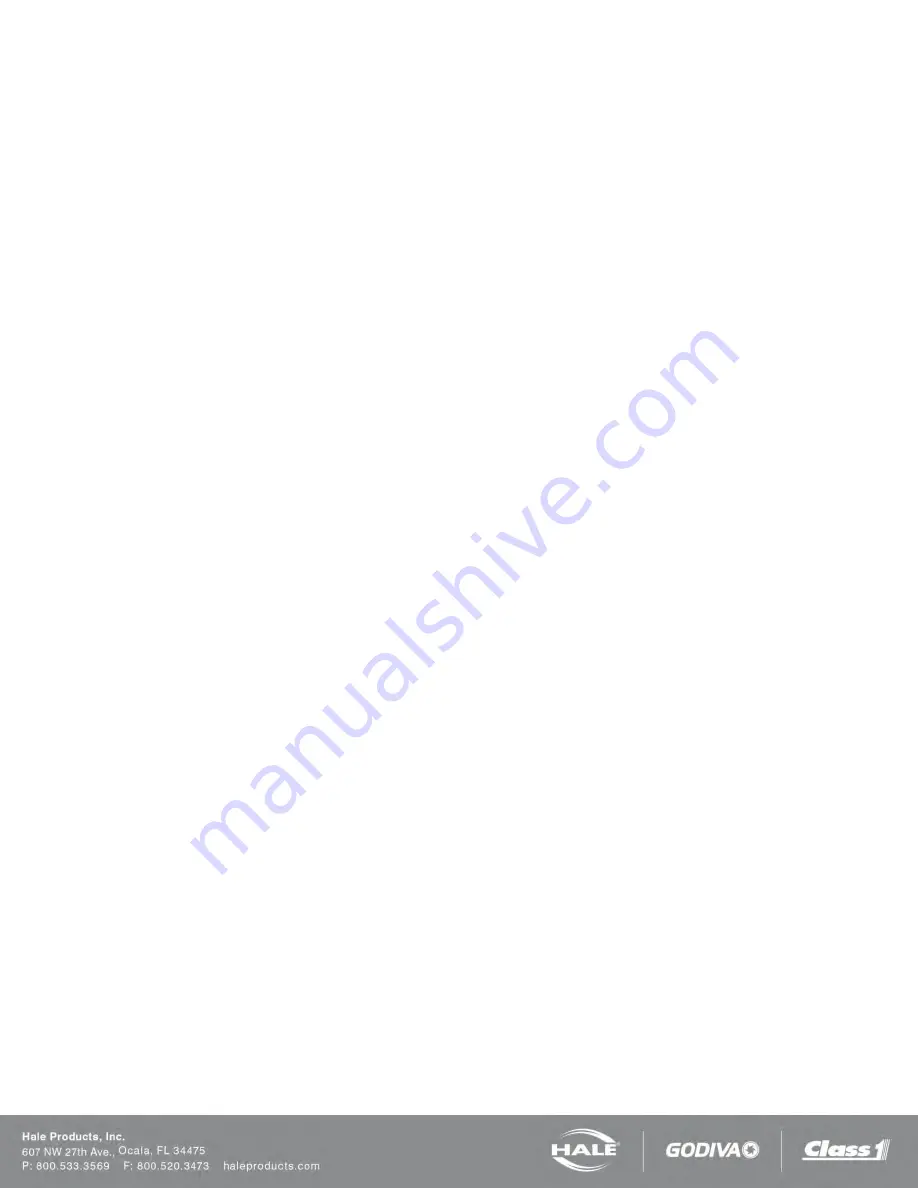
Page
71
SmartFOAM
START-UP CHECKLIST
Before energizing the apparatus and Hale SmartFOAM system for the first time, make sure the following items are
checked:
ELECTRICAL
❑
Tank level sensor wires connected to distribution box and sealed from moisture.
❑
Tank level sensor functions properly.
❑
Control cable connection at distribution box correct and tight.
❑
Flow sensor cable properly connected.
❑
All cables and wires are secured and protected from damage during operation.
❑
Control and flow sensor cables properly folded and secured; radio antennas, power lines and equipment away
from cables.
❑
Foam pump and motor assembly properly grounded using flat ground strap.
❑
Correct voltage provided. Direct current, negative (–) ground.
❑
Adequate current available (see
Table 2: Specifications – 1.7 and 2.1
Table 3: Specifications – 3.3 and 5.0
).
Main power direct to battery, battery switch or properly sized solenoid without primer or other accessories tied in.
❑
Correct motor voltage (provided by the converter, 24V) when installing the 501-4480-06-0 system on a 12V appa-
ratus. Converter output current, negative (–) ground.
❑
Motor voltage (provided by the converter, 24V, when installing the 501-4480-06-0 system on a 12V apparatus)
NOT connected anywhere other than motor.
❑
Primary electrical and ground connections tight and protected from corrosion with silicone sealant.
❑
Splices in wires sealed from moisture using adhesive filled heat shrink tubing.
LIQUID
❑
Flow sensor mounted with flow arrow in the correct direction for water flow.
❑
Check valves are properly mounted in water and foam concentrate lines.
❑
Strainer mounted for proper concentrate flow direction in foam tank to pump hose.
❑
Foam tank to foam pump valve is in place and open.
❑
Check valve/injector fitting lines are proper size and connections are tight.
❑
Bypass valve is properly mounted and oriented for direction of concentrate flow.
❑
Foam concentrate gravity feeds to foam pump from foam concentrate tank.
❑
All hoses free of kinks and sharp bends.
❑
No sharp bends that can trap air exist in system.
❑
Flush water connections correct and tight.
❑
Discharge piping hydro tested in accordance with NFPA/UL requirements.
❑
Bypass valve handle is in the INJECT position.
FOAM PUMP
❑
Foam pump and motor assembly mounted in horizontal position with base plate down.
❑
Foam pump and motor assembly properly secured using proper mounting hardware.
❑
Foam pump suction and discharge hoses connected to proper ports.
❑
Foam pump suction and discharge hose fittings tight.
Summary of Contents for SmartFOAM
Page 3: ...Page 2 SmartFOAM NOTES...
Page 16: ...Page 15 SmartFOAM SYSTEM DIAGRAM Figure 6 Typical Hale SmartFOAM 2 1A and 1 7AHP System...
Page 17: ...Page 16 SmartFOAM Figure 7 SmartFOAM 3 3 5 0 6 5 Single Tank System with In line Strainer...
Page 18: ...Page 17 SmartFOAM Figure 8 SmartFOAM 3 3 5 0 6 5 Single Tank withMSTandIn lineStrainer...
Page 19: ...Page 18 SmartFOAM Figure 9 SmartFOAM 3 3 5 0 6 5 Single Tank withMSTandFSSeriesStrainer...
Page 20: ...Page 19 SmartFOAM Figure 10 SmartFOAM 3 3 5 0 6 5 Dual Tank withMDTIIandIn lineStrainers...
Page 21: ...Page 20 SmartFOAM Figure 11 SmartFOAM 3 3 5 0 6 5 Dual Tank withMDTIIandFSSeriesStrainer...
Page 22: ...Page 21 SmartFOAM Figure 12 SmartFOAM 3 3 5 0 6 5 Dual Tank withADTandIn lineStrainers...
Page 23: ...Page 22 SmartFOAM Figure 13 SmartFOAM 3 3 5 0 6 5 Dual Tank withADTandFSSeries Strainers...
Page 48: ...Page 47 SmartFOAM Figure 28 Typical 4 Inch Check Valve Installation Midship Pump...
Page 59: ...Page 58 SmartFOAM Figure 43 ADT Option Air Hose Connections Part 2...
Page 68: ...Page 67 SmartFOAM Figure 55 Top Mount Low Level Sensor Assembly...
Page 77: ...Page 76 SmartFOAM NOTES...
Page 90: ...89 Page 89 SmartFOAM NOTES...